ADC12压铸过程的温度场数值模拟与 工艺参数的优化
2016-12-21 by:CAE仿真在线 来源:互联网
高压铸造属近净成形技术.被广泛地应用于航空、航天、电子和医疗等领域。目前,高压铸造是用于铸造铝合金常规的工艺,由于铝合金优异的充型性使其能够经济
地用于生产大型、薄壁和复杂铸件。压铸模具的温度场分布对模具寿命、压铸件质量、生产效率等有着至关重要的影响。一方面,模具温度场影响压铸件的充型、凝
固过程,而凝固过程的温度场分布是预测缩孔、缩松、热裂和宏观偏析等铸造缺陷的基础;另一方面,模具在压铸过程中,受到反复的急冷急热影响,模具的温度波
动较大,从而决定了其承受热应力的程度.导致一定程度的变形和裂纹,也就影响了模具的使用寿命。
为了提高铝合金压
铸件的质量和模具的使用寿命.压铸过程的温度场受到了越来越多的研究工作者和实际生产者的重视。Lee等研究得到了浇注温度和脱模剂对铸件与模具接触面的
温度场分布规律。Kaiser分析了模具的预热温度对铸件质量和模具寿命的影响。贾良荣实现了用有限差分法对压铸过程的铸件和模具温度场的模拟。因此,实
现精确的数值模拟,温度场的研究是必不可少的。本文以压铸实验为基础,针对壳状铝合金薄壁类压铸件,利ANSYS Workbench软件中热分析模块研究铝合金铸造过程中铸件和模具的温度分布规律。旨在通过观察温度的分布。研究铸件以及模具的温度变化规律,有效的预测铸件和模具热应力集中部位,以此得出更合理的工艺参数。以期达到对实际生产的指导作用。
1 实验设计
1.1 铸件、铸型以及传感器
实验为“薄壁”铸件,壁厚为4mm。铸件尺寸如图1(a)所示,铸件见图1(b)。
针对进一步提高计算效率和模拟精度。温度的采集需要较高的频率。同时一定要有距离型腔表面很近的测温点的温度值.从而保证测量结果和模拟结果的稳定性和准确性。因此,本实验采用K型热电偶,热电偶丝直径为0.5mm。置人位置如图2所示的传感器TCl、TC2、TC3、TC4。
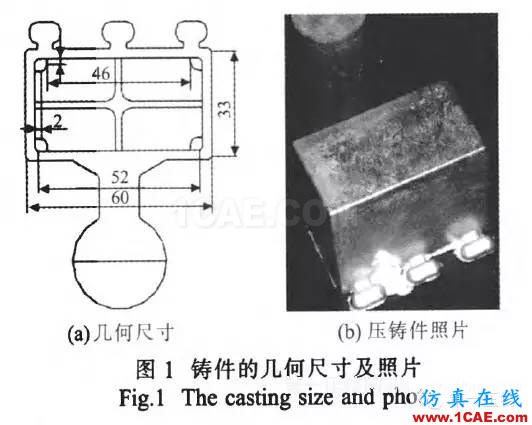
1.2 实验条件及实验过程
试验中模具材料为H13钢。铸件材料为ADCl2。表l列出了两种材料的相关热物性参数。
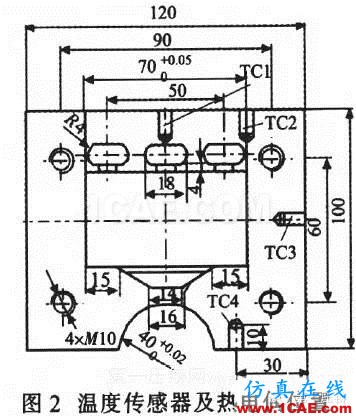
1.2 实验条件及实验过程
试验中模具材料为H13钢。铸件材料为ADC12。表l列出了两种材料的相关热物性参数。
实际压铸生产是一个复杂的周期性高速循环过程。为了便于计算,本文把压铸的一个循环过程简化为5个阶段:第1阶段为浇人液态金属、压射金属液并保压凝固;第2阶段为压回和铸件的冷却;第3阶段为开型、顶出铸件;第4阶段为模具上刷脱模剂;第5阶段为合型、等待下次浇注。
2 温度场计算的数学模型
在压铸过程中,热量的传递形式主要以热传导、对流以及辐射3种方式进行。由于能量守恒,温度场经过循环的压铸过程最终会趋于动态的平衡状态。
因此,根据Fourier导热定律,司表达出在方向流入的微元体热流量公式:

式中:r为温度,K;

为传热系数,W/(m2℃)。
同理.可表达出在方向上流出微元体的热流量公式:
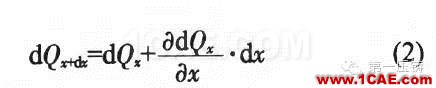
由式(1)、(2)整理得微元体吸收的净热流量:
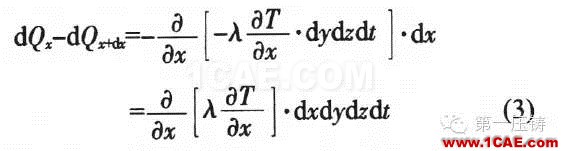
同理,微元体在y、z方向上吸收的净热流量分别为:
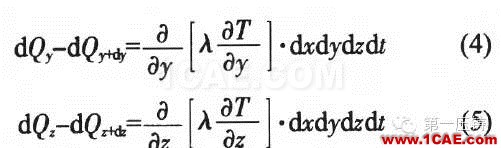
若在单位时间内,液态合金的发热量为Q,则在时间内,微元体的发热量为出d业·m。因此,在时间内微元体中的总热量变化为:

将该微分方程作适当整理化简之后。利用有限元法就可求出数值解,并将其用于研究整个压铸模的温度场分布。
3模拟结果及测量结果分析
针对合金ADC12的压铸实验共进行了56次压射,试验中改变的工艺参数有模具初始温度、浇注温度、保压时间以及高、低速压射速度。本文主要考虑常规工艺
参数(模具初始温度、浇注温度以及保压时间)对铸件以及模具温度场的影响。主要分析比较模拟温度和实测温度的变化程度,以及压铸过程中型腔上不同位置的温
度变化规律。
本实验中。选取的模拟压铸工艺参数为:铸造压力60MPa,高速压射速度6m/s,低速0.2m/s,浇注温度650℃,模具初始温度120℃,整个铸造周期为30s。
3.1模拟温度场分布
根据计算,由Thermo-calc软件分析得到在结晶潜热的释放过程中ADC12铸件液相线为607.5℃,固相线为525.8℃,并且随温度的递增,
固相率和温度呈线性关系。图3(a)为铸件凝固完成后的温度分布示意图。研究发现随着时间递增,铸件径向温度从内到外逐渐降低,温度呈现明显的规律性,同
时变化平缓且两边对称。图3(b)为铸件径向温度曲线图,温度从650.28℃降低到180.21℃。
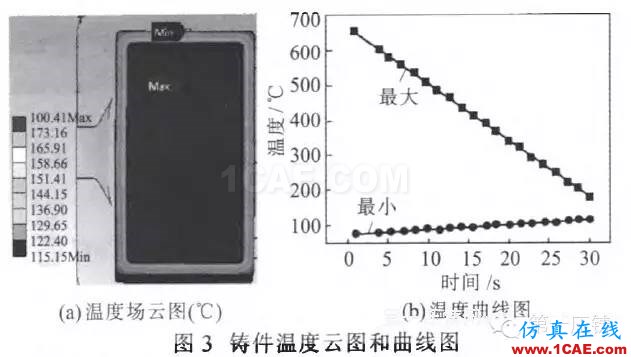
模具的温度场分布直接决定了模具的使用寿命.因而研究模具温度场的分布有着重要的意义。图4(a)为压铸过程模具的温度场分布示意图,发现与铸件接触面温度最高,模具底部温度最低。图4(b)是模具总热流量的矢量图,研究得到模具各面连接处热流量最大.冈此容易m现裂纹和变形。
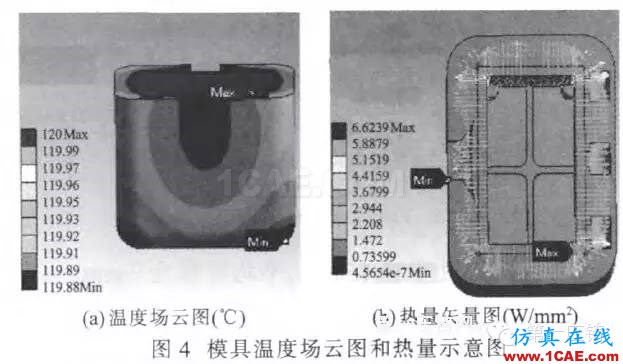
图5显示了型腔表面不同位置处的模具温度分布曲线。发现浇人液态金属1 s后,随着距铸件表面距离的增加,模具的温度受铸件充型、凝固过程的温度影响逐渐减小。在此工艺条件下,距型腔表面距离超过6mm后,受金属液的影响较小。另外,浇口附近的模具温度和型腔表面的平均温度呈现相似的变化规律。由于浇口处金属凝固最晚,所以仍保持较高的温度。
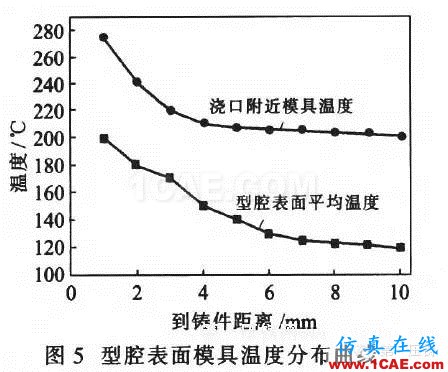
3.2实验所测温度分布
为验证模拟结果的准确性,本实验采用K型热电偶。在压铸过程中,从与型腔表面距离相同的测温点TCl和TC2两位置所测得温度曲线的变化趋势来看,表现出
了相似的变化规律,而且数值也比较接近,这说明了实际的传热过程接近一维传热。TC1、TC2热电偶测量温度(分别用TC1M和TC2M表示)以及模拟过
程计算得到的TC1温度(用TC1C表示)如图6所示。可以发现:热电偶所测温度与计算温度基本吻合。
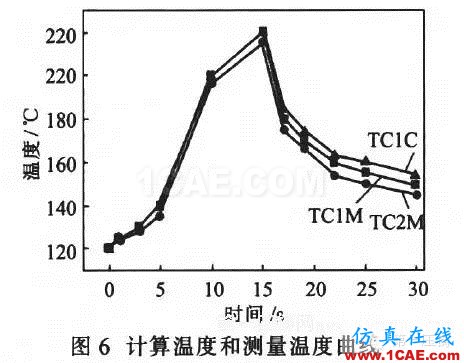
因此,考虑影响测量因素的热电偶本身的误差、热电偶安放位置以及热电偶的延迟效应和衰减效应阴都得到了有效地控制。提高了模拟的准确性。
相关标签搜索:ADC12压铸过程的温度场数值模拟与 工艺参数的优化 Ansys有限元培训 Ansys workbench培训 ansys视频教程 ansys workbench教程 ansys APDL经典教程 ansys资料下载 ansys技术咨询 ansys基础知识 ansys代做 Fluent、CFX流体分析 HFSS电磁分析 Abaqus培训