基于DOE技术的某牵引车横梁优化分析
2016-11-28 by:CAE仿真在线 来源:互联网
随着物流业的快速发展,牵引车也向着高速重载方向发展,由于车辆工作的多工况,车辆结构受力复杂,因此经常在使用过程中发生车架结构早期断裂破坏。这种现象已经成为困扰汽车设计部门的难题,并造成了明显的经济损失。
目前在车架强度研究方面普遍采用的方法为试验方法和计算机仿真方法。试验方法是一种直接而客观的设计与验证方法,结果最有说服力,但是试验周期较长,费用昂贵且重复性差,而且也不可能采集到足够多的数据,特别是用于产品改进所需的详细数据资料;计算机仿真方法具有费用低廉、周期较短、可重复性、结果信息全面等优点。通过仿真分析,可以在短期内,可以完成多次改进分析,并以此作为产品改进的依据。从模拟仿真和试验对产品安全进行验证,能确保分析结果的可信度和结构的可靠性。
本文利用有限元软件HyperMesh建立某牵引车车架有限元模型,利用Altair OptiStruct 进行静强度计算模拟,并与实际情况进行对比,对车架横梁处存在问题进行DOE优化设计来提高横梁的强度。
本文中某牵引车车架有限元模型,网格单元平均尺寸=10mm,焊接熔核直径=6mm,焊点由面到面连接方式生成,板簧使用Spring单元和RBE2模拟,安装在车架左右两侧的油箱和电瓶箱以及驾驶室和发动机本身结构的形状对车架的有限元强度和刚度分析影响很小;但是其本身的质量很大,对车架结构的强度和刚度影响很大,根据工程经验,选择用质量点单元mass来模拟简化油箱和电瓶箱的结构,这样可以减少建模时间,提高工作效率,车架有限元模型如图1所示,车架的材料数据如表1所示。
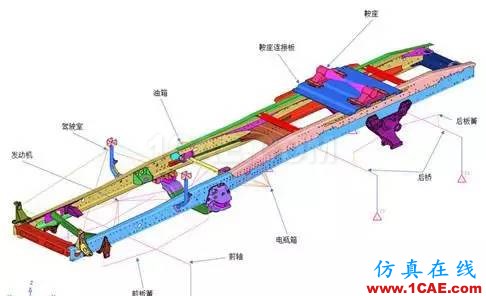
图1 车架有限元模型
表1 牵引车车架有限元模型材料参数属性

在进行静强度分析时,我们分别选择对横梁影响比较大的转向静态受力工况、扭转静态受力工况这两个典型工况为研究对象。
2.1 转向静态受力工况
车架转向受力载荷施加图如图2所示,应力云图如图3所示。
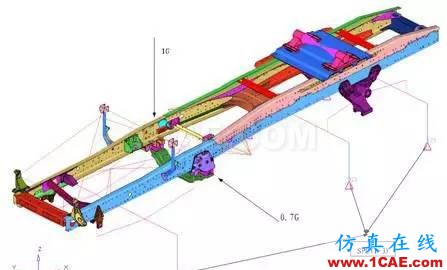
图2 车架转向受力工况载荷图
在应力云图3中我们可以看出,应力比较大的位置1处为车架横梁,也是车架真实断裂位置(车架真实断裂图如图4所示),此处的应力属于应力分布的高应力区域,根据断裂图片对比,该工况与真实情况一致。此处结构需要进行优化改进。位置2、3处应力值比较大,此处结构超过屈服极限,应当加以关注,进行适当的结构修改减少局部的应力集中。
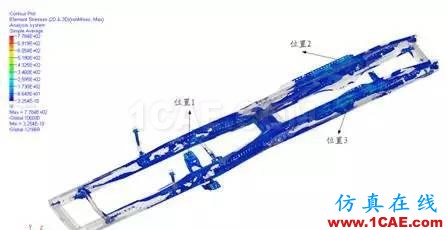
图3 车架转向受力工况应力分布云图
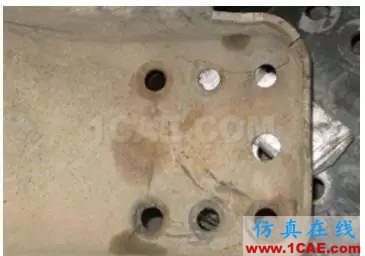
图4 车架横梁实际破坏图
2.2 扭转静态受力工况
车架转向受力载荷施加图如图5所示,应力云图如图6所示。
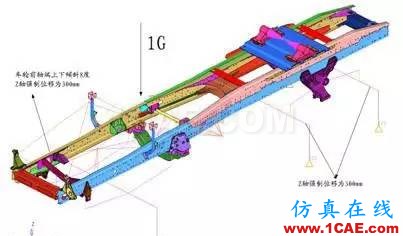
图5 车架扭转受力工况载荷图
从应力分布云图6中我们发现,位置1处为横梁最大应力值,大于材料的屈服极限,也是真实的破坏位置,应进行优化改善。位置2处为横梁应力值大于材料的屈服极限,应高度重视,极有可能产生疲劳破坏。位置3,4处应力值比较高,但是没有超过材料屈服极限,所以不会对该零件造成强度破坏。
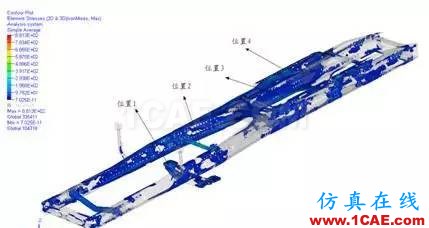
图6 车架扭转受力工况应力分布云图
DOE-Design of experiment(试验设计)主要应用在试验的合理安排和试验数据的处理上,利用数理统计学的基本知识,讨论如何合理地安排试验、取得数据,然后进行综合科学分析,从而尽快获得最优组合方案。
针对本车架横梁处强度较差的特点,本文运用OptiStruct软件对其进行了DOE优化设计,希望通过改变横梁及其加强件的厚度值,来增强部件的强度,从而达到提高整个车架的承载能力的目的,我们在横梁与车架纵梁连接处添加了两块加强板,添加加强板前后状态如图7、图8所示,加强板与横梁体铆接。
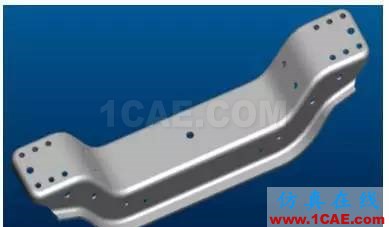
图7 横梁原始状态
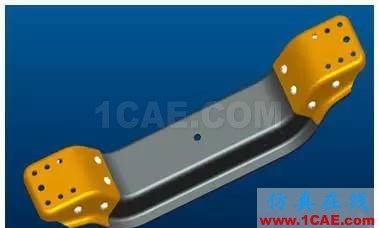
图8 横梁添加加强板状态
3.1 DOE数据分析
DOE设计中,因素水平数的选择十分关键,因为如果因素水平选取过多,将会使试验次数急剧增加,既不经济,又费时间,如果选取过少,又有可能造成无法选到主要因素的后果。我们选择对横梁影响比较大的典型工况扭转工况为研究对象,分别选用横梁厚度与加强板厚度作为试验设计的2个因素,进行交叉试验,试验次数为31次,车架的安全系数有较大的差异,如表2所示。
我们也可以从图9、图10中可以更加直观的看出横梁厚度、加强板厚度和安全系数之间的关系。
表2 扭转工况下的DOE分析数据
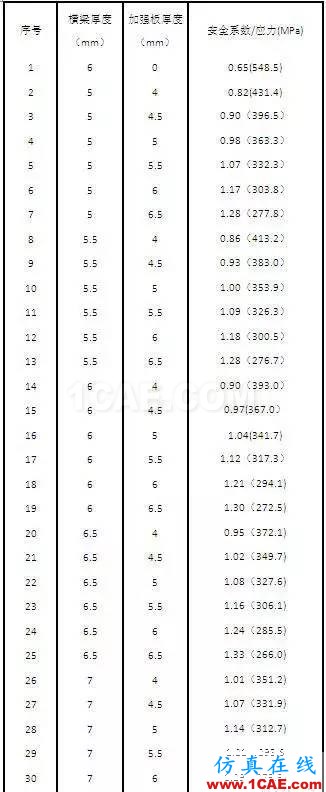

图9 扭转工况下DOE响应面图
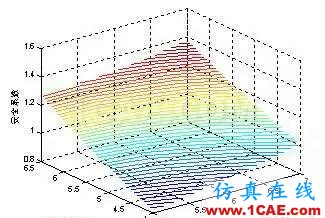
图10 扭转工况下DOE等高线图
通过DOE分析,我们可以更加全面地得到不同横梁厚度和加强板厚度之间组合横梁总成的车架安全系数。综合考虑实际工艺、模具及成本等方面的因素,原始结构状态为表2中的第1组组合,在实际生产中选择表2中第16组组合,以此进行结构的改进。
3.2 横梁结构优化前后模态对比
我们将横梁原始结构的自由模态与改进后横梁的自由模态的第一阶频率进行对比,原始结构与改进结构自由模态的第一阶频率分别如图11、图12。
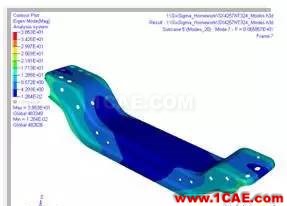
图11 原始结构第一阶频率
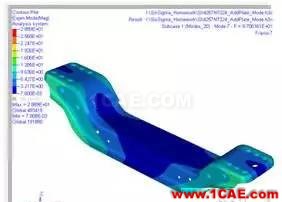
图12 改进后结构的第一阶频率
由图11、图12可以看出自由模态幅频特性:
原始结构:最大幅值:38.53;第一阶频率:80.7Hz;
改进后结构:最大幅值:28.89;第一阶频率:87.06Hz;
最大幅值降低:38.53-28.89=9.64;
基频提高:87.06-80.7=6.36(Hz)。
3.3 横梁结构优化前后应力对比
本文仍然选择对横梁影响比较大的转向受力工况和扭转受力工况为研究对象。
3.3.1 转向静态受力工况
横梁结构改进前后在转向静态受力工况时的应力云图分别如图13、图14所示。
由图13、图14可以看出最大应力幅值(安全系数):
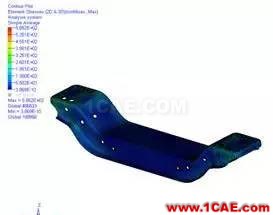
图13 原始结构应力云图
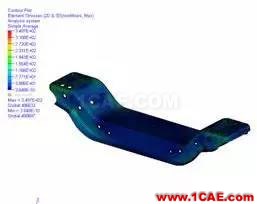
图14 改进后结构的应力云图
改善前状态:585MPa(安全系数0.61)
改善后状态:350MPa(安全系数1.02)
应力降低:585-350=235(MPa)
安全系数提高:(1.02-0.61)/1.02×100%=40.2%
3.3.2 扭转受力工况
横梁结构改进前后在扭转态受力工况时的应力云图分别如图15、图16所示。
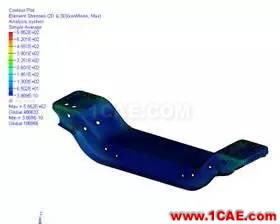
图15 原始结构应力云图
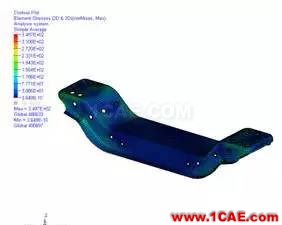
图16 改进后结构的应力云图
由图15、图16可以看出最大应力幅值(安全系数):
改善前状态:549MPa(安全系数0.65);
改善后状态:342MPa(安全系数1.04);
应力降低:549-342=207(MPa);
安全系数提高:(1.04-0.65)/1.04×100%=37.5%。
本文通过CAE软件HyperMesh建立了某牵引车的车架模型,利用Altair OptiStruct对其进行了静强度计算,得到了车架模态、应力等数值。本文采用DOE优化设计方法对车架横梁进行优化设计,优化结果表明优化方案相比初始设计方案明显降低了车车架横梁的应力,增强了车架强度,提高了车辆的承载能力,基于DOE的车架优化分析具有很强的工程实用性,对于车架结构变更设计具有巨大的指导意义。
相关标签搜索:基于DOE技术的某牵引车横梁优化分析 Ansys有限元培训 Ansys workbench培训 ansys视频教程 ansys workbench教程 ansys APDL经典教程 ansys资料下载 ansys技术咨询 ansys基础知识 ansys代做 Fluent、CFX流体分析 HFSS电磁分析 Abaqus培训