汽车车身模具质量控制是怎么做到的?
2016-11-16 by:CAE仿真在线 来源:互联网
汽车覆盖件模具,凸模和凹模之间的型面间隙,是由凸模和凹模型面加工精度所决定。加工精度不仅影响钳工的修抛效率,而且影响上下模研合率,直至影响模具最终的质量。所以,模具的上下模型面加工到位,是“二次加工”NC加工到位的一个主要内容。
经过近几年的实践,NC加工后,研床间隙研合确认,统计分析,再调整数控机床刀具的加工参数。目前,一般复杂的汽车覆盖件模具型面,上、下模型面分别经NC加工后,经合模研床确认,着色还比较均匀。但这仅解决了间隙不均和需钳工大量研抛的问题。要想解决NC加工后,上、下型面料厚间隙95%~100%区间的精度问题,还相差的甚远。这个区间精度问题的解决是一个很复杂很难稳定保持的问题,影响的因素甚多,且很敏感。如:刀具的磨损、每次对刀精度、加工的让刀现象、前面说的主轴振动,另外,对于大型模具上下模加工,刀具起始点和走刀轨迹的编程工艺问题等,目前我厂正在实践和探索中。
汽车覆盖件模具数控加工的在线测量是通过统计、分析、总结经验来调整数控加工参数,是近几年的新做法。我厂也开展了几年,收到了很好的效果。
在此过程中,我们做了两件事:一是定心冲头;二是刃口轮廓间隙。前期,我们在推广定心冲头使用时,追求上下模分别加工后合模的正确率。另外,在推广刃口模加工精度、追求上下模分别加工后合模刃口轮廓间隙的正确率时,主要用于孔位加工和轮廓加工两个方面。目前,这种方法已成为加工过程质量控制的一种自检方法,但仍存在一弊病,在线测量占用机时很严重,影响机床的使用效率,所以,孔位要求下模逐一检查确认,轮廓仅抽点检查确认。
常世平先生:制造精度在模具开发过程中主要有两种作用:1、制造精度对工艺和结构设计起保障作用,没有高精度加工再好的模具设计也无法实现。反之,没有高精度的加工,工艺设计和模具调试之间的反馈就被切断,也就不能实现工艺设计的提高;2、制造精度对模具的质量起保障作用,决定模具工作的稳定性和寿命。
采用数控加工、采用高速高精度加工是提高制造精度的第一步,相对比较容易,现在国内模具企业都已经认识和做到了这一点。但要达到制造高精度,并不是自然而然的事。保持机床刚度精度的稳定性、选用高精度高刚性刀具、刀具管理、加工参数的优化、高精度编程、铸件的热处理、提高标准件精度等,都需要很高水平的技术管理工作和大量的人力、资金投入。而我们的大多数企业都还远没有认识到,因此也不可能做到,高制造精度还停留在愿望阶段。举个例子:大型模具的上下模配合精度要求公差在0.02~0.03mm水平,而我们的机床定位精度、刀具摆动精度、刀具几何精度、工件找正精度甚至环境温度变化造成的工件收缩变形都属于同一数量级,在这些误差的累计和叠加下,怎么保证加工精度要求?确实不是件容易的事。高制造精度又是高质量模具的基础,因此,国内企业必须下大力量首先解决这个问题。
CAE是提高冲压件品质的关键技术
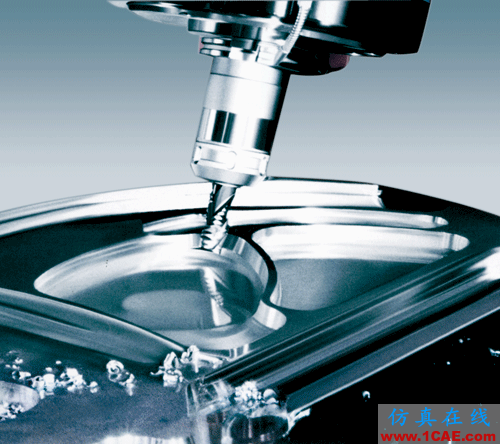
天津汽车模具有限公司总工程师常世平先生
常世平先生:关于冲压件质量是模具质量的关键因素前面已经说了很多,但怎样提高冲压件质量?在现阶段主要是运用好CAE技术。目前CAE技术在国内一流模具企业中已经普遍得到了运用,但不同企业对该技术的认识和运用水平差别很大,大多数企业还属于被动的和作表面文章的阶段,没有把它当成模具设计和制造的推动技术。
大多数人认为CAE只是冲压成形的验证手段,而且对其准确性还将信将疑。这种认识过时了,现在的CAE技术已经非常成熟,可以达到90%甚至95%以上的精度,可以运用于工艺设计的全过程,直接指导模具的调试,保证制件的内在品质,大大提高工艺设计水平和效率。
例如:在车身设计阶段,利用CAE技术可以提高车身零件设计可靠性,减少车身设计阶段的失误。这对当前国内车身设计尤为重要,车身设计工艺性的好坏直接影响到模具开发的进度和成本。现在的CAE软件都在向辅助工艺设计方向发展:自动确定冲压方向、自动产生工艺补充面、坯料的展开等,使工艺设计过程极大的自动化。同时,工艺分析的内容也大大扩展:啮合线分析、棱线偏移分析、修边角度分析、成裕度分析、扭曲回弹分析等,几乎所有的成形缺陷都能得到事先考虑,保证了冲压件的内在品质,这些内容是人的经验根本无法作到的。一个好的CAE报告完全可以取代现行的DL图,而且做得更好更全面。同时,利用CAE报告直接指导模具的调试可以使模具调试作到心中有数,不走弯路。
目前,在那些已经运用了CAE软件的模具企业中,运用CAE技术的普遍问题是:
1、工艺方案人员没有与CAE技术结合;
2、没有利用CAE软件作辅助工艺设计手段;
3、CAE计算精度不够;
4、各种成形缺陷分析不全面;
5、没有信心坚持CAE下的高标准工艺设计
6、没有标准化的高水平CAE报告;
7、调试没有把CAE报告当作指导;
8、制造精度不够,对精细模面设计不支持;
9、没有形成调试结果与CAE分析的闭环过程等。
对那些把CAE软件看成是很神秘的企业,CAE只是少数专业人员的事,只作为成形设计的检验,就会让工艺设计人员感到只添麻烦不帮忙,结果使CAE作为招牌束之高阁。
当然,目前CAE软件在解决回弹计算方面还远不能满足要求,这是影响制件精度的最主要原因。同时,CAE软件只把辅助工艺曲面设计融合进来,而没有把解决缺陷的一些常用处理方法吸收进来,使CAE软件在某种程度上还是一个只挑毛病而不帮忙的角色。
总之,CAE技术的充分运用可以可靠地保证和极大地提高制件品质,CAE水平已经成为衡量一个模具企业技术水平高低的重要指标。
李树新先生:在冲压模具方面,CAE模拟仿真帮助我们优化设计,主要体现在以下几个方面:一方面是产品工艺性的优化;另一方面是模具工艺设计的优化再一方面是NC加工的模拟仿真。
板料CAE模拟仿真无疑是一个好帮手,它利用有限元分析理论,把板料塑性加工的实践经验和板料特性融入其中。从理论上讲CAE是为了解决前期产品工艺性和冲压工艺设计优化等问题,前景广阔。CAE的美好愿景和最高境界是模具的计算机调试,解决模具的“无调试”化,实现模具生产制造质量和效率的最佳化。
在实际中,由于CAE有限元理论和生产实际还有一定的差距,另外,加上应用水平的原因,特别是要想发现产品设计工艺性问题和模具冲压工艺设计问题时,首先应用CAE的前提是:产品数模在什么样的冲压工艺补充造型条件下模拟。优秀的冲压工艺补充需要有相当的工艺知识和技能经验作保证。经验越丰富,CAE模拟所走的弯路才能越少。
另外,它还是一个反复模拟逐渐逼近的过程,每一次模拟后的解析和解析后所采取的措施,是CAE模拟技术的核心。最逼近是最好的结果,从理论上讲,就是CAE有限元理论和实际之差。再加上实际中还有加工精度、压床精度等因素的影响,所以模具的“无调试”化还是个理想。
NC加工模拟仿真主要是对编程员的程序质量进行模拟检查的过程。有两方面的内容:一是检查、确认程序的走刀轨迹能否满足质量精度要求,评审是否有异常跳刀的可能;二是检查、确认程序加工过程中刀具、主轴与工件是否干涉,也就是平时常说的干涉检查。
王正雄先生:目前,我厂CAE使用的软件是DYNAFORM,正处在由培训提高向实际应用转化的阶段。NC加工模拟仿真方面一直应用美国UGS公司的软件,加工部分带有模拟仿真软件,效果还比较理想。
我公司目前采用的模拟仿真工具软件是AUTOFORM,该软件提供了一个从产品概念设计到最后模具设计的完整的解决方案,其主要模块有User-Interface(用户界面)、Automesher(自动网格划分)、Onestep(一步成形)、Die Designer of Process(工序模面设计)、Incremental(增量求解)、Trim(切边)、 Hydro(液压成形) 等,该软件特别适合复杂的深拉延和拉伸成形模的设计、冲压工艺和模面设计的验证、成形参数的优化、材料消耗的最小化、新板料(如拼焊板、高强度板)的评估和优化以及成型件的回弹分析等。
我公司从2001年5月引进该软件,经过几年的应用和开发,在拉延成型类零件模拟分析、冲压零件可冲压成形性分析、冲压零件毛坯展开计算、零件回弹分析、工序模面设计等方面得到了广泛的应用,效果理想,保证了模具的最终质量。
影响模具使用寿命的关键因素
王正雄先生:模具材料的选用和热处理工艺是否适当对模具的使用寿命有着十分重要的影响,不同材质的模具寿命往往不同。冲压模具工作时要承受冲击、振动、摩擦、高压和拉伸、弯扭等负荷,工作条件比较复杂,模具零件易发生磨损、疲劳、断裂、变形等现象,因此,对模具工作零件材料的要求比普通零件要高。
冲压模具工作零件材料有两点基本要求:
一、使用性能好。具有高硬度(58~64HRC)和高强度,并具有高的耐磨性和足够的韧性,热处理变形小,有一定的热硬性;
二、工艺性能好。具有对各种加工工艺的适应性,如可锻性、可切削加工性、淬硬性、淬透性、淬火裂纹敏感性和磨削加工性等。通常根据冲压件的材料特性、生产批量、精度要求等,选择性能优良的模具材料,同时兼顾其工艺性和经济性。
当然,不同类型的冲压模具因工作条件不同,对模具工作零件材料的要求也有所差异。如冲裁类模具,对于薄板料冲裁模具,其工作零件用材要求具有高的耐磨性和硬度,而对于厚板料冲裁模具,除了要求具有高的耐磨性、抗压屈服点外,还应具有高的抗弯强度和韧性。又如拉深类模具,就要求模具工作零件材料具有良好的抗粘附性(抗咬合性)、高的耐磨性和硬度、一定的韧性以及较好的切削加工性能,而且热处理时变形要小。
李树新先生: 材质无疑是保证模具使用寿命的首要因素,但同时还有与之相关的另一大因素——材料的热处理。 材质方面,因国内普及使用的材料种类少,另外,还有进口材料价格和成本的原因,一般用户没有特殊要求的,仍延袭用比较传统的选材习惯,仅在产品特征和结构特殊的地方,才不得以选用特殊材质或表面特殊处理。
另外,在用户有特殊要求或国外厂家订货有要求时,有些模具材料选用进口材料,如:刃口材料,修冲类的焊接刃口的焊条;拉延成形的合金铸铁;甚至要求严格的连模具的上下模板一般铸件和螺钉都要进口。这一方面说明了影响模具寿命的首要因素是材质,另一方面也说明了国内材料生产能力和水平与国外相比还有一定差距。
热处理方面,除材质不同外,国外一般在模具调试好之后,为了适应大批量生产,模具往往采要进行表面处理,以提高模具的使用寿命,同时,对冲压件质量也有提高和保证,如表面镀铬、表面渗氮、TD处理等。
常世平先生:过去国内的铸件品质不高,很大地影响了模具的使用寿命,近年来这种情况已经有了根本性的改观,特别是国内一流铸造厂无论是合金铸铁还是球墨铸铁、铸造空冷钢已完全能达到质量要求,不比进口材料差,但我们的模具材料表面处理工艺还有差距,比如:拉延模的电镀、表面渗氮、TD处理和表面高频淬火等技术都没有应用或有很大不足。
应该引起我们重视的是,模具冲压工艺设计、模具刚度设计、模具制造精度以及模具材料的表面处理也是影响模具寿命的主要因素。一个好的设计方案,应该使制件成形容易、模具结构简单,这可以降低模具工作表面的摩擦,大大地延长模具使用寿命。另一方面,模具的精度和刚度不好,常常造成模具变形,引起模具的加速磨损,是极大的缩短模具寿命的元凶。
什么是真正的模具质量?
常世平先生:一提“产品质量”,人们往往想到的是一些数字,即各种各样的质量指标,但对于单件生产的订制产品来说,用户或供应商都很难把质量用一组单纯的数字表述。其实汽车覆盖件模具的质量也像其他产品的质量问题一样,满足用户的需求是最根本的质量。
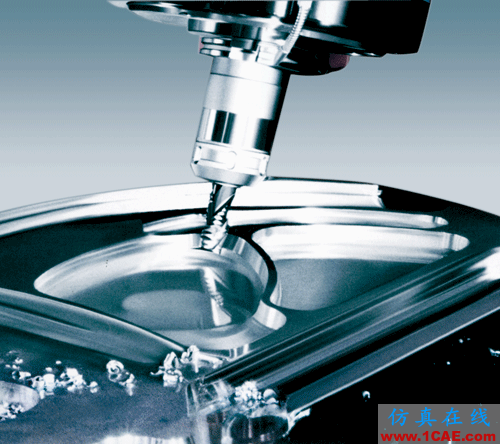
但模具作为工装设备,用户的需求可分为直接用户需求和最终用户需求。
直接用户需求主要是使用要求,模具的实用性、操作性、可靠性、维护性和寿命等要求。操作性包括模具的交换调整时间、人工操作的方便程度、自动化操作的适应和可靠性、废料的排出、冲次/分钟等。可靠性包括对冲床性能变化的适应裕度、平均免维护冲次等。
维护性包括易损件的互换性、维护的简单方便等。模具的寿命要满足车型的整个生命周期和车型退市后的售后服务需求。
国内以往的冲压模具绝大多数都是人工操作的低速冲压,如何生产满足相对高速的自动化冲压线模具就成为提高模具结构设计水平面临的桃战。又比如:满足模具自动快速更换,模具与自动化冲压线的同步配合,冲压20次/min以上时的废料排出问题,自动冲压线的动态干涉问题,大批量高速冲压模具的稳定性和平均无故障时间问题等,这些问题都要求我们对自动化高速冲压特性有充分的认识,以提高我们的模具设计水平,更好地满足用户的需求,进而达到模具质量的要求。
模具的最终用户需求主要是产品性能要求。模具的最终产品是冲压件,这就要求用模具生产出的冲压件的成本、精度、面品、刚度等满足要求。对大规模生产来说,模具设计首先要解决材料的利用率、适应高冲次等直接关系到制件的成本问题。同时,模具对不同的车型能提供不同的精度、面品、刚度要求的冲压件。这些问题对中国的模具企业来说都是新问题,也是直接影响模具质量的大问题。
对于模具来讲,用户还有一些特殊需求,比如:用户的认知水平和使用习惯,车型开发整车协调中的模具修改等。
总之,对用户需求的了解和适应,模具设计和制造的针对性是提高质量的关键,把模具的质量问题简单地归为模具材料和模具精度的提高并没有找到问题的根本。
高质量的冲压件是模具要实现的最终任务
李树新先生:模具的最终任务是冲压出高质量的冲压件。目前,在塑性加工过程中,最难解决和最棘手的就是应力、应变所引起的扭曲、回弹等变形现象,所以说板料的塑性加工,更确切地说应该是塑性变形和弹性变形的复合体。
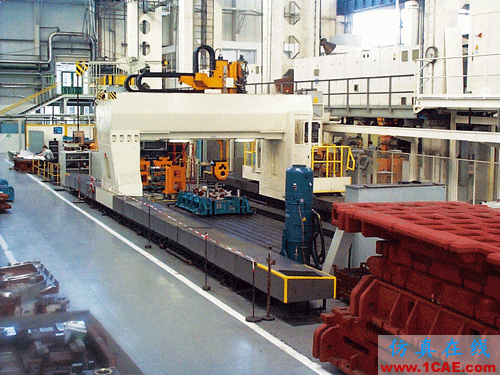
如何准确地判断冲压成形板料塑性加工的应力分布是解决应变的重要基础。在现实的生产实践过程中,由于冲压件产品形状复杂,不同材质的板料在同一产品制件成形中所产生的应力不同,因此,应变也不同。目前,我们只是凭经验作定性分析,给出一定冲压余量,作业冲压产品的缺陷预测,并制定预防措施。这些措施有些是在冲压工艺方案上实施,有些是在模具结构上实施,有些是在产品数模再设计环节中实施。
改变产品数模,局部预留冲压余量,达到最终冲压产品缺陷预防的作用,这些正是塑性加工理论难以定量解决的问题,也是模具行业技术领域高深莫测之处。
目前,国外在此方面做法比较严谨。他们对难以把握的冲压产品,在作CAE反复逼近模拟分析后,通过制作概念车进行冲压工艺试验。经验加上试验最后得出的修正值,也就是所说的冲压余量才是比较准确和稳定的,也才能把该冲压余量最后移植到正规批量生产的模具上。这种严谨的做法无论是在产品设计开发,还是在模具的工艺分析、工艺设计上,投入的人力、物力都是巨大的,这就是为什么同一产品开发、工艺设计,国外的技术价值含量要比国内高很多的原因。目前,我厂有一些产品的冲压余量是凭经验给出的,如顶盖,也有一些产品则是通过调试、测量统计分析后,总结出不等变量的冲压余量,最终修正模具,落实到正规批量生产的模具上,如轿车天窗骨架、重卡左右保险杠侧板。
常世平先生:国内的汽车模具企业数量众多,这些企业在理念、技术、工艺、管理等许多方面都有很大的差异,企业处于不同发展阶段,面临的主要模具质量问题也各不相同,因此要针对各自特殊情况加以解决。但树立模具制造以用户需求为质量要求的理念,重视利用CAE技术提高冲压工艺水平,实现数字化设计制造,坚持通过高精度加工达到只装不配少修阶段,我们的模具质量一定会有一个巨大的飞跃。
相关标签搜索:汽车车身模具质量控制是怎么做到的? Autoform分析培训班 Autoform汽车模具仿真 Autoform视频教程 Autoform资料下载 在线软件培训 汽车钣金代做 Fluent、CFX流体分析 HFSS电磁分析 Ansys培训 Abaqus培训 有限元培训 Solidworks培训