ANSYS|基于Workbench的液压油路管强度研究
2016-10-21 by:CAE仿真在线 来源:互联网
导读:本文通过研究各直径油路管在不同交叉角度下的应力分布,分析液压控制壳体中油路管交叉角度对油路管内壁强度的影响。
液压驱动装置体积小、重量轻、结构紧凑、操纵控制简便,易于实现过载保护,在各个领域中得到广泛应用和发展。特别是在航空领域,液压驱动装置起着举足轻重的作用。
飞机起落架的滑行、起飞;舱门的打开与关闭、军用飞机上导弹的投放等都是由液压驱动装置控制实现。所以液压驱动装置可靠性运行显得非常突出和重要。同时航空产品对产品重量的要求也是相当苛刻。
液压控制壳体作为液压驱动装置中控制和调节液体压力、流量和方向的控制元件当然是整个装置中的重中之重。
液压控制壳体中,各油路纵横交错,既要保证液压驱动装置的可靠运行,不能发生油路管漏油、破裂等故障又要将产品重量降到最小,这就涉及到油路管强度校核和最小壁厚的问题。
本文重点研究液压油路管交错角度对强度的影响及不同直径油路管对应的最小壁厚,为液压驱动装置的设计及减重提供参考。
对直径为6mm、10mm、20mm油路管分别在相交30度、45度、90度时的强度进行有限元分析。对各个几何模型采用相同大小网格处理,将油路管交叉处网格细化,以提高计算精度。施加油压 42 MPa,计算得到各直径下不同交叉角度时的油路管在相同油压下的最大应力。
1.1直径10mm油路管相交30度的强度分析
直径10mm油路管相交30度在 42 MPa 油压下的应力分布如图1所示。最大应力出现在两油路管相交处,最大应力为544.75 MPa。
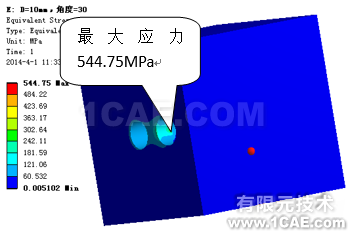
图1 直径10mm油路管相交30度应力分布图
1.2直径10mm油路管相交45度的强度分析
直径10mm油路管相交45度在 42 MPa 油压下的应力分布如图2所示,最大应力出现在两油路管相交处,最大应力为352.04 MPa。
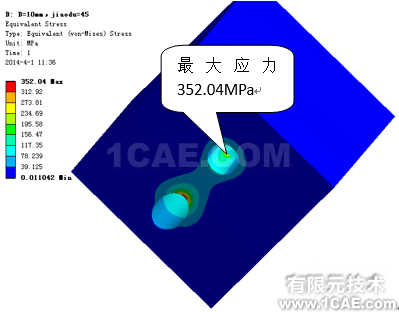
图2 直径10mm油路管相交45度时应力分布图
1.3直径10mm油路管相交45度的强度分析
直径10mm油路管相交90度在 42 MPa 油压下的应力分布如图3所示,最大应力出现在两油路管相交处,最大应力为177 MPa。
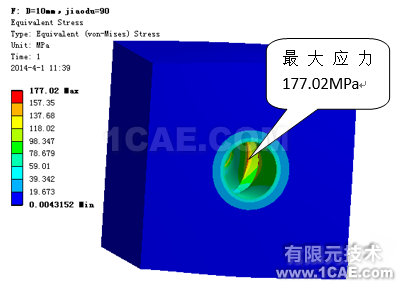
图3 直径10mm油路管垂直相交时应力分布图
直径6mm油路管、直径20mm油路管相交30度、45度、90度时的应力分布与直径10mm油路管应力分布相同,最大应力均出现在油路管相交处。两个油路管45度相交时,油路管口壁厚较薄,应力也较大,如图2所示。
表1 不同直径、不同角度油路管42MPa油压下的最大应力
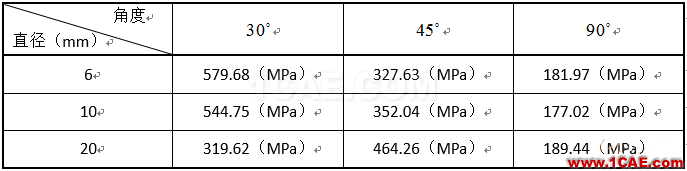
通过上表可以看出,相同直径油路管在不同角度下的应力不同,两油路管相交角度越大,应力越小。无论油路管直径多大,两管垂直相交,应力最小。
本节主要研究在内压作用下油路管的屈服失效、爆裂失效以及疲劳强度。油路管内压屈服失效的基本原理是内壁发生屈服即失效,但内压屈服并不丧失密封完整性和结构完整性,内壁屈服在实际试验中和现场应用中都体现不出来,屈服失效准则较严酷。
爆裂能真实的体现油路管丧失密封完整性,采用抗拉强度校核。本文中对油路管内壁采用抗拉强度校核,最小壁厚外壁处采用屈服失效准则校核。为了与实际更接近,本文采用一端堵口的油路管进行有限元模拟。
爆破试验油压一般为 70 MPa ,材料取7A04-H112,对直径 6 mm、10 mm、15 mm、20 mm 油路管的最小壁厚进行研究。
2.1材料参数
表2 材料性能参数

2.2各直径油路管对应最小壁厚研究
2.2.1直径6mm油路管最小壁厚1.2mm
直径6mm、壁厚1.2mm油路管在70MPa爆破油压下最大应力为314.2MPa,壁厚1.2mm处的最大应力为253.32MPa,应力分布如图4所示。
图4 直径6mm、壁厚1.2mm油路管应力分布图
表3 直径6mm、壁厚1.2mm油路管静强度计算结果
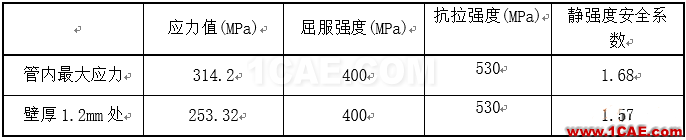
2.2.2直径10mm油路管最小壁厚2mm
直径 10mm 、最小壁厚 2mm 油路管在 70MPa 油压下最大应力为 319.67MPa,最小壁厚2mm处最大应力为 259.14MPa ,应力分布如图5所示。
图5 直径10mm、壁厚2mm油路管应力分布图
表4 直径10mm、壁厚2mm油路管静强度计算结果

2.2.3直径15mm油路管最小壁厚3mm
直径15 mm、最小壁厚3mm油路管在70 MPa油压下最大应力为392.45 MPa,最小壁厚3mm处最大应力为260.39 MPa,应力分布如图6所示。
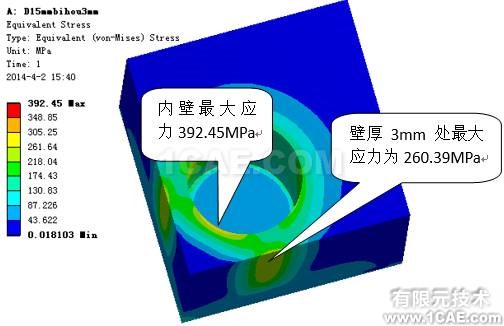
图6 直径15mm、壁厚3mm油路管应力分布图
表5 直径15mm、壁厚3mm油路管静强度计算结果
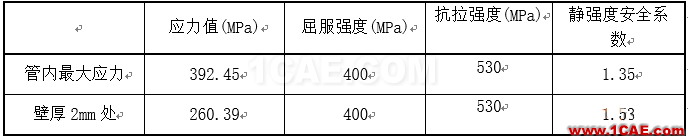
2.2.4直径20mm油路管最小壁厚4mm
直径 20mm、最小壁厚 4mm 油路管在 70 MPa油压下最大应力为444.19MPa,最小壁厚4mm处最大应力为262MPa,应力分布如图7所示。
图7 直径20mm、壁厚4mm油路管应力分布图
表6 直径20mm、壁厚4mm油路管静强度计算结果
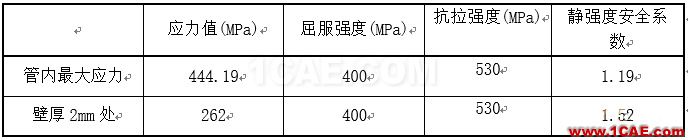
2.3各油路管最小壁厚静强度计算结果
各直径油路管对应最小壁厚下的静强度计算结果如表7所示。
表7 各直径油路管静强度计算结果
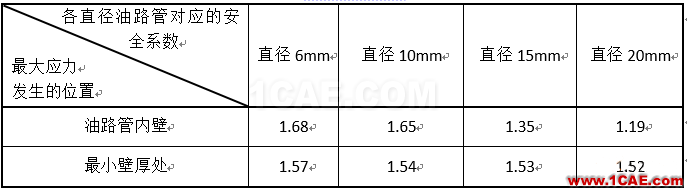
由上表可以看出,各直径油路管在 70 MPa 爆破油压下,内壁安全系数均大于1,即内壁均未发生爆裂破坏;各直径油路管最小壁厚处的静强度安全系数均大于1.5,说明最小壁厚处均未发生屈服失效且留有一定安全余量。因此可以得出结论:直径小于20mm油路管对应的最小壁厚为油路管直径的20%。
2.4各油路管最小壁厚疲劳强度计算
表8 各油路管疲劳强度计算
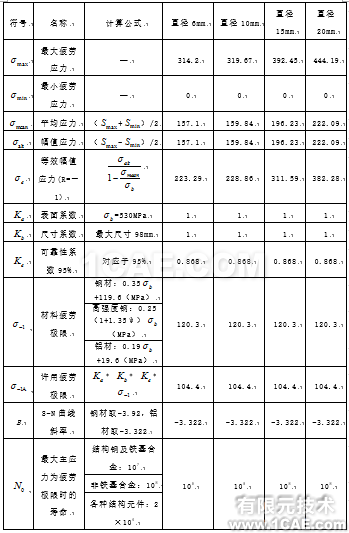
由上表可知,各直径油路管在 70 MPa 爆破油压下的安全寿命分别为2.0E+6 次、1.825E+6 次、6.5E+5 次和3.25E+5 次。由此表明各直径油路管在压力脉冲循环次数小于3.25E+5次时其对应的最小壁厚均满足疲劳强度。
本文基于ANSYS Workbench分别对油路管不同交叉角度对其强度的影响和不同直径对应最小壁厚的规律进行研究,可以得出以下结论:
(1)无论油路管直径多大,交叉角度为90度时,油路管内壁交叉处应力最小,油路管内壁不易发生磨损、漏油等;
(2)油路管直径小于20mm时,其对应的最小壁厚为直径的20%,既能满足爆破油压下的静强度要求,又能满足循环次数低于325000次的疲劳寿命要求,为液压控制壳体的设计和减重提供理论参考。
相关标签搜索:ANSYS|基于Workbench的液压油路管强度研究 Ansys有限元培训 Ansys workbench培训 ansys视频教程 ansys workbench教程 ansys APDL经典教程 ansys资料下载 ansys技术咨询 ansys基础知识 ansys代做 Fluent、CFX流体分析 HFSS电磁分析 Abaqus培训