金属板料渐进成形工艺过程有限元模拟
2017-03-02 by:CAE仿真在线 来源:互联网
本文介绍了金属板料分层渐进成形过程有限元模拟。在金属板料渐进成形过程中,材料的弹塑性变形十分复杂,影响成形过程的因素很多,同时各个工艺参数对成形过程的影响又很难确定。为此根据金属板料分层渐进成形为多工步成形的技术特点,建立一种有限元模拟方案,对板料渐进成形过程进行模拟分析。
1.前言
板料零件数控渐进成形工艺是一种通过数字控制设备,采用预先编制好的控制程序逐点成形板料零件的柔性加工工艺。该工艺不需要专用模具,成形极限较大,重复性好,可控制金属流动,能加工出形状复杂的自由曲面,适合于航天、汽车工业等的小批量、多品种、形状复杂的板料零件加工,有着十分诱人的发展前景。但是迄今为止,国际上对数控渐进成形工艺的研究也只处于探索阶段,理论方面的分析较少且不成熟,对于该工艺的成形和控制方面还有待于发展完善。
随着有限元分析技术的飞速发展以及计算机性能的不断提高,一个融入了计算机图形学、数值方法、塑性成形理论与工艺等各类技术的模拟软件系统已逐渐成为板料数控渐进成形研究及成形优化的强有力的工具。
本文就引入有限元模拟技术对板料零件数控渐进成形工艺的成形过程进行模拟方面的探讨。
2.金属板料数控渐进成形原理
板料零件数控渐进成形的加工过程如图1所示。数控成形系统主要由工具头(成形工具)、导向装置、芯模和机床本体组成。工具头在数控系统的控制下进行运动,芯模起支撑板料的作用,对于形状复杂的零件,该芯模可以制成简单的模具,有利于板料的成形。
成形时,首先将被加工的板料置于一个通用芯模上,在托板四周用压板夹紧板料,该托板可沿导柱上下滑动。然后将该装置固定在三轴联动的数控成形机上,加工时,成形工具先走到指定位置,并对板料压下设定压下量,然后根据控制系统的指令,按照第一层轮廓的要求,以走等高线的方式,对板料进行单点渐进塑性加工,如图1b所示。
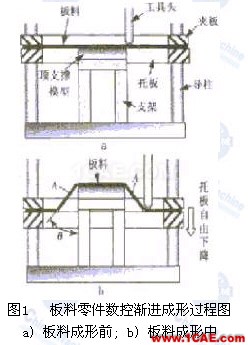
3.成形过程的计算机模拟
成形过程的特点决定了金属板料数控渐进成形的成形过程是一个同时包括几何非线性、材料非线性和边界条件非线性等问题的非常复杂的弹塑性大变形力学过程,其物理模型和数学模型都不同于传统的板料单次拉深工况下的模型,必须基于板料分层成形的特点进行分层成形过程的计算机模拟,采用大变形弹塑性非线性有限元法求解分析模型,获得工件成形过程中变形和应力的分布、成形力的变化、预测成形过程中可能产生的缺陷,为制定正确的成形工艺提供理论依据。
作为大型的通用有限元分析软件之一,ANSYS/LS-DYNA兼有ANSYS和LS-DYNA的优点。其强大的非线性功能、多种材料模型和较强的运动加载控制在模拟板料渐进成形方面具有很大优势。ANSYS后处理器可以很方便的将计算结果进行彩色等值、矢量图和梯度等多种直观显示。经过渐进成形后板料的应力场分布、板厚变化和各种工艺参数对成形结果的影响可以直观方便的显示,并可有效的模拟出板料渐进成形的全过程,为金属板料渐进成形过程中各种工艺参数的合理优化,有效地控制板料的变形过程提供理论依据。
下面对有限元模拟中模型建立、网格划分、加载和边界条件等关键方面进行分析。
有限元模型的建立和网格划分对于板料渐进成形工艺过程的有限元模拟来说,其建模过程不是很复杂。在ANSYS本身具有的前处理模块就可以对整个模型进行完整的描述。另外,ANSYS提供了与其他CAD软件的专用数据接口,能够实现与CAD软件间无缝的几何模型传递,对于较复杂的顶支撑模型可通过其他CAD软件导入。
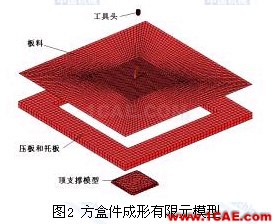
图2为模拟方盒件成形的有限元模型。
该模型由工具头、板料、托板和压板以及顶支撑模型四部分组成,能够较好的完成对整个成形过程的模拟。
建模的关键在于网格划分。网格划分中各种参数的设置将决定生成的模型在分析时是否能够满足准确性和经济性。通常情况下映射网格具有规则形状、排列有规律的单元,往往比自由网格得到的结果更加精确,而且在求解时对CPU和内存的需求也相对要低些。为获得这种规则网格形状,需要从建立几何模型开始就对模型进行比较详尽的规划,以使生成的模型满足生成映射网格的规则要求。同时对网格的疏密进行控制,在板料的塑性变形区采用较密的网格划分,而对没有参与变形的区域采用较疏的网格划分。在板料渐进成形工艺中,工具头按指定轨迹进行运动,板料每次产生的变形仅发生在成形球头的周围,对于几乎所有的金属(бb/бS≤2)其塑性区大小:
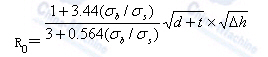
其中d为工具头直径,t为板厚,△h为工具头单层进给量。
因此网格细分区应在成形零件的外轮廓基础上有一个相应的偏移量T0,其中T0≥R0。另外,对不同的零件形状工具头所走的轨迹也有所不同,相应的板料网格划分也应采取不同的形式。图3为成形方盒零件和圆盒零件所采取的两种板料网格划分形式。
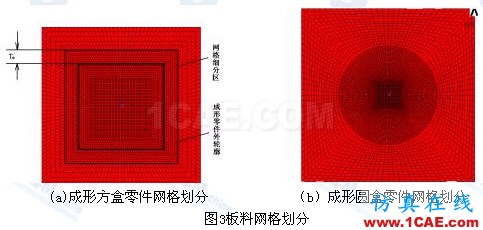
工具头的运动加载
由于工具头的运动轨迹多为空间曲线,用ANSYS直接模拟这样的空间曲线运动还比较困难,目前采用的方法是用若干较小的直线段对曲线进行分段逼近.每个直线段起点和终点均给以相应的坐标,坐标以相对位移增量的形式给出(相对于工具头初始位置),且每个坐标点对应一个时间点,这样即可完成对工具头运动轨迹的模拟。
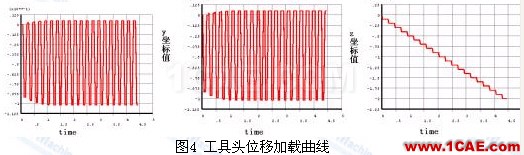
图4所示为成形方盒件时,工具头的位移轨迹加载。把X、Y、Z方向的位移增量表示为时间的函数,通过运动合成实现整个加载过程。
在工具头运动速度控制方面,为了减少计算时间,通常采用增加工具头运动速度的方法,在模具成形时,模拟速度一般为实际速度的100倍左右,在这里也沿用这一方法进行模拟,即缩短相邻两点间的时间间隔。多数情况下可获得较好的解,当出现与实际情况不符的解时,应适当降低模拟速度。
边界条件的处理
板料渐进成形过程中边界条件的处理也是比较重要的一环。在实际模拟中对板料的边界条件进行相应的简化,建模时板料和托架及压边框即固连在一起,实际上即相当与将板料被压边框压住的部分自由度全部限制住,仅给予托架沿Z轴(垂直)方向的位移自由度,对顶支撑模型约束所有的自由度,这样即达到与实际成形情况相符的目的。
模拟结果的后处理
后处理是指检查分析的结果,这是分析中最重要的一环。ANSYS本身自带有两个后处理器可用以显示和分析模拟的结果。POST1通用后处理器可以观察整个模型或模型的一部分在某个时间上针对特定载荷组合时的结果,可进行模拟结果彩色等值云图、梯度、矢量图等显示,以及各种结果数据的列表。可将成形板料的变形图以及应力、应变分布图显示出来。关键点的数据结果还可以列表显示保存。POST26为时间历程后处理器,可在瞬态分析中以图形表示产生结果项与时间的关系或在非线性分析中以图形表示作用力与变形的关系。可用该处理器将渐进成形过程中,板料变形随工具头运动的变化情况显示出来。另外LSTC公司开发的软件LS-POST作为后处理器兼具上述两个后处理器的特点,操作简单快捷。图5为板料渐进成形模拟及用LS-POST显示方盒件加工到第四层时的塑性应变图。
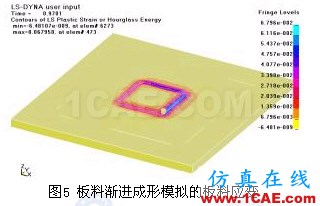
结束语
金属板料渐进成形不同于传统的整体成形,影响工件质量的因素非常复杂,金属板料渐进成形的有限元模拟可以对成形参数进行优化,对成形结果进行预测以及缺陷诊断,是改进这一成形工艺的强有力的工具。然而这一模拟还处于起步阶段,板料渐进成形是一个涉及多门学科的塑性成形过程,在使用有限元方法进行板料渐进成形过程模拟方面还需要在以下几个方面进行进一步研究:
(1)对工具头较复杂的曲线运动进行模拟还存在一定困难。目前大多进行规则曲面的模拟,因此在较复杂的轨迹加载方面需对ANSYS进行二次开发。
(2)对于模拟过程中影响板料变形的参数和成形结果之间的关系需进一步分析,如工具头的运动速度、单层进给量和边界条件等,建立影响板料变形的参数数据库,为优化模拟参数,预测板料变形提供理论依据。
(3)由于板料渐进成形的成形特点,决定了对其成形工艺过程进行有限元模拟时必然要耗费大量的机时,目前模拟方盒件20层成形需要上百小时,因此需对诸多影响模拟时间的因素如最小时间步、网格划分、工具头的速度控制以及建模规划等方面进一步研究。
相关标签搜索:金属板料渐进成形工艺过程有限元模拟 Ansys有限元培训 Ansys workbench培训 ansys视频教程 ansys workbench教程 ansys APDL经典教程 ansys资料下载 ansys技术咨询 ansys基础知识 ansys代做 Fluent、CFX流体分析 HFSS电磁分析 Abaqus培训