有限元分析在薄壁注塑模具设计中的应用
2017-01-23 by:CAE仿真在线 来源:互联网
11 前言
“薄壁”通常由壁厚少于1mm的轻便电子制件所定义的。对大的汽车部件来说,“薄”可以是2mm。目前,生产小尺寸、高精度、构造复杂的薄壁制件已经成为 注塑加工面临的主要挑战。由于快速充模和高压能以高速将熔融的热塑性材料注入模腔中,从而防止了浇口冷固。因此,注塑速度和压力成为确保薄壁注塑成功的关 键因素。当前,一个厚度小于2 mm的电子制件,充模时间通常不超过0.5秒,而注塑压力往往高于50MPa 。
为了缩短产品注塑成型周期,降低模具原材料成本,减少模具厚度已经成为设计人员采用的主要手段。但过薄的模具在经受注塑高压的冲击下会引起模板弯曲过大, 导致注塑制件不合格。面对这一矛盾,企业往往仅能依靠设计人员的经验,多次试模、修模,不断重复,直至注塑出合格的试样。这样对企业人力、物力资源都是很 大的浪费。而有限元分析(FEA)技术弥补了模具设计过程中依靠经验试制所带来的定性不定量的不足,它可以帮助技术人员在模具设计初期阶段,及时发现问题 并加以改进,从而提高生产效率,减少生产成本。目前,FEA在模具行业受到了越来越广泛的重视。
本文借助大型有限元工程软件ANSYS对某款薄壁注塑模具进行应力、应变分析和尺寸优化。首先将模具整体几何模型导入到ANSYS 中。然后,考虑模具的实际工作载荷和边界约束,对其施加位移和压力边界条件,以模拟其真实的注塑环境,并对整个模具进行网格剖分和应力、应变分析。最后, 尺寸优化设计为模具改进提出了参考方案。
22 有限元建模
2.1 几何模型导入
图1 所示是厂家提供的在某款注塑模具的几何模型,整个模具是由面板、底板、方铁、公模、公模镶件、母模镶件和母模7 个主要部分组成,熔融塑料被注塑机高压射入浇口,流经面板、公模,进入由公模和母模镶件所形成的内腔中,经保压成形生成成品制件。

(1 底板;2 方铁;3 公模;4 公模镶件;5 母模镶件;6 母模;7 面板;8 浇口)
几何模型导入到ANSYS 中是整个仿真分析的基础,利用ANSYS 与UG 的双向互导功能,可以在UG 的设计环境中直接激活ANSYS 并导入到ANSYS 分析环境,这就实现了从设计到分析的无缝接合,导入到ANSYS 的模型保留了原UG 模型的所有特征而没有任何丢失(见图1)。另外,ANSYS 在导入模型的过程中,自动识别并且建立了各连接部件之间的接触关系,由此大大简化了接触关系的定义工作,提高了分析效率。
2.2 初始条件设置
1)模腔压力和锁模力
模腔压力P 主要受下面5 个因素影响:浇口的数目和位置、浇口的尺寸、制品的壁厚、使用塑料的粘度特性和注塑速度。根据文献
P= P0×K=39×1.4= 54.6MPa (1)
注塑件投影面积数值:S = 6984.07mm2
该注塑模具工作所需要的最小锁模力:
F=P×S=54.6×106×6984.07×10.6 =381.33KN (2)
2)模腔压力加载时间历程
通过载荷时间历程的施加方式,来模拟填充到保压阶段的应力变化,即模腔压力由注塑开始的0MPa,上升到保压阶段开始的最高压力,然后在保压阶段下降到最大压力的80%,最后卸载至0MPa ,这称为一次加载过程,如图2 所示。
图2 模腔压力加载时间历程
综上分析,在面板上施加锁模力,大小381.33KN ,方向由面板指向公模。在模腔的内表面施加最大注塑压力,大小54.6MPa ,方向垂直于模腔内表面,底板上使用固定约束,以模拟模具在注塑阶段到保压阶段中的工作情况。所施加的边界条件如图3 所示。
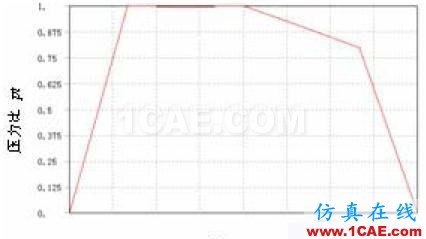
2.3 材料参数
面板、底板、方铁、公模和母模的材料为普通碳素钢S45C
2.4 模型的网格化
该注塑模具模型共划分了284954单元,总节点数是478202,如图4所示。具体网格划分方式与单元尺寸设定如下:
1) 面板,底板和方铁4 个部件,使用六面体占优的网格划分方式,单元边长尺寸为12.5 mm ,共划分4852 单元,25221 节点;
2) 公模和母模2 个部件,使用六面体占优的网格划分方式,单元边长尺寸为8 mm,共划分81771 单元,134523 节点;
3) 公模镶件和母模镶件2 个部件整体上使用六面体占优的网格划分方式,单元边长尺寸为8 mm;同时,为了捕捉模腔内的细节,再选择模腔内表面102 个面,使用全四面体的网格划分方式,单元边长尺寸为1.2 mm ,最共划分198331 单元,318458 节点,如图5所示。
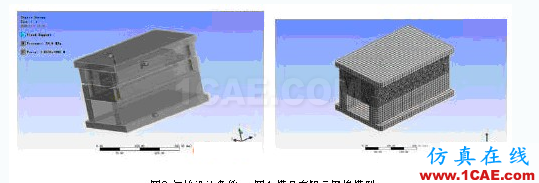
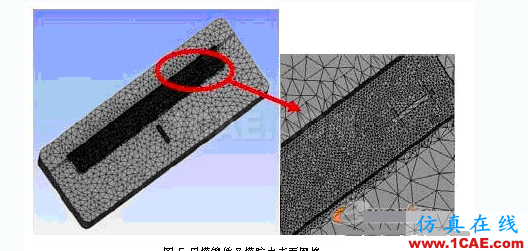
33 模具刚度和强度计算结果
通过计算结果的云图颜色深浅就可以判断变形和应力的大小,通过最大/最小值图标可以方便地判断最大/最小应力、应变的位置。同时,在计算结果的后处理中, 可以通过将应力、应变结果做成动画,更加直观地显示计算结果,方便设计人员确定问题所在。计算所得模具整体最大变形为0.0199mm,发生位置为公模/ 母模镶件模腔表面(如图6所示);最大等效主应力(Von Mises 应力)为302MPa ,发生位置为母模镶件模腔表面;面板与公模之间的最大压力为67.4MPa ,方铁与底板、母模之间的压力最大为102MPa 。上述指标均符合设计要求,即“保证塑件加工精度在0.01mm~0.03mm 之间”,最大等效应力小于材料屈服强度(826MPa )。
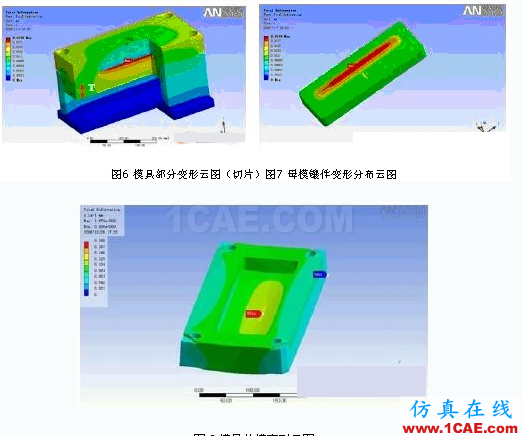
44 模具优化设计
为了改进模具设计,在模具整体变形和应力值不超过设计要求的情况下,尽可能的减少材料,对不同厚度的公模进行了对比计算。当公模的厚度(图6 所示尺寸T)变薄2mm 时,有限元分析的结果如图8 所示。从图中可以看到公模最大变形由原来的0.011mm 增加为0.019mm ,最大变形发生的位置在公模底面中心位置(图8,MAX 处)。公模厚度减少2mm ,模具变形不大,依然满足“保证塑件加工精度在0.01mm~0.03mm 之间”的设计要求。
55 结论
借助ANSYS 结构静力学分析功能,对某型号注塑模具的应力应变分析,确定其在特定工况下(锁模力为381.33KN ,注塑压力为54.6MPa )模具的整体变形及应力分布,校核模具在工作状态下的结构强度。获得以下结论:
1)利用ANSYS 和UG 间的接口,能够将注塑模具模型导入到ANSYS 分析环境中,并且能够自动的建立和识别零部件间的接触关系,提高了分析效率;
2)整个模具的镶件部分变形最大值为0.0199mm ,位置在母模镶件模腔内表面上,保证了该注塑模具加工塑件的精度在0.01mm~0.03mm 之间,故可以认为该模具结构设计比较合理;
3)整个模具的镶件部分等效应力分布比较均匀,虽然局部最大应力达到302MPa ,考虑到该部分使用的模具钢2738 ,并未超出其屈服强度(826MPa),故可以认为这个结构设计比较合理。
4)模具局部最大应力值随之锁模力和注塑压力的增大而增大,采用ANSYS 多工况分析,计算得到导致模具发生塑性应变的最大锁模力为1042KN ,最大注塑压力为149MPa 。
5)根据不同尺寸的模具,做了优化分析。在满足工作要求的情况下,得到最优的模具尺寸,即公模厚度减少2mm ,从而节省了模具材料和制造成本。
相关标签搜索:有限元分析在薄壁注塑模具设计中的应用 Ansys有限元培训 Ansys workbench培训 ansys视频教程 ansys workbench教程 ansys APDL经典教程 ansys资料下载 ansys技术咨询 ansys基础知识 ansys代做 Fluent、CFX流体分析 HFSS电磁分析 Abaqus培训