【技术篇】基于ANSYS的汽车前轴强度分析和模态分析
2017-03-23 by:CAE仿真在线 来源:互联网
前轴是轻型载货汽车前桥的重要部件,汽车前轴的结构设计是否满足汽车安全行驶的要求直接决定了整车的安全性,同时又影响了汽车的动态特性。前桥的两侧安装着从动车轮,并通过悬架与车架相联,工作时,其承受车轮传来的制动力和侧滑扭矩,同时又承受悬架作用的垂直载荷,为确保前桥工作时的可靠性和安全性,因此对前桥的强度,刚度,抗冲击性,疲劳强度及可靠性等方面都提出很高的要求。汽车前轴在承载车身重量的同时,还会受到来自行驶路面、发动机及其他运动部件产生的激振。如果各种激振频率与前轴的某阶固有频率相等时,就会引起共振,影响前轴及其装配零部件的使用寿命。因此在前轴的设计阶段,不仅需要考虑其强度和刚度等静态特性,也要将其动态特性纳入前轴的前期设计体系,与整车同步开发,为提升整车的NVH(噪声、振动、声振粗糙度)性能提供重要的理论依据。
三种工况下强度分析的结果表明,前轴在结构设计上基本符合强度要求,具有较高的安全系数。前轴的模态分析表明,其没有发生振动突变现象,并且没有与行驶路面激励发生共振,此外其前六阶固有频率与人体各器官的固有频率相差较大,不会与人体某些器官发生共振。
从改革开放以来,中国的汽车工业随着国民经济的发展和交通运输体系的全面建立得到了飞速发展。特别在2001年中国加入WTO以后,全球性的贸易给中国的汽车行业带来巨大的竞争,但同时也带来了新的发展机遇。目前,全球的汽车生产商不仅仅在车型、价格、新技术等方面激烈角逐,同时更加注重产品质量。因此,如何以最低的成本生产出性能最佳,质量最好的汽车产品成为当今我国汽车制造的一大主题。为了争夺市场份额,全世界的汽车制造商对零部件的要求也越来越高,由原来的只从内部配套厂采购的保护政策转变为向全球的零部件制造商进行采购的竞争政策,这种政策的转变给我国现有的规模小,生产效率低,缺乏自主创新能力的汽车零部件生产企业带来巨大的冲击。而且现阶段我国各种能源资源人均占有量相比于国际水平依然很少,为了提高能源资源的利用率,党的历年政府工作报告中就明确的把能源资源的节约与高效利用提上了议事日程,倡导全民共同努力,充分利用和节约现有资源。在这种国际形势下,生产经济、耐用、节约资源的汽车零部件就成为全球各汽车零部件制造商共同追求和奋斗的最终目标。
如今全球的汽车工业正处在高速发展阶段,而作为汽车工业的重要配套行业,中国汽车车桥行业自然面临着重要的机遇与挑战。同时现代汽车通过采用各种设计不断追求更高的动力指标、经济指标及舒适性指标,相应会使车桥的机械负荷不断增加,形状也越来越复杂,这对汽车车桥的设计与制造提出了更高的要求。
汽车的车桥通过悬架与车架连接,其支承了汽车大部分的重量,并将车轮受到的牵引力或制动力,以及侧向力通过悬架传递给车架。在汽车设计时,为了便于与不同类型的悬架相配合,汽车的车桥分为整体式和非整体式两种。而按车桥的使用功能划分,其又可分为转向桥、驱动桥、转向驱动桥和支持桥。而转向桥和支持桥都属于从动桥,其中起主要承载作用的是前梁,又称前轴,在车辆行驶时主要承受弯矩和扭矩的作用。与非独立悬架相配合使用的转向桥前轴多为工字形结构,主要是因为采用工字形断面可以有效的提高前轴的抗弯强度,同时还可以减轻前轴重量,另外在钢板弹簧处向两侧车轮方向逐渐由工字形断面过渡为方形断面,可以提高前轴的扭转刚度,又可以保持其断面强度相等。目前,该种形式的前轴结构主要应用于载重货车。而本文研究的就是轻型载货汽车的整体式前桥,它的前轴就是工字形结构。
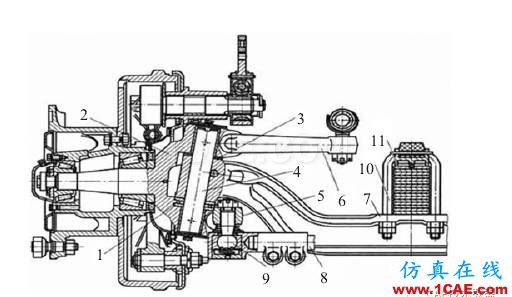
图1-1 整体式转向桥结构
1. 转向节推力轴承 2.转向节 3.调整垫片 4.主销 5.转向梯形臂 6.转向节臂 7.前轴 8.转向横拉杆 9.球销 10.钢板弹簧支座 11.钢板弹簧
在前轴的初始设计阶段,传统的简化方法对前轴的强度及刚度计算,不可能得到较精确的解析解,甚至可能是错误的解。为得到满足工程要求的数值解,就必须运用最近得到不断完善和快速发展的现代数值模拟技术,其成为现代工程学形成和发展的重要推动力之一。传统的产品设计流程是一个设计者反复进行多次设计的过程。一般首先由工程师借助CAD 工具进行产品的初始设计,接着提交给工厂进行加工制造,然后对实物产品进行试验,如果产品不能满足各方面功能要求或者失效,就需要工程师对产品的设计进行修改,甚至重新设计,如此不断反复,直至实物产品在实际试验中满足全部功能要求为止。随着有限元分析技术的发展与成熟,利用有限元分析,能够在产品设计之初,就对产品的结构和强度进行比较全面的分析,尤其对于需要进行模具开发的产品,能够显著的提高产品开发的一次成功率,缩短产品的开发周期,提高产品品质,降低开发成本,减少资源浪费,并且可以使产品的结构得到最大的优化,减少零件自身的质量。因此,在汽车初始设计阶段利用有限元分析软件ANSYS进行有限元分析计算具有十分重要的意义和作用。其能够对汽车的结构和各零部件进行比较全面的分析,有效地减少产品的试验周期,降低设计与制造费用,显著减少了产品的开发周期。
现今国外利用有限元法进行汽车的结构分析和计算方面的技术已经相对比较成熟。国外从20世纪60年代中后期开始就十分重视利用有限元法对汽车结构进行辅助分析和计算,为汽车的初始设计提供理论依据,并且在汽车的某些结构件静态分析方面取得了大量的研究成果。到20世纪70年代,人们在汽车结构的分析方面,不仅仅满足于静态特性分析,开始向动态特性分析方面拓展,一般采用一些大型计算程序并逐渐开发专用程序,但是计算量大,计算过程复杂。而国内在汽车有限元法方面的发展主要是在前轴的成型制造方面,哈尔滨工业大学材料科学与工程学院的蒋鹏教授等人利用有限元软件模拟前轴的精密辊锻成型过程,了解了前轴精密辊锻成型机理,掌握变形规律,直接在计算机上检验模具设计和工艺设计的合理性,提高了模具设计质量,缩短产品试制周期,对前轴精密辊锻技术的发展和提高具有重要意义。此外我国设计者还普遍利用有限元法进行汽车的静强度分析和模态分析。在对前轴进行有限元分析之前,要对前轴进行三维实体建模。湖北三环车桥有限公司的郑乐启等人提出了基于SolidWorks平台的汽车前轴混合建模,可以根据汽车前轴不同的结构特点,充分利用SolidWorks软件的建模功能,对零件的每一部分进行分割,采用最简洁的方法将汽车前轴模型设计出来。合肥工业大学机械与汽车工程学院的张红旗等人提出利用Pro/E软件中的变截面扫描,可以高效的实现汽车前轴三维参数化实体建模。中铁四局一公司的熊向进则通过HyperWorks软件对汽车前轴的强度进行有限元分析,得出前轴紧急制动和侧滑工况下的应力分布图。北京工业大学的郭雷提出了基于ANSYS汽车前桥的模态分析,利用ANSYS软件分析提取前轴的前六阶振型和固有频率,分析其固有频率与外界激励及人体共振频率的耦合情况,为前轴的动力学研究及改进提供了重要的理论依据。
根据课题的基本要求,本文主要在以下几个方面开展了工作:
(1)阐述了本课题的研究背景及意义,有限元在汽车前轴设计中的应用,
(2)利用现行全球用户最大的ANSYS软件,确定单元模型,通过三维建模软件Pro/e建立前轴的实体模型,通过智能网格划分器,将前轴模型划分为具有32441个节点,146416个单元的有限元计算模型。
(3)建立前轴的力学模型,选择越过不平路面、紧急制动、侧滑三种维修工况,通过力学原理确定前轴在相应工况下的载荷,并转换为ANSYS中加载载荷,确立边界约束条件。
(4)对该轻型载货汽车前轴进行静态分析。前轴的静态分析主要包括两个方面:结构刚度分析和结构强度分析。其中刚度分析主要分析其弯曲刚度,而强度分析则主要从前轴整体出发,对前轴强度进行校核。
(5)对该轻型载货汽车前轴进行有限元模态分析。通过对该轻型载货汽车前轴进行模态分析,获取其前六阶固有频率和振型,通过与行驶路面的激振频率、发动机的固有频率以及人体各器官的固有频率进行对比,从宏观角度来分析前轴的动态特性。
(6)将前轴的静态分析和模态分析结合,得出最后的结论,提出改进意见和不足之处,并利用得出的结论指导实际生产,为前轴设计者提供理论参考依据,缩短设计周期,降低设计成本。
由于有限元分析软件ANSYS的建模功能比较薄弱,本章首先介绍用三维软件建立三维模型。用Pro/e5。0建立前轴的实体模型,在前桥建模时进行一些简化,去除一些对结果影响不大的倒角和凸台,加快计算机的求解时间,提高求解精度,然后将建立的实体模型以igs格式保存下来,然后导入ANSYS中进行有限元分析。
前轴的分析计算所需定义的材料特性包括:弹性模量、泊松比、材料密度、抗拉强度及屈服强度。由于前轴为塑性材料,故以屈服强度作为极限应力。前轴的材料特性如表2-1所示。
特征 |
材料 |
弹性模量(Mpa) |
泊松比 |
材料密度(g/mm3) |
抗拉强度(Mpa) |
屈服强度(Mpa) |
前轴 |
45 |
2.08e5 |
0.3 |
7.85 |
590 |
355 |
表2-1 前轴的材料特性
考虑到前轴结构的实体特征,采用Brick 8node 45类型。Solid45单元在ANSYS软件中用于构造三维实体,它通过8个节点来定义,每个节点有3个沿x、y、z方向平移的自由度。这种单元类型是ANSYS软件中处理实体类型问题最基本的单元类型之一,是处理固体力学问题最常用的单元。
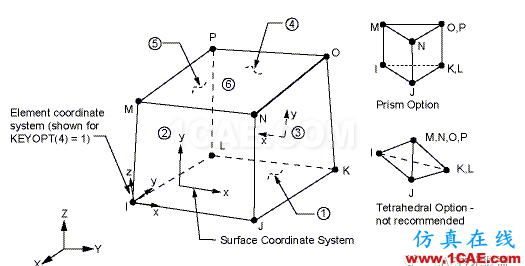
图2-1 Solid45的几何特征
由于前轴的结构比较复杂,可以在不影响分析结果的前提下,对其进行适当的简化。Pro/e三维建模软件提供了混合,混合扫描,变截面扫描这些特征,可以相对容易的实现前轴三维实体的构建,提高了三维建模的效率。前轴的实体模型如图2-2所示,前轴的主要设计参数如表2-2所示。
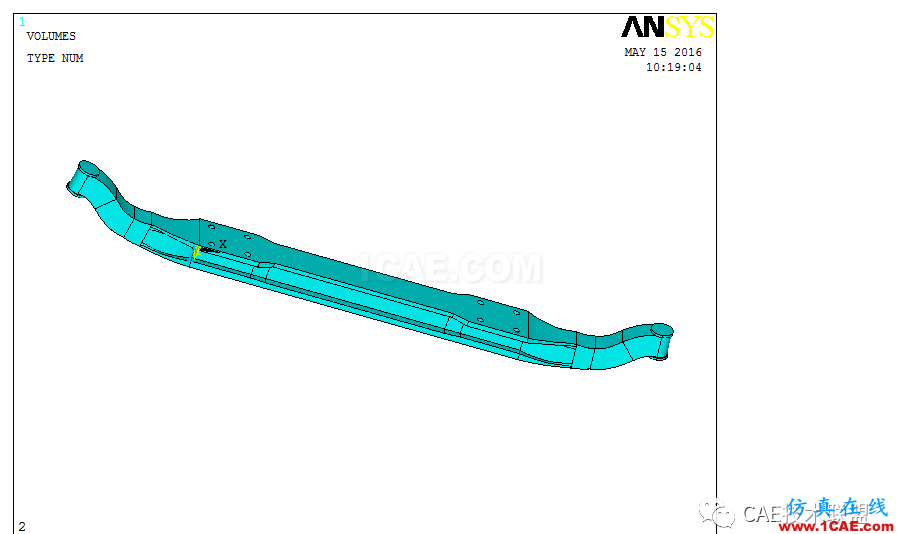
图2-2前轴的实体模型
表2-2 前轴的主要设计参数
序号 |
参数 |
参数值 |
1 |
最大承载质量G,N |
55000 |
2 |
轴距L,mm |
6100 |
3 |
满载时整车质心具地面的高度h,mm |
1294 |
4 |
满载时整车质心至后桥中心距l,mm |
1987 |
5 |
前轮距B1,mm |
2020 |
6 |
主销中心距M,mm |
1853.3 |
7 |
板簧距B2,mm |
900 |
8 |
轮胎半径r,mm |
526 |
9 |
道路附着系数ɸ |
0.8(制动);0.4(侧滑) |
10 |
动载系数K |
2.5 |
11 |
制动时前轴质量分配系数m1 |
1.7 |
汽车前轴进行有限元网格划分时,对前轴的实体进行自由网格划分,设置网格划分的精度为6级,网格的长度取为10mm,,生成具有32441个节点,146416个单元的有限元计算模型。对前轴进行网格划分的结果如图2-3(a)和(b)所示。
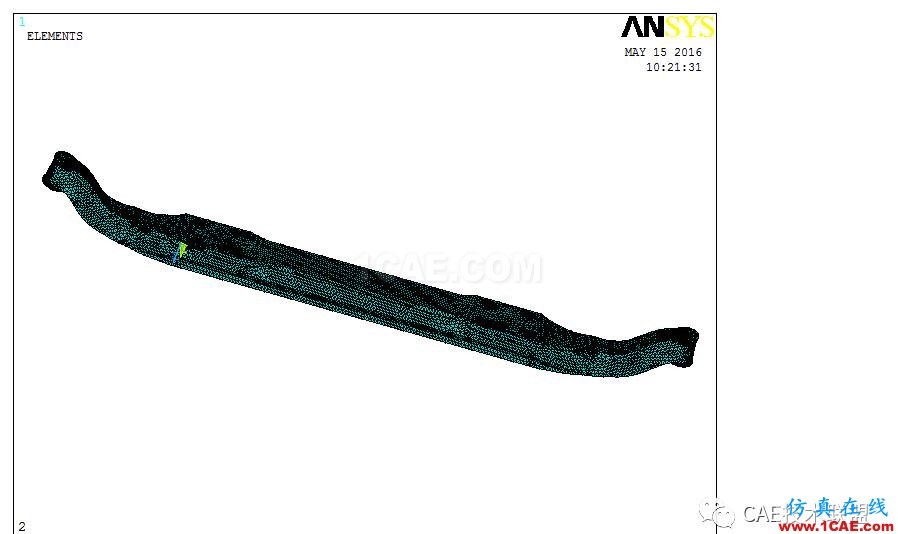
图2-3(a)前轴进行网格划分的整体图
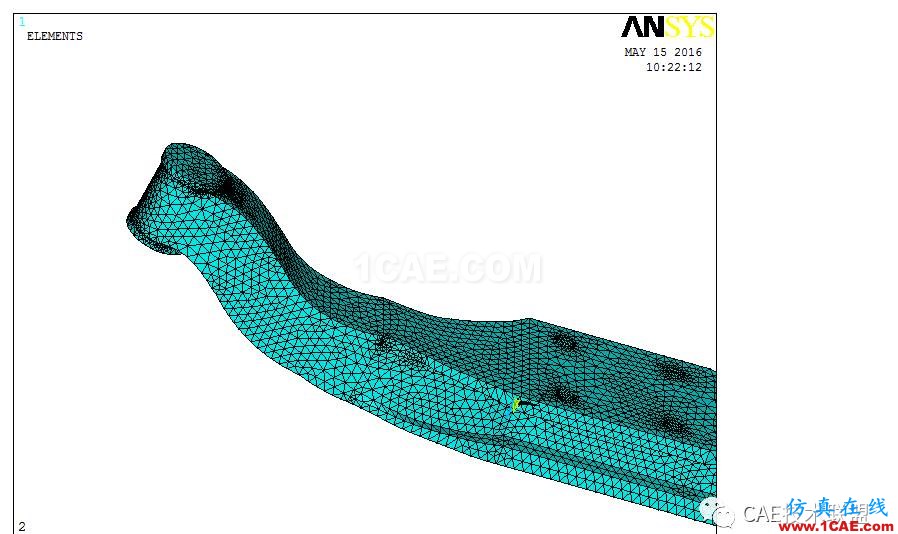
图2-3(a)前轴进行网格划分的局部放大图
在汽车正常行驶过程中,其受力状况比较复杂,主要包括垂向力、侧向力和纵向力。根据前轴的受力情况,对前轴的受力按3种危险工况进行分析计算,即越过不平路面工况、侧滑工况和紧急制动工况。如图3-1所示,由车辆行驶过程中的受力分析可知:越过不平路面工况为垂向力单独作用的工况;侧滑工况为垂向力和侧向力共同作用的组合工况;紧急制动工况为垂向力和纵向力共同作用的组合工况。此轻型载货汽车满载时的最大重量为55000N。
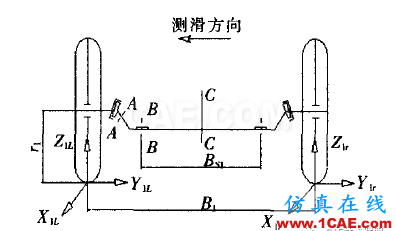
图3-1 前桥受力简图
Z为作用于两侧车轮的垂直反作用力;X为作用于两侧车轮的水平反作用力;Y为作用于两侧车轮的横向反作用力。
越过不平路面工况主要是垂向力单独作用。垂向力
Fz=

(3-1)
Fz为作用于两侧车轮的垂直反力;Kd为动载系数,其值取2.5;G为前轴满载载荷。
紧急制动工况主要是由垂直力和纵向力共同作用。垂向力
Fz=

(3-2)
Kd为制动时前轴的质量分配系数,其值取1.7。
纵向力
Fx=

(3-3)
根据工程经验,制动时的道路附着系数ɸ取0.8。
侧滑工况主要为垂直力和侧向力共同作用。垂向力
Fz=

(3-4)
侧向力
Fy=

(3-5)
式中ɸ为侧滑工况的道路附着系数,其值取1.0。
本章由获取的前桥设计参数,对汽车的前轴进行强度分析。按照上一章前轴的受力情况,对前轴的受力按照3种危险工况进行有限元分析计算,即超越不平路面工况,紧急制动工况和侧滑工况。采用有限元分析软件ANSYS分析前轴在3种危险工况下的应力与变形,判断其强度和刚度是否符合设计要求。
在越过不平路面工况下,前轴左侧转向节轴颈约束 y、z 方向的移动以及 x、z 方向的转动,前轴右侧转向节轴颈约束 x、y、z 方向的移动以及 x、z 方向的转动。由第三章中前轴在垂直工况下的受力分析对前轴进行加载。该工况下垂向力以均布载荷施加在钢板弹簧座上。前轴的应力分布云图如图4-1所示。前轴的位移分布云图如图4-2所示。由应力分布图可知,最大应力位于转向节轴颈处,其值为51.6Mpa,小于材料的屈服强度,符合强度设计的要求。由位移分布云图可知,前轴的最大变形为0.17mm,没有超过设计标准规定的最大变形量1.5mm,符合刚度设计的要求。
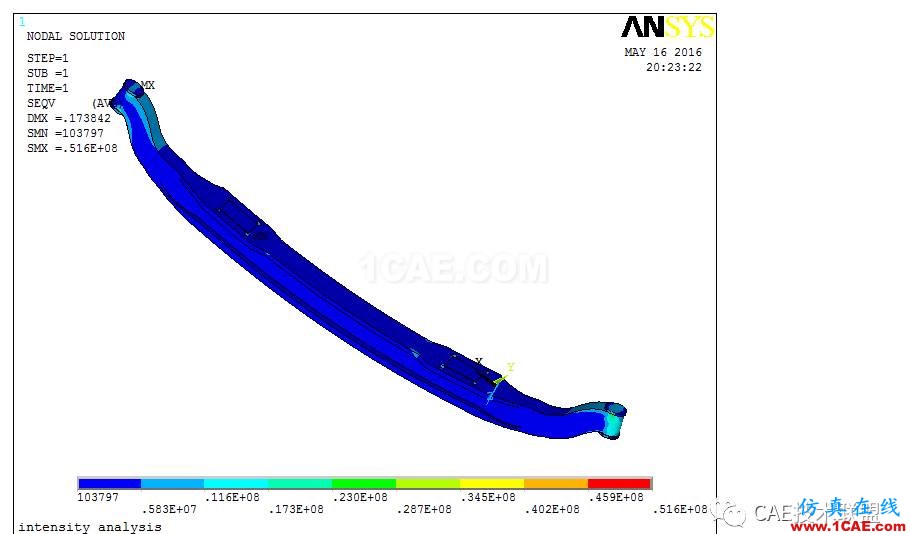
图4-1 垂直冲击工况前轴的应力分布云图
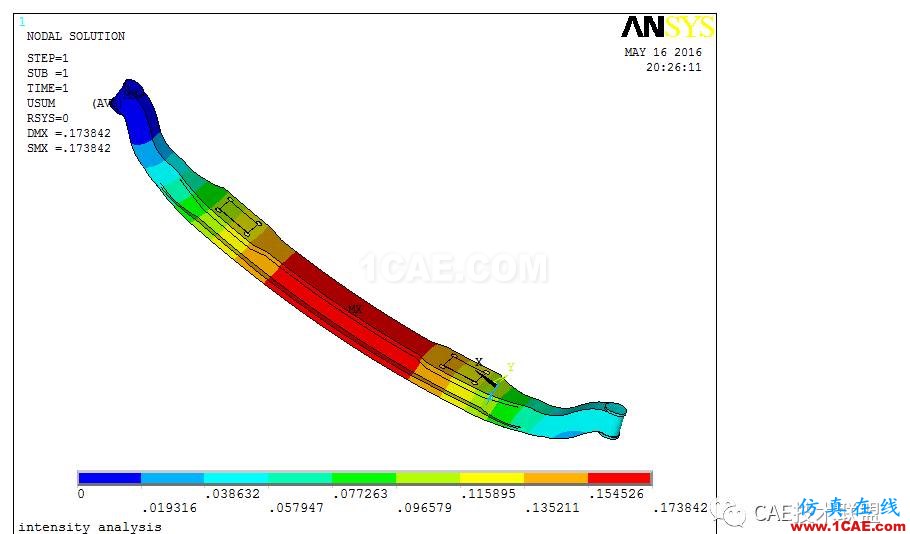
图4-2 垂直冲击工况前轴的位移分布云图
在紧急制动工况下,前轴左侧转向节轴颈约束 y、z 方向的移动以及 x、y方向的转动,前轴右侧转向节轴颈约束 x、y、z 方向的移动以及 x、y方向的转动。由第三章中前轴在紧急制动工况下的受力分析对前轴进行加载。该工况下垂向力以均布载荷施加在钢板弹簧座上,制动的纵向力以均布载荷施加在安装螺栓孔的内表面上。前轴的应力分布云图如图4-3所示。前轴的位移分布云图如图4-4所示。由应力分布图可知,最大应力位于转向节轴颈处,其值为163Mpa,小于材料的屈服强度,符合强度设计的要求。由位移分布云图可知,前轴的最大变形为1.07mm,没有超过设计标准规定的最大变形量1.5mm,符合刚度设计的要求。
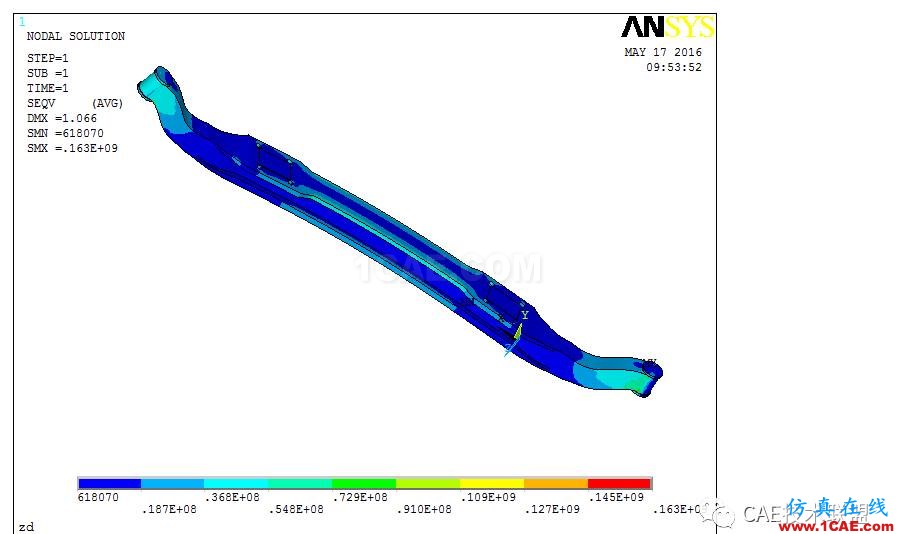
图4-3 紧急制动工况前轴的应力分布云图
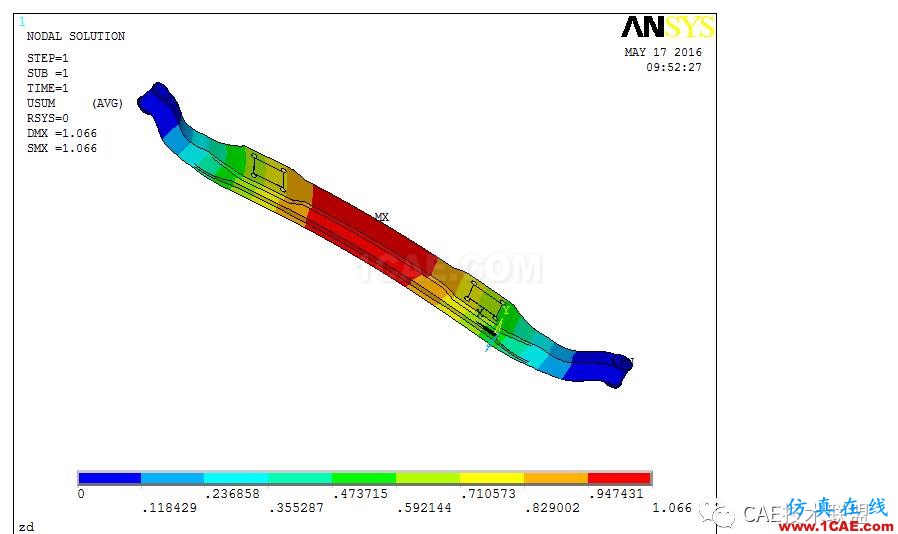
图4-4 紧急制动工况前轴的位移分布云图
在侧滑工况下,前轴左侧转向节轴颈约束 y、z 方向的移动以及 x、z方向的转动,前轴右侧转向节轴颈约束 x、y、z 方向的移动以及 x、z方向的转动。由第三章中前轴在侧滑工况下的受力分析对前轴进行加载。该工况下垂向力以均布载荷施加在钢板弹簧座上,侧滑时的侧向力以均布载荷施加在安装螺栓孔的内表面上。前轴的应力分布云图如图4-5所示。前轴的位移分布云图如图4-6所示。由应力分布图可知,最大应力位于转向节轴颈处,其值为43.6Mpa,小于材料的屈服强度,符合强度设计的要求。由位移分布云图可知,前轴的最大变形为0.11mm,没有超过设计标准规定的最大变形量1.5mm,符合刚度设计的要求。
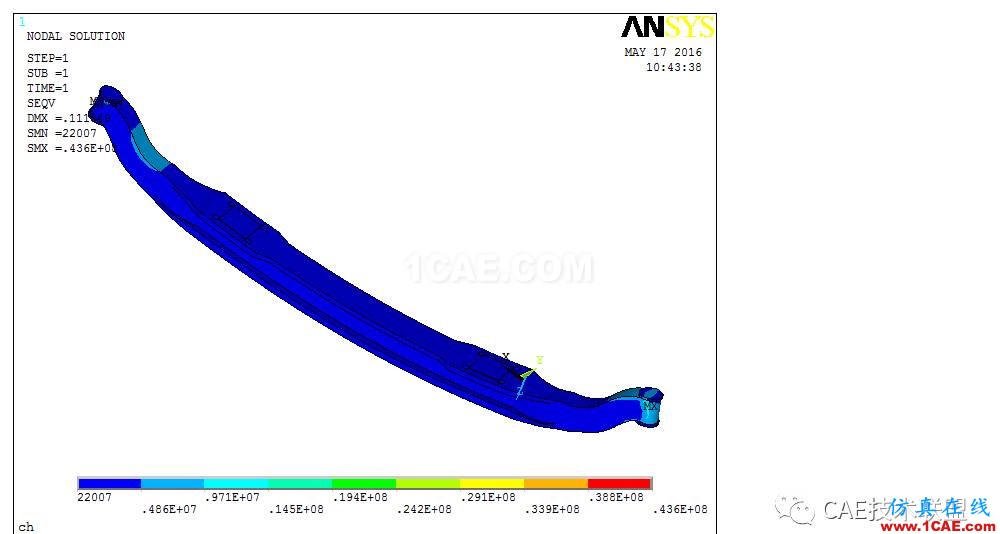
图4-5 侧滑工况前轴的应力分布云图
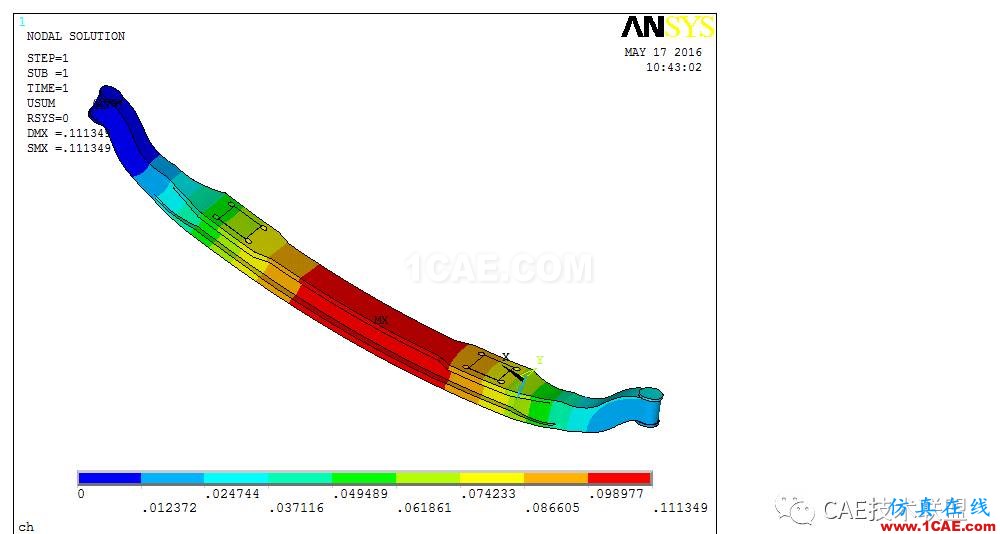
图4-6 侧滑工况前轴的位移分布云图
通过分析结果可知,制动工况下应力和变形均最大,最大应力为163Mpa,位于转向节轴颈处,最大变形为1.07mm。紧急制动工况出现最大应力和变形的原因是:在紧急制动工况下,制动力垂直于轴向,产生剪应力,从而导致组合应力和变形均增大。在该工况下,前轴的最大应力仍小于屈服极限,强度安全系数n=2.2。此时安全系数依然较大,满足前轴强度设计的要求。
以前在前轴的结构设计中,往往首先考虑前轴结构的静强度和刚度,而忽略了前轴的动态特性。但汽车在实际行驶过程中,前轴要承受来自外界和内部各种激励源的激励,其中主要的激励是行驶路面对车轮的冲击和汽车发动机的振动。这些动载荷直接作用在汽车前轴上,是时间的函数。因此,前轴结构上受动载荷作用而产生的位移、应力和应变不仅随其结构的空间位置变化,同时也随着时间的变化而变化。当作用于前轴的动载荷的频率与前轴结构的某些固有频率接近或耦合时,前轴结构将产生强烈的振动,即共振,产生很大的动应力,造成前轴强度的破坏或产生结构上不允许的大变形,影响汽车乘坐的舒适性和平稳性。
如今,车辆乘坐的舒适性和平稳性已成为消费者衡量整车性能的一个重要指标。并且消费者也越来越注重车辆乘坐的舒适性,所以对车辆结构进行模态分析来减少共振发生的可能性也越来越受到设计者的重视。在过去,工程技术人员在研究车辆结构的动态特性时,一般只能通过实验方法来实现,这种方法不仅费时费力,并且需要有实车作为样车,所以就不能在产品设计和开发初期就对乘坐的舒适性进行控制和评价。因此,在车辆初始设计中,采用有限元法对前轴进行模态分析,获取前轴结构本身所具有的刚度特性,即振型和固有频率,提前了解前轴的动态特性,从动态角度对前轴进行初始设计,分析计算其振动特性,判断其是否满足动态要求,为前轴进一步合理的改进提供科学的理论依据,同时它可以在设计开发的初始阶段就预测出前轴在各种工况下的振动特性及响应,能够避免前轴与汽车其他构件发生共振,降低噪声,减少企业的经济损失,具有十分重要的社会意义。
模态分析的有限元模型和静态有限元模型基本相同。对前轴进行有限元模态分析时,由于获取的是前轴的固有特性(固有频率和固有振型),与前轴所受外力无关,所以可以忽略外部载荷的作用。在对前轴进行模态分析时,如果前轴的有限元模态分析采用实际的边界条件支撑,这当然能够精确地反映出前轴工作时的动态特性,但前轴工作时的实际边界条件是十分复杂的,而且实际边界条件会在有限元模态分析中形成病态的刚度矩阵,这将严重影响有限元计算的精度。因此前轴实际支撑条件下的有限元模态分析是很难实现。所以基于以上几个方面的原因,本文采用自由边界支撑约束来对前轴进行有限元模态分析。
前轴模态分析的结果如表5-1所示。
表5-1 前轴的各阶固有频率
模态阶数 |
第一阶 |
第二阶 |
第三阶 |
第四阶 |
第五阶 |
第六阶 |
固有频率(Hz) |
97.3 |
173.8 |
278.0 |
352.1 |
446.1 |
549.1 |
对应的各阶次振型如下。
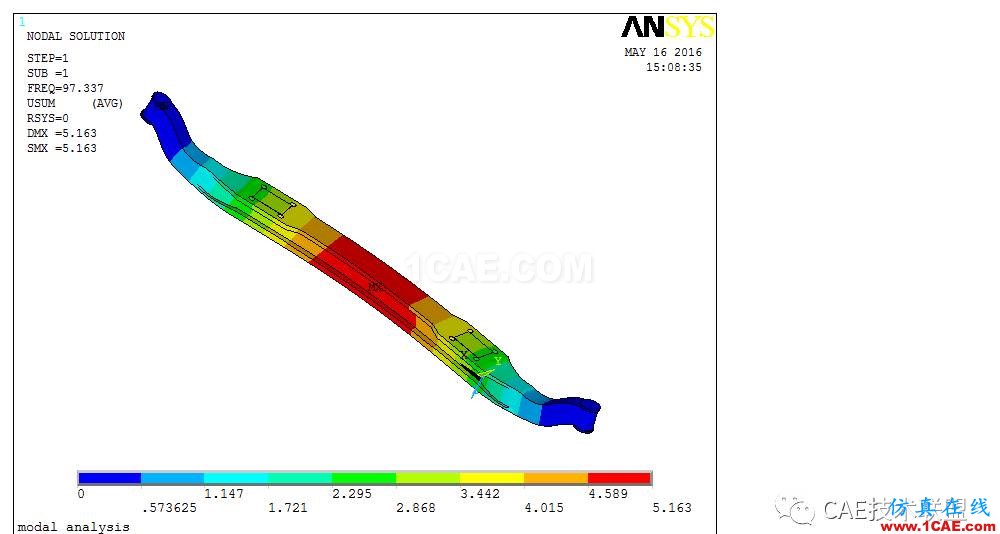
图5-1 前轴的一阶振型

图5-2 前轴的二阶振型
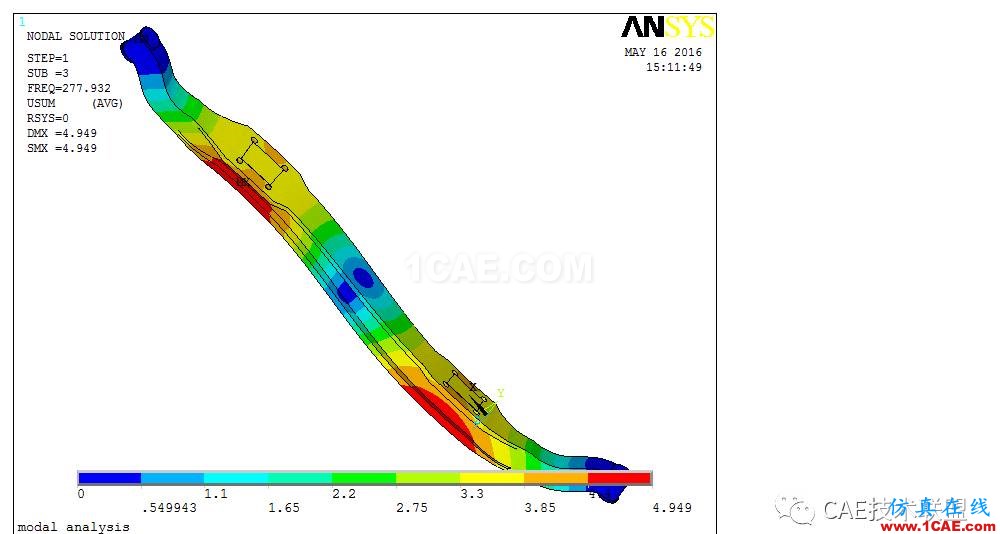
图5-3 前轴的三阶振型
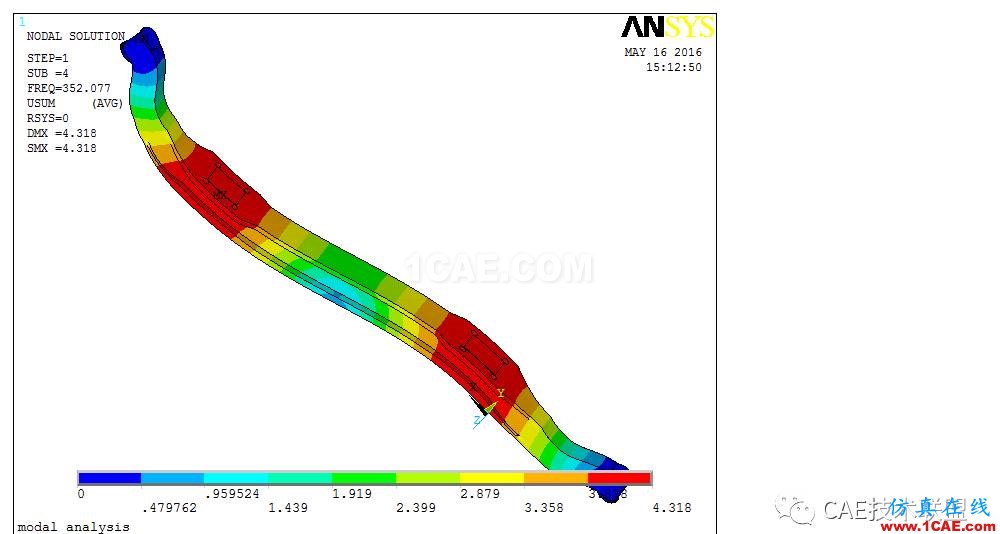
图5-4 前轴的四阶振型
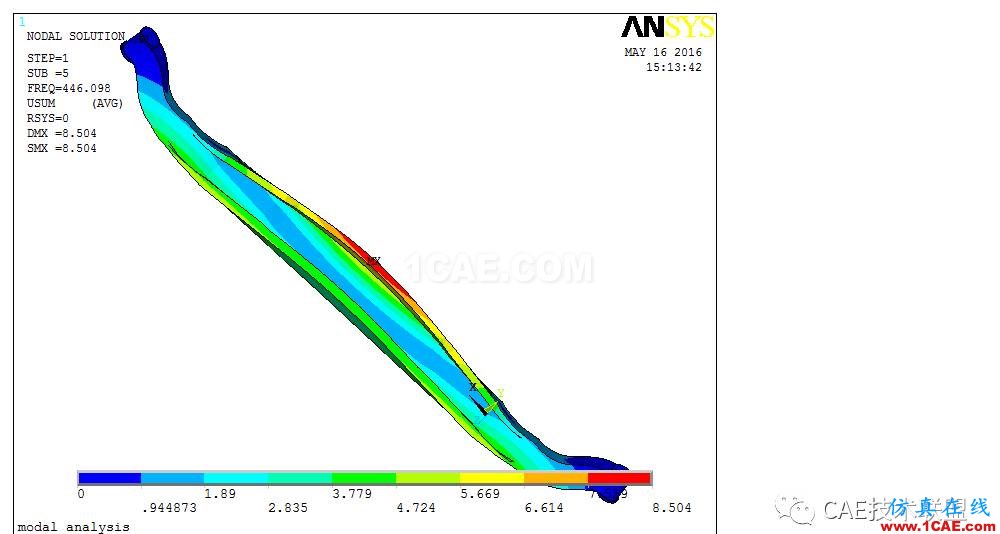
图5-5 前轴的五阶振型
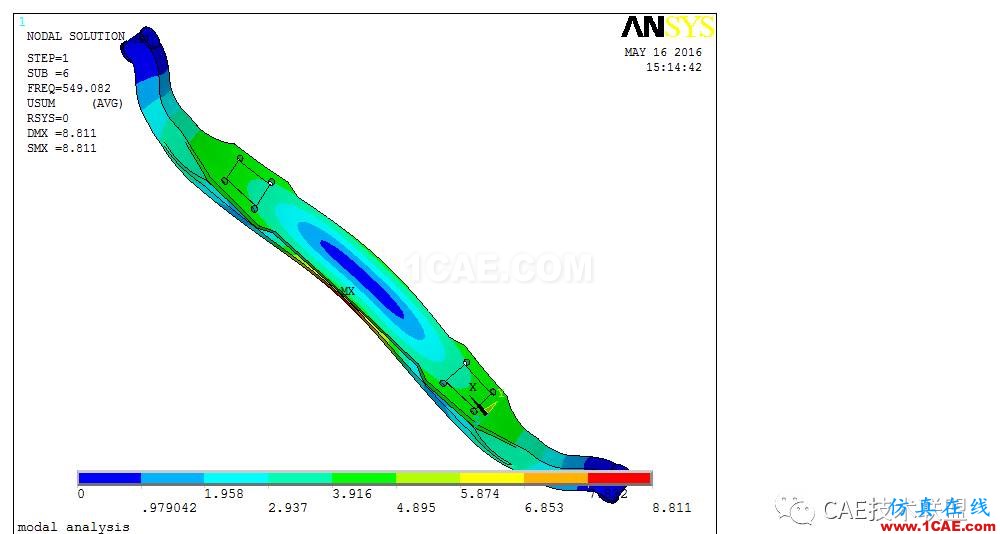
图5-6 前轴的六阶振型
从前轴的振型图可以看出,在一阶和二阶振型中,前轴由轴中心向上做较大幅度的振动,振动的频率较小,在97~174Hz之间;在三阶和四阶振型中,前轴由轴中心到主销孔之间做较大幅度的振动,其振动的频率在278~353Hz之间;在五阶和六阶振型中,前轴以轴心为中心,做较大幅度的上下振动和扭转振动,其振动的频率在446~550之间。
汽车行驶过程中,激励源产生的激励主要来自于路面、发动机、传动轴不平衡、车轮的不平衡以及车身车架等。路面激励由行驶的道路条件决定,在汽车通过不平路面时,路面引起的运动学激振大多是5~20Hz的垂直振动;而在高速公路和城市较好路面行驶时,此激励多在3Hz以下;由汽车发动机引起的激振可以由爆发频率公式计算得出,为23Hz以上;汽车行驶时经常使用的车速是80公里/小时;由传动轴的不平衡而产生的弯曲振动频率为46Hz左右;由车轮不平衡产生的激振频率一般低于11Hz;汽车的车身车架的振动频率约为80Hz。
由生物力学研究可知,人体全身垂直振动在4~8Hz范围内有一个最大的共振峰,称其所对应的频率为第一共振频率,此频率主要由人体胸腔共振频率产生,对人的胸腔内脏影响最大;在10~12Hz和20~25Hz附近的范围内有两个较小的共振峰,分别称其对应的频率为第二和第三共振频率,其中第二共振峰主要由人体腹腔共振频率产生,对人的腹部内脏影响最大。此外,人头部的共振频率约为2~30Hz,心脏的共振频率约为5Hz,眼部的共振频率约为18~50Hz,脊柱的共振频率约为30Hz,手部的共振频率约为30~40Hz,臀和足部的共振频率约为4~8Hz,肩部的共振频率约为2~6Hz,躯干的共振频率约为6Hz。而且振动还会影响人的视力,对视力的损害程度与振幅成比例,并且10~20Hz的振动频率对视力的影响最大。因此,在设计车辆(包括车身各部件)时,必须充分考虑人体的共振频率,采取有效的减振措施,尽量避免与人体产生共振效应。
综上所述,可知车身车架的固有频率与前轴的一阶固有频率较为接近,会在一定程度上影响汽车的平稳度和舒适度,但不会与车身车架发生共振。此外,由以上的频率分析可知:前轴的设计不会与路面发生共振,也不会与人体发生共振。
本文通过三维建模软件Pro/e建立前轴的实体模型,然后导入ANSYS进行前轴的有限元强度分析和模态分析,得出以下结论:
(1)利用现在已经比较成熟的三维建模软件如Pro/e进行实体建模,可以弥补ANSYS在建模方面比较薄弱的缺点,使实体模型的建立更加容易,提高工作效率。
(2)本文首先计算了汽车前轴在三种危险工况下的载荷情况,然后利用ANSYS软件分析前轴在三种危险工况下对应的应力分布和位移分布。由分析的结果可知:此轻型载货汽车的前轴在越过不平路面工况和侧滑工况下所承受的最大应力都比较小,安全系数较大,结构设计符合强度要求;同时前轴在此两种工况下的变形也远小于许用值,结构设计符合刚度要求。但在紧急制动工况下,前轴所承受的最大应力比较大,安全系数较低,存在一定的安全隐患;同时在此工况下前轴的变形量也较大,但是依然小于许用值,符合刚度设计的要求。
(3)前轴在自由条件下的模态分析表明,前轴本体的固有频率既不会与路面发生共振,也不会与人体发生共振,但是前轴的一阶固有频率与车身车架的固有频率接近,会对汽车的平稳度和舒适性造成一定的影响,但不会发生共振。但通过振型分析,得知外界激励对前轴的刚度影响也较大,因此有必要对前轴结构做进一步的改进。
虽然本文对轻型载货汽车的前轴做了较全面的有限元分析,而且取得了一定的研究成果,但是由于时间和自身水平的限制,还存在诸多的不足之处,需以后进一步加以完善。由本文的分析方法和分析结果,今后可以在以下几个方面对前轴作进一步的研究和改进:
(l)本文在整个前轴的分析过程中都采用的是线弹性分析,以后的工作可以结合非线性分析方面的理论对此轻型汽车前轴进行进一步分析,并将线性分析与非线性分析的结果进行对比,为前轴结构的完善提供更加充分的理论依据。
(2)由于本文整个设计还处在理论验证阶段,还没有进行实际的实验测试,因此今后的一个重要工作就是利用样车进行实际的实车测试,并将理论分析结果和实际实验结果进行比较,再对前轴的模型及载荷进行修改,使前轴的有限元分析结果更加符合实际。
(3)本文在对此轻型载货汽车的前轴进行有限元强度分析时,计算的各种工况主要是由相关的规定得出,各种参数是常用的经验值。为了获得前轴更加实际的分析结果,就应该结合多种动力学软件,建立整车的多种动力学模型,并将由此得到的各种分析结果进行比较分析,形成相对全面准确的分析方法。
综合自网络
相关标签搜索:【技术篇】基于ANSYS的汽车前轴强度分析和模态分析 Ansys有限元培训 Ansys workbench培训 ansys视频教程 ansys workbench教程 ansys APDL经典教程 ansys资料下载 ansys技术咨询 ansys基础知识 ansys代做 Fluent、CFX流体分析 HFSS电磁分析 Abaqus培训