熔模石膏型真空加压铸造技术 在大型复杂薄壁舱体铸件上的应用
2017-03-19 by:CAE仿真在线 来源:互联网
随着装备轻量化的加速发展,近十年来,为追求零部件的结构紧凑化,把原来由几个机加铝合金零件组装而成的部件,改用一个整体铝铸件来代替的情况日益增多[1-2],大型复杂薄壁铝合金铸件的应用已成为一种趋势。对于结构复杂(曲线型面、变壁厚、多筋多凸台等)、加工难度大和高承压能力的耐压构件,从减少铸件切削加工量、缩短制造周期、降低成本等出发,国外通常采用压力铸造、挤压铸造和熔模铸造等技术成形,而采用熔模石膏型真空加压铸造技术实现铸件的薄壁化浇注,可使铸件晶粒细化,致密度提升,组织及性能均得到明显改善[3-4]。
熔模石膏型真空增压铸造技术是专门针对航空航天装备中常见的一类复杂、薄壁整体结合和高气密性铸件而开发的一种新技术。该技术集成了熔模石膏型工艺中尺寸精度高、表面粗糙度低、薄壁化程度低和真空增压铸造技术中合金充填性能好、缩孔缩松程度低、铸件性能优良的优点,克服了传统铸造技术中尺寸稳定性不好、精度低、难以实现薄壁整体结合的缺点。目前熔模石膏型真空加压铸造技术已成功应用于航空航天铝合金薄壁铸件的工程化生产,不仅获得十分优异的铸件冶金品质,而且实现传统铸造技术难以企及的铸件合格率,熔模石膏型真空加压铸造技术已经成为大型复杂薄壁铸件铸造的重要手段。
2 熔模石膏型真空加压铸造技术原理及其特性
2.1 熔模石膏型的技术优点
熔模石膏型是将传统的熔模铸造法和普通石膏造型法结合起来的一种造型方法,兼有两者的优点,但也有其独特的地方,其特点为:生产周期短,铸件的精度高,表面质量好,且成本低,石膏铸型残余强度低,溃散性良好,利于铸件清理,生产的铸件具有尺寸精度高,表面粗糙度小和结构复杂等特点。
(1)尺寸精度高,表面粗糙度小
熔模石膏型真空加压铸造采用了尺寸精度、表面光滑的可溶性模,而获得了无分型面的整体型壳,且避免了一般铸造方法中的起模、下芯、合型等工序所带来的尺寸误差,铸件的棱角清晰,尺寸精度可达CT4~CT6级,表面粗糙度可达Ra0.8~1.25μm。因此熔模石膏型真空加压铸造所生产的铸件,已接近于零件的最终形状,故可显著减少铸件的加工工作量,并节省金属材料的消耗。
(2)适用于铸造结构复杂的精密铸件
熔模石膏型真空加压铸造可铸造出结构复杂、精密,且难于用其它方法生产加工的铸件,石膏浆料流动性和复制性良好,石膏导热性差,有利于金属液充填,其生产不受拔模的限制,可铸造壁厚仅为0.5mm,铸孔最小孔径为1mm以下的小铸件和薄壁件,还可铸造重量大于1000kg,外形尺寸可达2000mm以上的大型铸件。可将原来由许多零部件组合的部件进行整体铸造,铸件成品率高,可达90%以上。
2.2 真空加压铸造技术原理
真空加压铸造是在真空吸铸、低压铸造及差压铸造的基础上发展起来的一种反重力铸造方法,是将真空浇注和加压凝固融为一体复合而成的一种铸造技术[5-6]。其机理有两个方面:一是通过真空浇注的工艺条件,避免浇注和充型过程中的卷气、窝气,消除铸件内部的侵入性气孔和大幅减少铝液表面氧化膜的产生,同时提供铝液充型时平稳流动和避免氧化膜夹杂降低铸件力学性能;二是通过对凝固中的铸件施加外力(立体加压的气压力),使凝固中的铸件产生液相金属的挤滤作用和已凝固的枝晶产生显微变形,从而提高冒口的有效补缩能力,保证铸件的致密性和强韧性;同时抑制铸件凝固时气泡的形成和增加氢气体在固态合金中的溶解度,保证铸件针孔度级别的优良,从而保障铸件的气密性和耐压性。
真空加压铸造设备示意图如图1,其工艺过程如下。
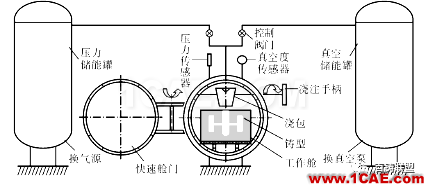
图1 真空加压铸造设备原理示意图
(1)铸型和装有金属液的浇包安置在工作舱内,并快速关闭舱门,实现工作舱的密封。
(2)启动设备,对工作舱抽真空,并在真空气氛下完成铸件的浇注、充型。
(3)对工作舱充压,并保压一段时间,使铸件在外加压力条件下凝固成形。
熔模石膏型真空加压铸造技术原理可归纳为一句话:真空浇注和加压凝固。真空加压铸造工作舱的铸型及金属液环境压力示意图如图2 所示(图中压力数值的零点以大气压力为准)。
图2 铸型及金属液环境压力示意图
2.3 真空加压铸造工艺特性及技术优点
(1)对金属液流动性的影响
真空浇注与大气压下浇注相比,金属液流表面张力降低、铸型型腔气阻小,金属液流动性大幅提高,由图3可知,提高1倍左右,十分有利于薄壁复杂铸件的浇注充型,保障铸件的顺利成形。
图3 流动性比较(材料:ZL114A,试样,同轴3R半圆蜗旋;型温,200±10℃;浇注温度,730±10 ℃)
(2)对力学性能的影响
弥散在铸件内部的氧化膜夹杂微粒数量多少的差异,如图4所示。大气下浇注时,铸件强度值波动大,而真空浇注时,强度值均在大气下浇注时的上限;当应力值一定时,铸件的疲劳寿命相差5~ 10倍。由此证明了真空浇注对改善铸件强韧性和疲劳寿命的显著效果。
图4 铸件疲劳强度对比(材料,ZL114A;疲劳试验,冲击试验)
(3)对铸件缩松的影响
加压凝固时, 由于外力对枝晶间间隔液相金属的挤滤作用和使初凝枝晶发生显微变形, 大幅提高了冒口的工艺补缩能力, 结果使铸件内部缩松得到改善(见图5);另外,还由于真空增压铸造法的加压方式是“立体加压”,不同于其他压力铸造“管道加压”方式,勿需整体补缩通道,克服铸件的缩松倾向效果明显。
图 5 加压铸造对棒状铸件缩松的影响(ZL114A,浇注温度720~730℃)
(4)对铝铸件针孔的影响
在铝铸件的生产中,由于合金液中溶解的氢原子在铸件凝固过程中析出氢气,最终在铸件内部形成针孔。针孔严重时铸件常因气密性和力学性能低下而报废。
首先讨论加压凝固对合金液析出氢气形成氢气泡的影响。
氢气泡形成的条件:
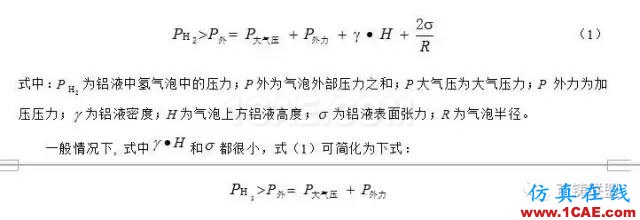
当增大“P外力”使PH≤P外时,就不能形成氢气泡。
另外,从图6 所示不同外压下气体在合金中的溶解度变化关系中可以看出,增加外压可增加气体在固相合金中的溶解度。
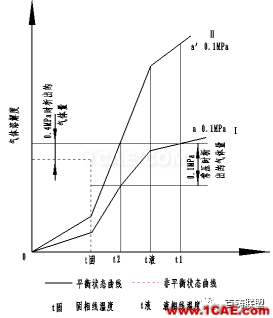
图6 不同外压下气体在合金液中的溶解度示意图
综上所述,熔模石膏型真空加压铸造技术通过采用先进的技术原理,综合并强化了各种反重力铸造技术的优势,为铸件的薄壁化、复杂化和高品质化提供了更为有力的保障。
3 大型复杂薄壁舱体铸件熔模石膏型真空加压铸造成形
3. 1 大型复杂薄壁舱体铸件成形关键技术
针对大型、复杂、薄壁、整体铝合金铸件铸造成形中共有的合金液充型困难、分散热节缩孔和缩松严重、分散热节和厚大部位针孔密集、变形及尺寸精度4大技术难点,就熔模石膏型真空加压铸造技术应用适宜性和相关技术进行讨论。
(1)合金液充型问题
根据产品结构特点、技术要求和影响合金液充型的3大要素:型腔气阻、合金液流表面氧化膜、铸型温度和导热率的全面分析可知,采用真空浇注技术,再融入可热模浇注、热导率低的石膏型工艺及分散内浇道方案,即可使狭长、复杂型腔合金液充型困难的问题得到极大的改善。
(2)分散热节的补缩问题
铸件表面积大,平均壁厚小,且又有众多的分散热节,难以建立完整的顺序凝固温度场,分散热节补缩困难,极易形成缩孔、缩松等缺陷。对此,利用真空加压铸造法的立体加压,使铸件凝固过程中各个部位均整体受压,并设置相应的分散冒口等,便可有效地解决好对分散热节的补缩。
(3)针孔问题
复杂铝合金铸件除几何形状复杂外,其复杂的含意还包括了铸件的一些特殊功能要求( 如气密性、耐压性等) 。对一些有高气密性要求的铝合金铸件,常因铸件内部针孔严重、气密性性能低下,造成大量或成批报废。对此问题,在保证铝合金熔炼质量充分除气的情况下,在铸件整个凝固过程中对其立体加压,就可以充分保障铸件针孔度级别的优良。
(4)变形及尺寸精度问题
因超大型的尺寸,使合型、下芯十分困难,而且更难以保证位置、形状尺寸的精度。对此,可采用预制整体石膏型芯—带石膏型芯的超大型熔模—外形石膏型的铸型制备工艺。
3.2 大型复杂薄壁舱体铸件成形工艺设计
3.2.1铸件蜡样成形
快速成形工艺主要用于大尺寸薄壁及复杂精密构件关键模具的快速成形,适用于成形难度大的复杂结构件及新产品的开发,在提高大型精密复杂模具制造质量、短时间内实现模具快速制造和修复、新产品新工艺试制等方面具有突出优势[7]。采用快速成型工艺制备出形状完整、轮廓饱满、表面质量和内部质量优良的大型复杂薄壁铸件蜡样如图7所示。
图7 大型复杂薄壁铸件蜡样
3.2.2 浇冒系统的设计
对铸件浇冒系统进行了初步设计,并通过MAGMASOFT软件对铸件铸造充型、凝固过程中的温度、速度、应力场及缺陷分布状态进行了模拟(铸件充型和凝固过程见图8),进而对浇注系统进行优化改进,获得了“多层过滤+多浇口短流程+凝固导向冷铁+分散热节补缩冒口”的铸件浇冒系统,如图9所示。
(a)充型速度场 (b)凝固温度场
图8铸件充型凝固过程模拟图
图9 铸件浇冒系统
3.2.3 铸型制备工艺
由于铸件三种舱体轮廓尺寸均较大,加上石膏传热慢的特点,焙烧阶段炉膛热量向铸型内部传递困难,内外温度的不同步导致型腔内外容易出现收缩率差异。铸件所选用的铸型材料为一种高强、收缩率稳定温度区间长、抗裂能力强的新型材料。
铸件铸型在灌浆结束后自然干燥24h,随后入炉进行干燥、脱蜡、焙烧,焙烧工艺曲线见图10。各温度梯度之间升温时间均为1h,降温为随炉降温。
图10 铸件铸型焙烧工艺曲线
3.2.4 真空加压铸造
为进一步保证铸件薄壁结构的顺利成形和厚大部位分散热节的充分补缩,同时,减少多浇道浇注系统的二次氧化和型腔反压,铸件浇注采用真空浇注、加压凝固工艺,试验确定的真空加压铸造主要工艺参数见表1。
表1 铸件真空加压铸造主要工艺参数
铸型温度(℃) |
浇注真空度(MPa) |
浇注温度(℃) |
加压压力(MPa) |
保压时间(min) |
350±10 |
-0.04~-0.08 |
760±10 |
0.8~1.2 |
4~5 |
铸件的真空加压铸造过程中浇注速度、工作压力(真空度)、铝液温度随时间变化的工艺曲线,如图11所示。
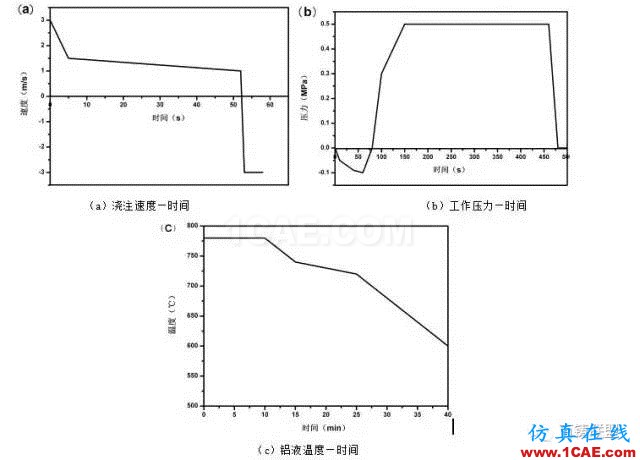
图11 铸件真空加压铸造工艺曲线
3.2.5 热处理工艺
为解决铸件大型薄壁壳体结构刚性差,常规热处理工艺铸件变形严重、校正困难的问题,采用“室温装炉—缓慢阶梯升温—上限长时保温—下限短时保温—热水水淬”的工艺进行铸件防变形固溶热处理,将铸件固溶处理变形量控制在±2mm以内,从而大大减小了铸件的校正变形量,保证了校正的安全顺利开展。试验确定的铸件热处理规范见图12。
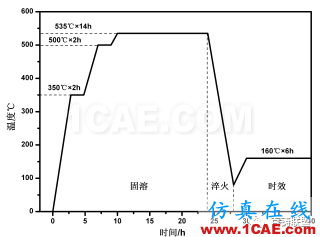
图12 铸件热处理工艺
4 结束语
采用熔模石膏型真空加压铸造技术能够铸造出力学性能好、致密度比较高的铝合金和镁合金等大型复杂薄壁铸件。但在铸件组织致密性、尺寸精度和检测技术以及铸造工艺优化等方面,还需不断研究提高,针对熔模石膏型真空加压铸造技术尚需进行的工作有以下几点:
(1)对熔模石膏型真空加压铸造技术的工艺特性参数进行系统的试验分析,建立应用 CAE所必需的真空加压铸造的合金热物性参数、凝固补缩特性参数的数据库。
(2)对熔模石膏型真空加压铸造设备的自动化、机械化、系列化进行系统的工程实验研究,使设备在工程化应用上更趋完善。
(3)对铸件的热处理规程进行系统的研究,建立铸件的热处理工艺数据库,便于采用变形最小的热处理规程。热处理后的铸件应采取振动时效处理等措施进一步释放其内应力,有利于适量机加精度的保证和尺寸稳定性的保持。
参考文献:
[1] 田锡惠. 导弹结构、材料、强度[M] . 北京:宇航出版社,1996.
[2] 鱼雷力学编写组. 鱼雷力学[M] . 北京:国防工业出版社,1992.
[3] 苏志权,孟照亮,孙昌建. 熔模石膏型真空加压铸造技术及其应用前景[J].四川兵工学报,2004,4: 16-19.
[4] 李新亚. 铸造行业国内外生产技术现状及发展方向[J].铸造,1999(增刊): 3-11.
[5] 柳百成. 铸造工程的模拟仿真与质量控制[M] . 北京:机械工业出版社,2001.
[6] 孙昌建,舒大禹,王元庆,苏志权. 大型复杂薄壁铝合金铸件的熔模石膏型真空加压铸造技术[J] .铸造技术,2008,29(2):232-235.
[7] 毕鉴智,曲万春,祝强,等. 差压铸造的应用与发展[J] .铸造技术,2000,2: 16-18.
本文来源于网络,文章中的观点归原作者所有,不代表本公众号。若侵权,请联系后台联系我们删除.
相关标签搜索:熔模石膏型真空加压铸造技术 在大型复杂薄壁舱体铸件上的应用 Ansys有限元培训 Ansys workbench培训 ansys视频教程 ansys workbench教程 ansys APDL经典教程 ansys资料下载 ansys技术咨询 ansys基础知识 ansys代做 Fluent、CFX流体分析 HFSS电磁分析 Abaqus培训