钻杆钢腐蚀疲劳的断口分析
2016-12-07 by:CAE仿真在线 来源:互联网
首先通过对钻杆钢进行了疲劳腐蚀实验,然后借助于扫描电镜对S135钻杆钢的腐蚀疲劳断口形貌进行宏观和微观分析研究,最后对其断口形貌形成的影响因素进行讨论。结果表明其疲劳断口是以脆性性为主的多源性断口,且在不同加载载荷下,腐蚀钻杆钢的疲劳断口主要由粗糙程度差异明显的疲劳裂纹源区和劳裂纹稳态扩展区与疲劳裂纹瞬断区组成,在裂纹源区断面相对光滑,裂纹扩展区断面相对粗糙,且疲劳裂纹扩展一般萌生于金属表面。而且随加载载荷的大小不同,其各区域面积也随之不同。
随着现代工业的快速发展,当今社会对石油资源的需求越来越大。伴随着浅部油气层的长期开采,各大主力油田大多己进入开发的中后期,浅层勘探很难发现大型的油气资源,因此在今后的油气勘探中,深井、超深井和大位移井等高难度井将成为国内外各大油气田增产上储的主要手段。近年来随着定向井、大位移井、水平井、深井等高难度井应用的逐年增多,钻具失效断裂事故也随之增加。
钻具失效在石油钻井界是普遍存在的。在深井!超深井、大位移井等高难度井钻井过程中,钻具的受力状况复杂,井下环境异常恶劣,处在内、外充满钻井液的狭长井眼里工作,通常承受弯曲、挤压、扭转、液体压力等载荷,因此钻具在井下的运动是一个复杂的动力学系统。钻井液是由固体、液体和化学处理剂组成的复杂混合液,碱性极强,pH值大多在7-11之间。在钻井过程中,由于钻井液及其它腐蚀介质(如硫化氢、二氧化碳等)和复杂交变应力的共同作用,会严重降低钻具的疲劳寿命,使钻具极易发生腐蚀疲劳断裂事故。钻具的腐蚀疲劳断裂没有疲劳极限,因此很难预测其疲劳寿命,危害性极大。钻井过程中钻具在任何部位断裂都会造成严重的后果,导致油井报废。美国的统计和估算表明:14%的钻柱断裂事故发生在井上,平均每发生一次损失约106000美元,这是正常消耗以外的巨额费用。据统计我国每年必须用数亿元人民币的外汇进口各种规格的钻杆和钻挺。
根据管材研究所2003年对国内十几个油田调查资料统计:全国每年发生钻具断裂事故约1000起,其中约70%发生在深井、定向井、大位移井、水平井等高难度井中。在管材研究所1999年到2003年完成的钻具失效分析中,有72%的事故与高弯曲应力、高摩阻、腐蚀介质等复杂工况有关。在复杂工况下钻柱主要失效类型为钻柱腐蚀、钻柱腐蚀疲劳断裂、钻柱接头摩擦热纵向开裂、钻挺螺纹疲劳断裂以及钻杆的氢脆等。钻柱腐蚀疲劳失效[1-2],在钻柱失效中约占40%,且以钻杆为主。统计表明:在钻杆失效中,约80%为腐蚀疲劳。由此可见,石油钻杆钢的腐蚀和腐蚀疲劳被广泛关注。
本文以S135钻杆钢为研究对象,在NaCl腐蚀溶液中,通过在疲劳试验机上加载不同载荷获得钻杆钢试样,清洗保存;然后采用扫描电镜( SEM )对腐蚀疲劳断口形貌进行分析,总结钻杆钢在不同加载载荷下的腐蚀疲劳规律及断裂特征。
在实验加载过程中,为了使腐蚀液对试样表面有充分的腐蚀,试验应在低的频率(低于l.5Hz)下进行,经研究表,因此本试验采用的载荷频率为1Hz。腐蚀介质3.5%NaCl,pH值7-8,介质温度控制在23℃士3℃之间。裂纹长度由读数显微镜测到(精确到0.001mm), 疲劳加载试验机上采用轴向应力控制、正弦波,疲劳试验采用 3 种不同的应力σ:(1) σ=8KN;(2) σ=12KN;(3) σ=16KN。为了更好的实际工况,在整个试验进行的过程中,介质箱应始终处于敞开状态,以利于空气中的氧分子进入到溶液中,与腐蚀疲劳试样进行作用。试验步骤如下:
(1)将S135钻杆钢试样加工成直径为5mm圆棒状光滑试样;并进行清洗、保存等处理;
(2)在PLD-100KN型电液伺服疲劳试验机上进行疲劳试验,获得腐蚀疲劳断口试样;
(3)在JSM6390A型扫描电镜下进行试样断口观察,分析腐蚀疲劳规律及断裂特征;
(4)得出结论,并进行分析讨论。
3.1 宏观断口形貌分析
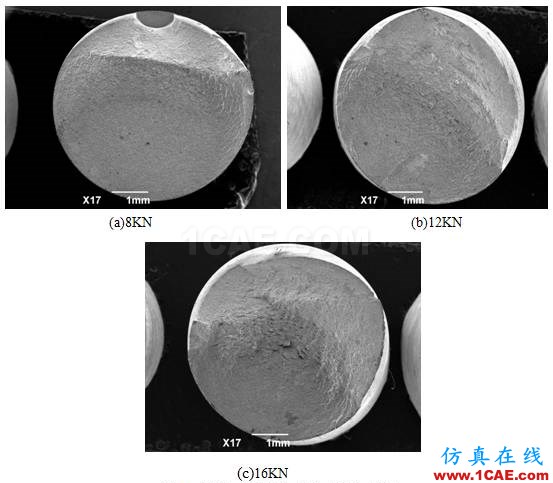
如图1为不同加载载荷下的宏观断口形貌特征图,从图中可以看出它们均具备了断口形貌的三大特征区域:疲劳源区、疲劳裂纹扩展区、瞬断区;同时,经研究表明,在大气NaCl溶液环境下,断口表面多表现出点蚀坑的存在(黑色点状部分),在载荷作用下,断口中间部位的裂纹沿着试样断口表面横向扩展,而裂纹前沿靠近表面的地方均出现了明显的宏观剪切唇,该剪切唇与裂纹面之间的夹角大约为45°。显然,对于钻杆钢腐蚀疲劳试验,裂纹面在扩展过程中的取向发生改变,导致腐蚀疲劳裂纹由起初的拉伸模式疲劳裂纹逐渐向剪切模式疲劳裂纹过渡,疲劳裂纹从试样表面形成,向试样内部扩展,且由图2看出,不同载荷下,断口各区域比例也随发生变化;从宏观形貌上分析断口特征,其断口附近无明显的塑形变形,都是脆性断裂,疲劳裂纹一般萌生于材料表面或靠近表面的位置。
比较图2中(a)、(b)、(c),在靠近裂纹源处,裂纹放射状明显,其后裂纹逐渐稀疏,裂纹扩展速度加快,显示出快速断裂的形貌特征,在图2(a)中有多处疲劳源,表现出多疲劳源特征,而在图1(b)、(c)中只有一处疲劳源;比较图1(a)、(b)、(c)断口区域的比例可以看出:随载荷的增加,断口上疲劳裂纹扩展区的面积减小,瞬断区增大。在图1(a)中,断口上的疲劳裂纹扩展区约占整个断面的 2/3,而在图1(c)图中,疲劳裂纹扩展区的面积则占整个断面的 1/2。
3.2 疲劳裂纹源的微观断口形貌特征分析
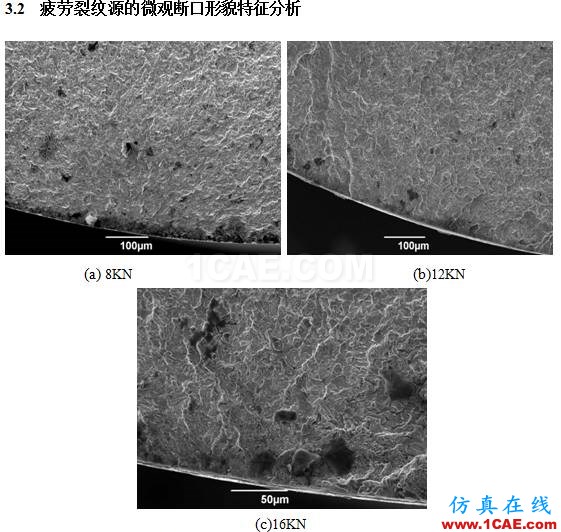
如图2为不同载荷下的疲劳源微观断口形貌图,疲劳裂纹一般萌生于材料表面或靠近表面的位置,裂纹从萌生点(点蚀坑)开始(如图中断口表层的灰黑色腐蚀层),在扩展中相遇,裂纹前沿因阻力不同而发生扩展方向上的偏离,此后,裂纹开始在各自的平面上继续扩展。根据相关文献表明,裂纹在不同的断裂面相交而形成台阶,这些台阶在断口上构成了放射状射线,且裂纹源区大多呈解理形貌;在断口上,裂纹从萌生点开始,以河流状花样向前扩展,在扩展中相遇,裂纹前沿因阻力不同而发生扩展方向上的偏离。此后,裂纹开始在各自的平面上继续扩展,不同的断裂面相互交割而形成台阶,这些台阶在断口上构成了放射状射线,随着加载载荷的增加,河流花样减少,在该区域内观察不到疲劳条带。
比较图2中(a)、(b)、(c),随着加载载荷的增加,其形貌特征显著,在图2(a)中,疲劳源处裂纹放射线相对集中,密度较大,裂纹细小;在图2(b)中,裂纹放射线密度逐渐发散,且密度随载荷增大而减小,裂纹形状也随之变得细长;而在图2(c)中,裂纹放射线更加疏散,且裂纹形状变得粗长。
3.3 疲劳裂纹扩展区的微观断口形貌特征分析
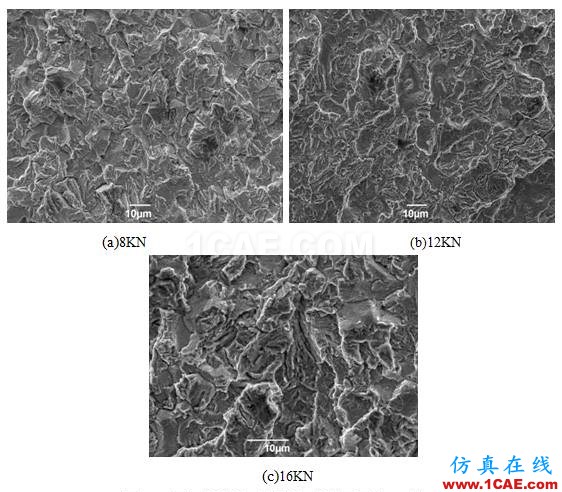
图3 不同加载载荷下的疲劳裂纹扩展区微观形貌
如图3为疲劳断口的裂纹扩展区微观形貌图,在加载载荷下,断口较为粗糙,且在该区域可以看到大量的小晶面,表明在裂纹扩展区,断裂方式主要以脆性断裂为主,同时,在不同载荷下的小晶面呈现不同的高度差,表现为晶面状形貌,且台阶尺寸也不尽相同;而且在断口形貌上有部分微裂纹,表明腐蚀疲劳裂纹基本上是在奥氏体晶粒内沿着不同的位向缓慢地以穿晶方式扩展,从而造成解理断裂,最终在其断面上形成解理形貌。
比较图3中(a)、(b)、(c),在不同加载载荷下,可以看出,在裂纹稳定扩展区以解理断裂为主要特征,可见,在图3(a)图中,解理台阶的晶面较小,高度差不明显;随着载荷的增加,在图3(b)中,解理台阶明显,呈明显的高度差,且面积增加,在图3(c)中,断口表面呈结晶状,解理台阶高度差更加明显,且晶面面积较大;由此,随着加载载荷的增加,扩展区解理形貌差别明显,其断口特征主要表现为解理形貌。
本实验通过对钻杆钢在腐蚀环境中不同加载载荷作用下所获得的疲劳断口进行宏观和微观的形貌分析,比较了不同载荷作用下的断口形貌特征,总结以下几点:
(1)在不同加载载荷下,腐蚀钻杆钢的疲劳断口主要由粗糙程度差异明显的疲劳裂纹源区和劳裂纹稳态扩展区与疲劳裂纹瞬断区组成。在裂纹源区断面相对光滑,裂纹扩展区断面相对粗糙,且疲劳裂纹扩展一般萌生于金属表面。
(2)裂纹源区大多呈解理形貌,表现为脆性断裂;在裂纹源区向裂纹稳态扩展区的过渡区,存在放射状条纹、塑性亮痕,呈现出脆性断裂形貌特征;其断口多表现为解理台阶。
(3)疲劳断裂过程中,随着载荷的增大,疲劳源处裂纹放射线密度逐渐减小,且扩展区面积逐渐减小,瞬断区面积逐渐增大。
相关标签搜索:钻杆钢腐蚀疲劳的断口分析 Ansys有限元培训 Ansys workbench培训 ansys视频教程 ansys workbench教程 ansys APDL经典教程 ansys资料下载 ansys技术咨询 ansys基础知识 ansys代做 Fluent、CFX流体分析 HFSS电磁分析 Abaqus培训