冲压零件常见缺陷及措施
2017-04-11 by:CAE仿真在线 来源:互联网
1.废料、异物压痕
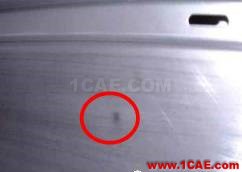
产生原因:
异物压痕是上下模掉入异物、灰尘产生凸凹。垫废料是由于生产过程中,未及时清理废料,导致将冲孔废料带到工作区所致。冲孔工序出现垫废料几率最高
引起因素:
(胚料污垢,胚料毛刺,拉延时发生渣滓,设备污垢,冲模污垢。板件碎末)
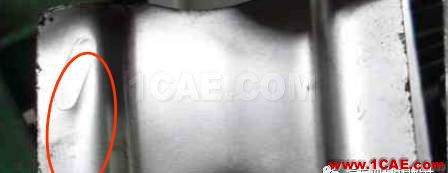
检查方法:主要以目视、油石、触感进行检查
判定 | 发现问题 | 处理意见 |
V1 | 目视明显 | 产品缺陷较大需要修正模具及工件 |
V2 | 目视轻微,触感明显 | 产品有缺陷需要修正模具及工件 |
V3 | 目视不可见,触感轻微 | 产品缺陷可不动,模具要修正 |
预防措施:
及时清理废料。
2.起皱
产生原因:
板材在成型过程中拉伸不足产生局部皱褶,主要原因是凸缘部分压边力太大,武大抵制过大的切向压应力而引起的切向变形,因而失去稳定后形成皱纹。
引起因素:
(气垫压力低、模具平衡块压力低、胚料涂油量多、破裂发生而导致流入现象、因异物混入而引起压住力弱)
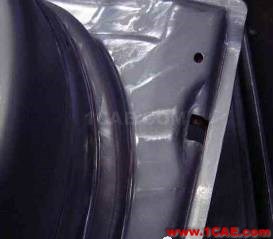
检查方法:基本以测量、目视、触感进行检查
判定 | 发现问题 | 处理意见 |
V1 | 目视明显范围大于100mm | 产品缺陷较大需要修正模具及工件 |
V2 | 目视较明显,有明显触感(外观面)目视明显,对后工程有明显影响(非外观面)经验值:0.5mm<=凹凸程度 | 产品有缺陷需要修正模具及工件 |
V3 | 目视轻微,有轻微触感;(外观面)目视较明显,但对后工程无明显影响(非外观面)经验值0.3mm<=凹凸程度<=0.5mm | 产品缺陷可不动,模具要修正 |
预防措施:
主要方法是加大压边圈的压边力和适当加大材料的尺寸,使其拉伸时始终处于稳定状态,即可减少皱纹的发生。
3.拉毛(拉延痕迹)
产生原因:
模具表面不光顺,造成板件有线状划痕。
引起因素:
凸凹模表面有尖利的压伤,凸凹模之间的间隙过小或间隙不均匀,凹模圆角表面粗糙,冲压时由于冲模工作表面或材料不清洁而进入杂物压伤表面,凸凹模硬度低时,表面附有金属废屑后,也会使拉伸后的工作表面产生拉痕。
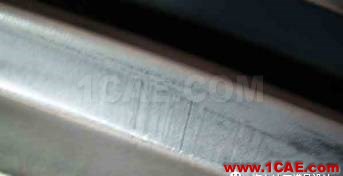
检查方法:基本以目视、触感进行检查
判定 | 发现问题 | 处理意见 |
V1 | 产品缺陷较大需要修正模具及工件 | |
V2 | 目视较明显,有明显刮手感,或伤到外表面棱线 | 产品有缺陷需要修正模具及工件 |
V3 | 无刮手感 | 产品缺陷可不动,模具要修正 |
预防措施:
将压伤表面进行修磨或抛光,将凸凹模间隙修整加大,将凹模圆角半径进行修磨和打光,保持凸凹模表面清洁,增加凸凹模表面硬度。
4.划伤
产生原因:
零件表面人为或异物划伤
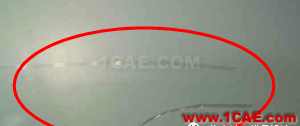
检查方法:基本以目视、触感进行检查
判定 | 发现问题 | 处理意见 |
V1 | 产品缺陷较大需要修正模具及工件 | |
V2 | 目视较明显,有明显刮手感,或伤到外表面棱线 | 产品有缺陷需要修正模具及工件 |
V3 | 无刮手感 | 产品缺陷可不动,模具要修正 |
预防措施:
平时生产中和使用中注意此问题,可以避免和解决。
5.多孔,少孔,孔变形,孔未冲透
孔变形产生原因:
凸凹模间隙大,凸凹模间隙偏。
孔未冲透产生原因:
模具行程不够,定位不当。
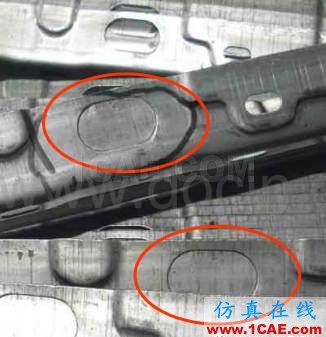
引起因素:
冲头多装或者少装,冲头折断,冲孔压料及冲头间隙不好,有带料现象。
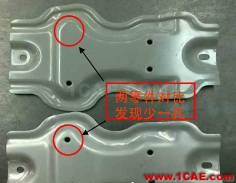
检查方法:基本以数孔,测量,目视、触感进行检查
判定 | 发现问题 | 处理意见 |
V1 | 多孔,少孔 | 产品缺陷较大需要修正模具及工件 |
V2 | 目视明显(经验值:变形程度大于0.3mm) | 产品有缺陷需要修正模具及工件 |
V3 | 目视轻微(经验值:0.1mm<=变形程度<=0.3mm) | 产品缺陷可不动,模具要修正 |
预防措施:
调整凸凹模间隙,勤刷油。调试时将滑块调到合适的高度,生产时严格按照操作规程操作
6.压痕
产生原因:
模具上下模研合局部接触过强产生压痕。
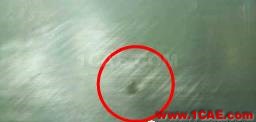
检查方法:基本以目视、触感进行检查
判定 | 发现问题 | 处理意见 |
V1 | 产品缺陷较大需要修正模具及工件 | |
V2 | 目视可见,触感明显 | 产品有缺陷需要修正模具及工件 |
V3 | 触感轻微 | 产品缺陷可不动,模具要修正 |
预防措施:
平时生产中和使用中注意此问题,可以避免和解决。
7.变薄(缩颈,拉薄),暗伤
产生原因:
板材在成型过程中应力过大产生局部厚度减少。
引起因素:
1.模具原因:凸凹模间隙太小:拉延筋布置不均匀:凹模口或拉延槽圆角太小:压边面不光洁。
2.设备原因:压边力过大或不均匀。
3.材料原因:质量不好,毛胚尺寸太大或不准确。
4操作:润滑不足或不当。
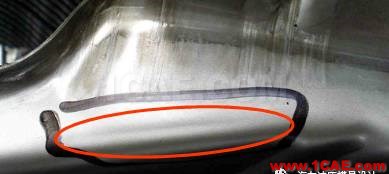
检查方法:基本以千分尺测量、目视、触感进行检查
判定 | 发现问题 | 处理意见 |
V1 | 无法钣金修理的缩颈 | 产品缺陷较大需要修正模具及工件 |
V2 | 零件正反面目视,触感明显,外板板厚残余小于60%,内板板厚残余小于70% | 产品有缺陷需要修正模具及工件 |
V3 | 零件正反面目视,触感轻微,外板板厚残余60%-75%,内板板厚残余70%-75% | 产品缺陷可不动,模具要修正 |
预防措施:
调节压边力,调整模具间隙,使之变大且要均匀,改变拉延筋的数量及位置,加大凹模及拉延筋圆角半径,提高压边面的表面质量,改善润滑条件,调整材料及毛胚形状及大小。
8.拉裂
产生原因:
板材在成型过程中应力过大产生破裂
引起因素:
气垫压力高,压边力过大或不均匀,调整垫压力高,涂油量少,毛刺大,拉延放料胚料错位,冲压R角小,激光焊接不良。
1.模具原因:凸凹模间隙太小:拉延筋布置不均匀:凹模口或拉延槽圆角太小:压边面不光洁。
2.设备原因:压边力过大或不均匀。
3.材料原因:质量不好,毛胚尺寸太大或不准确。
4操作:润滑不足或不当。
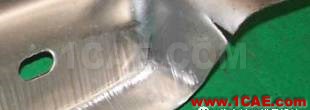
检查方法:基本以千分尺测量、目视、触感进行检查
判定 | 发现问题 | 处理意见 |
V1 | 开口超过2mm,裂纹长度大于50mm | 产品缺陷较大需要修正模具及工件 |
V2 | 开口不超过2mm,裂纹长度小于50mm | 产品有缺陷需要修正模具及工件 |
V3 | PB工序产生,后工程可切除部分裂纹 | 产品缺陷可不动,模具要修正 |
预防措施:
调节压边力,调整模具间隙,使之变大且要均匀,改变拉延筋的数量及位置,加大凹模及拉延筋圆角半径,提高压边面的表面质量,改善润滑条件,调整材料及毛胚形状及大小。
9.叠料
产生原因:
板材在成型过程中拉伸不足产生局部严重皱褶,板料重叠
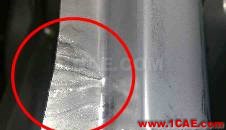
检查方法:基本以千分尺测量、目视、触感进行检查
判定 | 发现问题 | 处理意见 |
V1 | 出现板材破裂 | 产品缺陷较大需要修正模具及工件 |
V2 | 未出现板材破裂;但板材重叠严重 | 产品有缺陷需要修正模具及工件 |
V3 | 板材重叠轻微 | 产品缺陷可不动,模具要修正 |
预防措施:
平时生产中和使用中注意此问题。
10.毛刺
产生原因:
模具切刀间隙配合不好或切刀破损
引起因素:
凸凹模间隙过大,过小或者不均匀。冲模工作不分刃口变钝。凸模与凹模由于长期受振动冲击,轴线不重合,则易产生单边毛刺。

检查方法:基本以测量、目视、触感进行检查
判定 | 发现问题 | 处理意见 |
V1 | 产品缺陷较大需要修正模具及工件 | |
V2 | 管理部位毛刺高度大于0.15mm,一般部位:毛刺高度大于0.3mm | 产品有缺陷需要修正模具及工件 |
V3 | 一般部位:0.15mm<=毛刺高度<=0.3mm | 产品缺陷可不动,模具要修正 |
预防措施:
采用合理的凸凹模间隙,修磨凸凹模刃口
11.刻字、印记不清晰
产生原因:
到底标识不清晰
引起因素:
模具刻字、印记深度不足,装模高度不到位
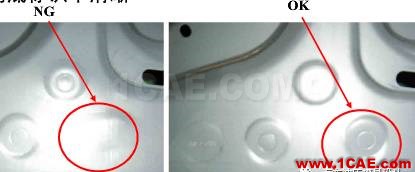
检查方法:基本以目视、触感进行检查
判定 | 发现问题 | 处理意见 |
V1 | 产品缺陷较大需要修正模具及工件 | |
V2 | 刻字、印记不全 | 产品有缺陷需要修正模具及工件 |
V3 | 刻字、印记不清晰 | 产品缺陷可不动,模具要修正 |
预防措施:
平时生产中和使用中注意此问题。
12.材料锌层脱落,表面粗糙
引起因素:上下模研合局部接触过强板材成型流动过程锌层脱落
检查方法:基本以目视、触感进行检查
判定 | 发现问题 | 处理意见 |
V1 | 外观面材料锌层大面积片状脱落 | 产品缺陷较大需要修正模具及工件 |
V2 | 外观面材料锌层脱落 | 产品有缺陷需要修正模具及工件 |
V3 | 三级面及非外观面外观面材料锌层片状脱落 | 产品缺陷可不动,模具要修正 |
预防措施:
平时生产中和使用中注意此问题。
冲压工序易产生的缺陷及处理方法
落料冲孔切边
1.毛刺过大(凸凹模间隙过大或者过小,刃口磨损,导向精度差,凸凹模位置不同心等)
2.变形(孔距太小,压料板与凹模型面配合不好,间隙过大等)
3.表面划伤(操作时有拖,拉等现象;板料在剪切过程中划伤等)
4.尺寸不符(上料不到位,定位装置损坏或松动,位置串动等)
5.少孔(冲头折断,长度不够等)
拉延
1.拉裂(凸凹模R角半径过小,压边力过大,材料成型性能差或材料尺寸偏大,凸凹模间隙小,润滑不当,定位不准,凸凹模R角或拉延筋不顺,拉毛等)
2.起皱(凸凹模R角半径过大,压边力过小,材料尺寸偏小;凸凹模间隙太大;润滑过甚;定位不准;拉延筋布置不良,高度不够等)
3.表面拉伤(模具工作表面有伤痕,材料表面有缺陷,润滑油中有杂质和废屑等)
4.波浪、鼓包、凹坑、麻点(压边力小,润滑不当,模具型腔脏,材料表面脏,透气孔堵塞,模具型面不平,润滑油脏等)
翻边
翻遍不垂直(凸凹模间隙过大)
翻边高度不一致(凸凹模间隙不均匀,定位不准,落料件尺寸不准)
翻边拉毛(刃口有伤痕,零件表面有杂质,刃口硬度太低)
翻边裂(修边时毛刺大,凸凹模间隙太小,翻边处形状有突变)
相关标签搜索:冲压零件常见缺陷及措施 Autoform分析培训班 Autoform汽车模具仿真 Autoform视频教程 Autoform资料下载 在线软件培训 汽车钣金代做 Fluent、CFX流体分析 HFSS电磁分析 Ansys培训 Abaqus培训 有限元培训 Solidworks培训