侧围板料开裂及对应模具分析
2017-01-04 by:CAE仿真在线 来源:互联网
在我国汽车市场繁荣的今天,世界汽车巨头纷纷投资抢占市场,然而使用进口的原材料对于当前急需降成本的汽车企业来说却是一个相当重的负担。在汽车生产过程中,实现材料国产化,无疑是降低汽车生产成本的有效措施。但是,一辆汽车融合了诸多先进的生产技术,要想实现材料国产化,需要相关企业开展更广泛的协同合作。我厂在某车型的生产中,发现车身侧围导入国产化材料后,频繁出现开裂现象,尤其以右侧围最为严重。为了解决这一板料开裂问题,我厂技术人员通过对该车型右侧围展开的一系列试验分析,最终找到了解决此类问题的方法。
材料分析
为了更准确地找到侧围板料开裂的原因,技术人员对两厢和三厢汽车侧围材料进行了比较,开展生产调查。
通过实际生产调查,统计生产总量和残次品的数量,见表1。从表1中可以看出,车辆侧围缺陷主要是开裂和颈缩。经过现场调试,左侧围通过调整气垫压力或平衡块,问题可以消除;右侧围在添加了2次平衡块的垫片后,依然开裂,问题没有解决。
产品的数据分析
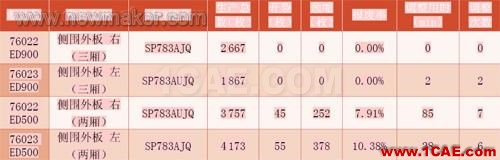
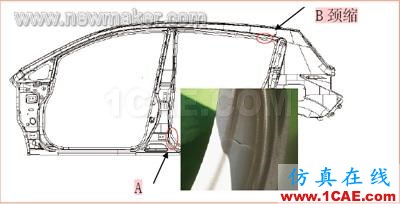
图1 两厢车侧围板料开裂
不同车型左右侧围A处数据
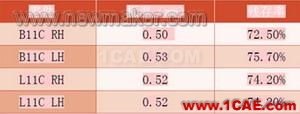
模具状态调查
该车型侧围零件在生产中由4道工序完成,分别是PB,拉延成形;PC,二次成形,修边(工艺补充的切除);PD,二次成形,修边冲孔;PE,翻边,冲孔。
1.PB模的结构
拉延模基本上由三大件组成:凸模、凹模和压边圈。拉延工艺可将平直毛料或工序件变成曲面形。凸模是冲模中起直接成形工件作用的凸形工作件;定位挡板决定材料的位置;平衡块可以调节上下模的间隙,起到约束力调整和吸料的作用;拉延筋控制材料的流动,调节进料阻力。模具结构如图2所示。
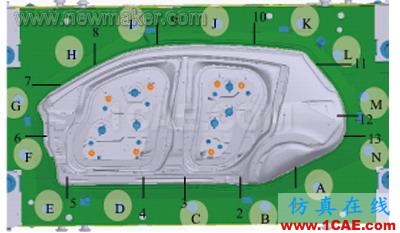
图2 模具结构
通过对圆形平衡块接触面积调查,得到如表3所示数据。从表3可以看出,平衡块接触面积均在30%以上,符合规定要求。
平衡块接触面积调查数据
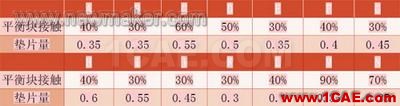
测量方法为:铅丝旁放40mm×40mm的方板,标准压力下进行冲压,测量冲压后的铅丝各部分厚度以获得拉延筋间隙。测量部位及拉延筋形状如图3所示(铅丝1.6mm圆形,材料板厚t=0.7mm)。按模具图示共测量15处铅丝数据,实际测得数据如表4所示。
拉延筋间隙调查
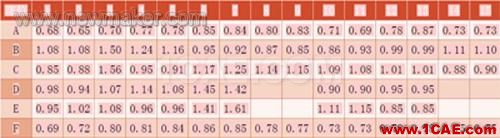
4.开裂破坏实验结果
所有平衡块抽出0.1mm垫片,无垫片就取消平衡块。观察开裂拉薄等处,有无接触较紧的部位。经过试验发现有2处压料较紧,已适当放松;并且实验中即便有拉裂或颈缩,板厚也没有再变薄。
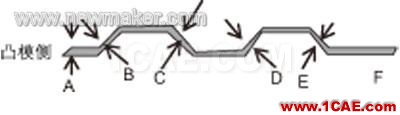
图3 测量部位及拉延筋形状
网格应变分析
在正常的模具状态下,我们采用网格应变分析方法对工件的成形过程进行模拟。一般钢板冲压成形中的3种变形方式:拉压变形、平面变形和双拉变形,分别对应3种应变状态:e2<0,e2=0,e2>0。
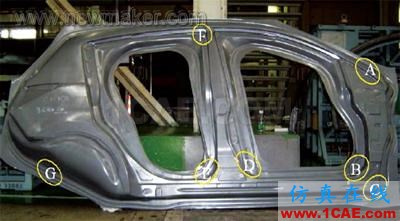
图4 危险区域分布
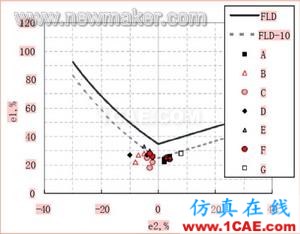
图5 正常状态,与FLC接近的点是破裂危险点
各部位所得数据
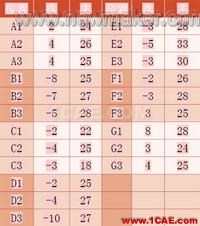
由以上调查测量结果分析得出E部位是成形破裂危险点,而且模具的成形分析也表明,门框下方是破裂危险点。
根据上述对模具的调查、网格分析及日产的CAE成形分析,技术人员提出了下一步的改进方案:准备将门框处的R角放大。首先,我们考虑了放大R角后对总装工程的影响,经过总装相关人员现场调查,发现放大此处R角到30mm左右,后续工程装配无影响。
根据预测板厚减薄率的经验公式,并通过实际测量得出的数据,计算板厚减薄率:
板厚残存率=58.356-0.180×RS-0.209×r1-0.136×θ1-0.525×L+0.197×H
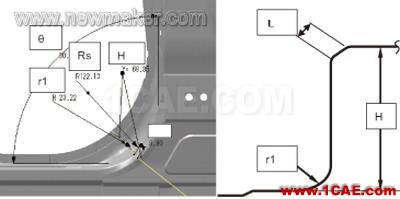
R角的验证
板厚减薄率=27.63%。
设想将r1=23mm放大至30mm,进行计算可得:
板厚减薄率=26.21%。
可以看出,减薄率有1.42%的改善,此法可以实施。
结语
通过调查拉延模平衡块接触、拉延筋间隙、不同闭合高度下材料的流动及网格应变分析,针对这个问题得出结论:扩大局部R圆角,成形后板厚增加,破裂的危险消除,从而解决了国产板料颈缩、拉裂的问题。 (end)
开放分享:优质有限元技术文章,助你自学成才
相关标签搜索:侧围板料开裂及对应模具分析 Autoform分析培训班 Autoform汽车模具仿真 Autoform视频教程 Autoform资料下载 在线软件培训 汽车钣金代做 Fluent、CFX流体分析 HFSS电磁分析 Ansys培训 Abaqus培训 有限元培训 Solidworks培训
编辑