基于CAE技术的壳体轻量化【转发】
2017-11-01 by:CAE仿真在线 来源:互联网
1 引言
近年,很多学者对变速器壳体等机械零部件的轻量化做了大量的研究试验。陈黎卿等(1)采用微粒子群优化算法对差速器壳体进行轻量化设计。马闯等(2)对利用工程经验对汽车真空助力器的前壳体进行轻量化设计研究。宋春雷等(3)利用有限元技术对驱动桥的差速器壳体轻量化进行分析。彭帮亮等(4)利用拓扑优化技术对变速器壳体进行轻量化设计。由于目前新能源汽车对变速器的要求越来越高。例如轻量化要求,NVH要求、寿命要求、易维护性要求。有研究表明(5),油耗和汽车自身质量成线性关系,汽车质量的增加同时导致油耗和尾气排放量的增加。因此,汽车轻量化是解决汽车工业发展和能源、环境之间矛盾的有效途径之一,也是目前各主机厂商和零部件供应商研究的热点问题之一。而轻量化对变速器壳体的要求就是在满足强度、刚度等指标的情况下减少壁厚和增加加强筋等等技术手段。本文是对我司一款用于公交大巴和物流车的纯电动变速器壳体的轻量化所作的分析总结。
2.建立壳体有限元模型
目前由于变速器壳体结构复杂,受力不均匀,无法使用传统的解析法对壳体上任意一点的应力σi进行求解。所以本文采用有限元法来计算变速器壳体的强度。有限元法能对整个结构建立精确的模型并进行求解。它的主要优点是能够以三维可视化来准确体现结构的实际形状、约束情况和受力情况。在正确建模的基础上,不仅可以得到较准确的计算分析结果,而且还可以对整个结构的应力分布进行可视化观察分析。
应用有限元法对变速器壳体进行分析,通常包括以下三个步骤:
1) 有限元模型的建立(前处理);
2) 有限元模型的计算;
3) 有限元结果分析(后处理)。
我司一般根据针对变速器壳体的结构特点来确定划分网格的数量、节点的数量、求解的时间范围及精度等。在壳体前处理时对壳体进行一些合理的简化,以减少隐式计算方程的个数,加快有限元模型的求解速度和精度。
该变速器壳体包括前壳体和后壳体两部分,前壳体和后壳体之间的连接采用螺栓连接,在分析模型中使用刚性单元模拟,而壳体内部的轴承孔处使用rbe3单元代替轴承。而约束方面是前壳体与电机接合面之间的螺栓连接和悬置处的螺栓连接均采用刚性单元模拟。模型采用四面体单元做网格划分,平均单元为5mm、最小单元为1mm。在螺栓连接面及重要部位均采用合适的网格加密。
前处理步骤:
1) 简化处理CATIA模型(具体措施例如删除螺栓孔倒角、油封倒角、装配倒角、删除标签号码等);
2) 导入到前处理软件Hypermesh里;
3) 根据企业网格标准建立部件网格;
4) 定义壳体材料、属性;
5) 添加壳体约束;
6) 导入到Romax获取载荷;
之后就可以提交给求解软件NASTRAN计算,然后计算完成的结果可以在Hyperview等后处理软件中查看编辑。
2.1材料参数
原变速器壳体材料选用铝合金ZL101A、新变速器壳体材料选用铝合金ADC12。材料属性如表1所示。两种材料均属于塑性材料,常见失效方式为屈服。
表1 材料参数表

屈服失效常用畸变能密度理论来进行判别(6)。该理论认为畸变能密度是引起屈服的主要因素。即认为无论什么应力状态,只要畸变能密度达到与材料性能有关的某一极限值,材料就会发生屈服。
畸变能密度屈服准则为:
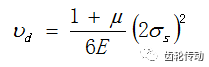
(1)式中,υd为畸变能密度,μ为泊松比,E为弹性模量,σs为屈服强度。
在任意应力状态下,畸变能密度计算公式为:

(2)式中,σ1、σ2、σ3为单元体的主应力。
将式代入式中,得到屈服准则为:
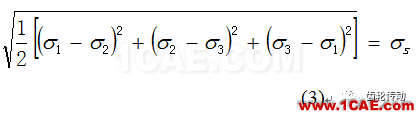
把σs除以安全系数得到许用应力[σ],于是畸变能密度理论的强度条件(Humber—Mises—Hencky屈服条件)是:
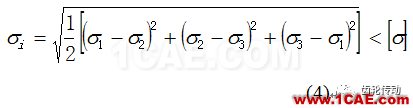
式中,σi为壳体上任意一点的应力,[σ]为材料的许用应力,其计算公式为:
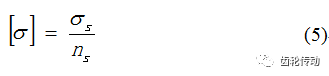
式中,ns为壳体材料的安全系数。
2.2 边界条件定义
2.2.1 载荷
变速器所受载荷有自重、轴承支撑反力、悬置载荷以及外部其他载荷等。
由于自重对变速器壳体的影响很小,所以在本文中不考虑自重因素。
轴承的支撑反力,是由输入轴、输出轴。中间轴以及各档齿轮组上的力产生的作用力引起的。该变速器最大输入扭矩为450N.m,一般定义扭矩安全系数为1.5,得出675N.m为计算扭矩,然后根据传动分析计算软件Romax计算各档工况最后得出一档工况最恶劣。在Romax中的计算过程是:先建立轴系(输入轴总成、中间轴总成、输出轴总成),再进行各零部件的空间定位,之后将载荷工况输入计算,然后将Hypermesh中划分完的网格以BDF格式导入到Romax进行刚度矩阵的缩聚,之后将具有轴承受力状况的文件以DAT格式导出到FEMAP计算。在其中刚度矩阵是一个重点。在有限元分析中基本方程式为

式中,[K]称为刚度矩阵。刚度是表示物质形变能力的一个量,此处被用作计算加载载荷后的壳体变形量及单元变形引起的应力变化。从理论角度来说,倒档工况由于该变速器为纯电动汽车变速器,电机能反转,不需要惰轮,并且考虑到壳体基本是轴对称模型,倒档工况占比很小并且扭矩小于1档工况,所以可以用1档工况代替。而二档、三档、四档的速比比一档小,所以不需考虑这几个档位的工况。所以本文考虑工况为一档工况675N.m下变速器的强度指标。动力传动路线见图1。
外部其他载荷主要是悬置对壳体产生的,由于主机厂未提供载荷要求,所以未考虑加载加速度对变速器壳体的要求。

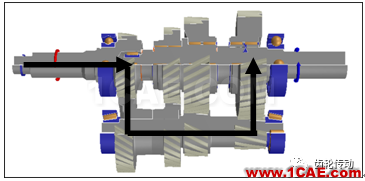
图1 动力传动路线
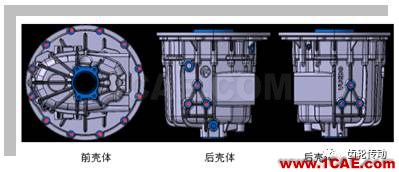
图2 约束点位置
2.2.2 约束
悬置处6个螺栓连接定义为6个自由度全约束。而前壳体和电机由于通过接合面的螺栓相连,后壳体和悬置通过两侧螺栓相连。考虑到不进行壳体接合面密封性校核以及螺栓预紧校核,所以螺栓连接均采用RBE2模拟,并定义6个自由度全固定,壳体约束点位置见图2。
3.1 静态结果分析
从Femap计算出的结果文件导入Hyperview中后。从原前壳体的应力云图上可以得出如下结论。
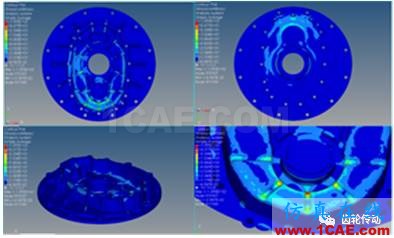
图3 原前壳体应力原图
原前壳体的两个轴承孔中的中间轴前轴承孔处为最恶劣受力处。原前壳体应力主要集中在前壳体内腔支撑中间轴前轴承的三根加强筋处,见图3,最大应力为105MPa。根据评估原前壳体内腔上的3根加强筋对支撑轴承处的轴向力作用不是很明显。
轴承径向方向上,原前壳体外腔的中间轴前轴承孔外腔突出基准面18mm,有效支撑轴承的宽度即壳体轴承孔轴向厚度仅有13.1mm。在中间轴前轴承的整个宽度范围内缺少有效支撑。而轴承轴向方向上,特别是在孔末端承受轴向力的位置缺少有效支撑,没有加强筋且壁厚只有7mm,不能对轴向力的分担起作用。外腔由于没有加强筋,所以在中间轴前轴承孔外腔凸出基准面的圆角过渡区域有平均大小为58~70Mpa的应力。
而原前壳体输入轴轴承孔处的几个加强筋均显示出较富余的强度,考虑可以减少筋的厚度。
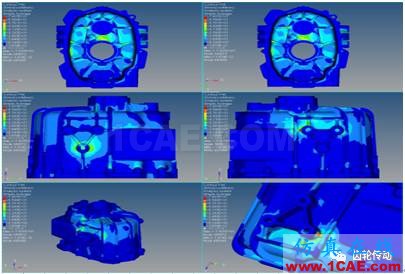
图4 原后壳体应力原图
原先的后壳体应力主要集中在两个悬置的加强筋处和壳体上输出轴后轴承孔的加强筋,见图4。
从受力分析得出后壳体的两个轴承孔中的输出轴后轴承孔处为最恶劣受力处。最大应力为74MPa。符合材料要求。
3.2 模态结果分析
模态分析是研究结构动力特性一种方法,一般应用在工程振动领域。其中,模态是指机械结构的固有振动特性,每一个模态都有特定的固有频率、阻尼比和模态振型。分析这些模态参数的过程称为模态分析。按计算方法,模态分析可分为计算模态分析和试验模态分析。
本文所做的分析是计算模态分析,是由有限元方法计算得到的。
在有限元分析程序中,振动方程表示为:

该方程作为特征值问题,对无阻尼情况,阻尼项被忽略,方程可简化为:

其中2(固有频率的平方)表示特征值;{u}表示特征向量,在振动的物理过程中表示振型,指示各个位置在不同方向振动幅值之间的比例关系,它不随时间变化。对于有阻尼的情况,振动方程可转化为:

以上各式中:[M]为结构的质量矩阵;[C]为结构的阻尼矩阵;[K]为结构的刚度矩阵;{u}为结构的位移列阵;


模态分析就是求解振动方程的特征值即特征方程的根
相关标签搜索:基于CAE技术的壳体轻量化【转发】 Ansys有限元培训 Ansys workbench培训 ansys视频教程 ansys workbench教程 ansys APDL经典教程 ansys资料下载 ansys技术咨询 ansys基础知识 ansys代做 Fluent、CFX流体分析 HFSS电磁分析 Abaqus培训