基于的Autoform的连续变截面板冲压分析
2016-11-11 by:CAE仿真在线 来源:互联网
随着汽车行业对节能、降耗的愈加重视,在实现大,使得零件调试难度增加,降低了企业生产效率。汽车轻量化方面有其独特优势的变截面板应用更广,逐步打破了传统的汽车用板材一般是都单一材质、同厚度的现状。变截面板的最大特点是厚度、材质的非均匀性。目前变截面板主要分为两大类:激光拼焊板和连续变截面辊轧板。
连续变截面辊轧板是利用近几年新兴的柔性轧制cae仿真技术,通过计算机实时控制和调整轧辊的间距来获取沿轧制方向上按预先定的厚度连续变化的板材。应用连续变截面辊轧板做车身覆盖件时,需要在车身设计阶段考虑到加工中钢板各个部位的实际受力和变形以及整车的承载情况,从而确定覆盖件的厚度变化范围。例如可以在覆盖件受力较大或成形变形较大的部位增加板料厚度,既保证了车身整体刚度又实现了汽车轻量化的目的。虽然连续变截面板有其独特的优势,但成型过程与模具设计方面的问题限制了其实际推广。
目前等厚板材冲压成型有限元分析与模具设计已经相当成熟,变截面薄板可以借鉴等厚板材的分析、设计、制造经验。同时又需总结材料自身的特点,建立新的设计准则。对于连续变截面薄板的冲压仿真,由于厚度的连续变化造成板料变形模式,数学模型等都与等厚板不同,导致仿真的结果与偏差较大,使得零件调试难度增加,降低了企业生产效率。因此建立适合变截面板料的冲压方法对于其应用相推广有重要作用。
本文以某前纵梁零件为例,提出一种基于Autoform连续变截面板冲压分析方法。
板斗成形数值模拟理论
Autoform软件是目前最为通用的板料成型有限元软件,采用隐式算法。在静态隐式算法中,认为板料成形是一个忽略惯性力的准静态过程。
目前常用牛顿法和修正牛顿法来求解非线性方程组问题,牛顿法在每次迭代中都需要形成一个新的刚度矩阵,效率较低。在修正牛顿法中,在每一次迭代中用位移增量对几何构型进行修正并计算一个新的载荷,节省了形成刚度矩阵的时间,效率较高。这两种方法有各自的优缺点,牛顿法的可靠性更高,但是修正牛顿法的计算效率更高。
CAE分析算列
如图1为某车型纵梁零件,该零件由连续变截面板冲压成型,板料厚度从两端的过渡到中间部位0.7mm。表1列出了TRB材料属性,其材质为H420LAD高强钢。
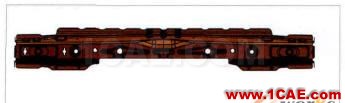
图1 零件图
零件工艺方案确定
参考等厚板材冲压技术分析本零件,此TRB纵梁要经过拉延、修边、整形、冲孔等工序。
1.压料面
压料面是工艺补充的重要部分,对拉延过程起重要作用。拉延时,凸模的成形力与压料面上的阻力共同构成毛坯的成形力,使毛坯产生塑性变形。其设置是否合理,直接影响到压料面毛坯向凹模内的流动方向与速度、毛坯变形的分布与大小、破裂和起皱的产生等。由于此纵梁零件有凸缘边,通常会以凸缘为基准,外延部分距离生成压料面。
2.工艺补充
工艺补充部分对拉延有重要影响,其直接影响到拉延成形时工艺参数、毛述的变性条件、变形量大小、变形分布、表面质量、破裂、起皱等质量问题。通过考察此零件的外形特征,考虑采用两段开口的方式拉延,提高材料利用率。另外,在侧壁部分的工艺补充,添加处加强筋以提高零件的拉延充分性,减少回弹量。
拉延工艺造型由分析师借助三维造型软件NX完成,建立好点的工艺造型型面如图2。
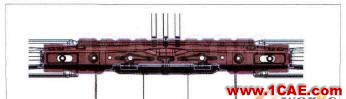
图2 拉延造型
有限元模型的建立
将在NX中建立好的工艺造型面,以IGES格式导入Autoform中进行冲压仿真设置。
1.拉延筋设置
拉延筋调整和控制材料流动,对板料成形工艺影响较大。本次模拟采用虚拟拉延筋,拉延筋分布及参数如图3。
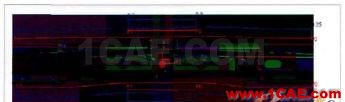
图3 拉延筋布置与参数
2.板料分段
根据TRB材料厚度连续变化的特点,本文提出了通过设置板料分段呈阶梯均匀变化近似模拟真实板料的连续变化过程。此厚度变化从两端的连续均匀变化至,故模拟时考虑以的单位大小呈阶梯型变化模拟实际板料的均匀变化,在Autoform中将板料分为等分通过中自带的激光拼焊功能将各个部分板料相连。
计算结果cae软件分析
设定好各项参数之后,提交Autoform计算。除了局部凸包与加强筋位置出现细微开裂风险外,其它部分均显示出合理的冲压结果。考虑到此TRB、纵梁U型截面形状及较高的屈服强度,其在成形后必定会有较大的回弹。在成形性分析完毕之后,添加回弹分析。回弹分析计算如图4所示。
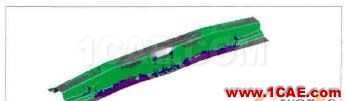
图4 纵梁成形性
由分析结果可知此零件产生了较大回弹,在零件侧壁位置甚至形成了2个凹包,凹陷有1.5mm左右,这与实际生产的零件状况较符合。
相关标签搜索:基于的Autoform的连续变截面板冲压分析 Autoform分析培训班 Autoform汽车模具仿真 Autoform视频教程 Autoform资料下载 在线软件培训 汽车钣金代做 Fluent、CFX流体分析 HFSS电磁分析 Ansys培训 Abaqus培训 有限元培训 Solidworks培训