基于AutoForm的回弹补偿设置流程
2017-06-09 by:CAE仿真在线 来源:互联网
展望21世纪,随着汽车、航空航天工业的迅速兴起,大型制造企业市场竞争日趋激烈,对冲压件的快速设计和制造也提出了更高的要求。仅仅依靠工程设计人员的经验来制造冲压产品的方式显然已经不能满足现代企业的生产需求了。如何实现高质量、低成本、短周期的产品开发是赢得这场竞争的关键。冲压成形数值模拟技术是解决这一问题的主要手段,它将定性的经验转化为定量的模拟,基于冲压成形理论,把广泛应用的诀窍和经验融入到CAE数字化仿真中,方便地求解工艺及模具设计涉及的复杂板料成形问题,准确地预测冲压成形结果,很多制造企业已经将同步工程作为产品开发制造的重要环节。
目前世界各大汽车公司对板料冲压成形模拟的投入都相当重视,欧美、日本等发达国家在主要汽车覆盖件开发过程中全部都要经过仿真分析。在国内,北京航空航天大学、一汽集团、上海大众、上海宝钢和上海交大汽车工程研究所等单位,开展了汽车覆盖件冲压成形动态仿真的工业应用探索,先后完成了红旗轿车、Santana系列轿车等若干覆盖件的冲压仿真分析与试验分析,开展了汽车板成形性能等方面的研究。二汽、长安汽车公司都采用了计算机模拟仿真技术进行模具设计、优化冲压工艺、零件冲压成形性能等方面的研究工作。
常用板料成形模拟软件有:AutoForm、DynaForm、Dyna-3D、Marc、Pam-Stamp、Amsys、Abauqs、Robust、Mar等。其中AutoForm软件以计算速度快,容易操作等优点在汽车行业得到广泛的应用。国内大型汽车企业也相续引进AutoForm软件来优化工艺方案和进行复杂的模面设计。然而,有一个合适的软件是一回事,正确使用这个工具是另一回事,用户必须熟悉软件的功能原理才能有效地驾驭它。以AutoForm软件为平台的论著不胜枚举,但目前为止,尚没有一部完整地从基础到高级应用的书籍。绝大部分书籍都是侧重于软件的基础介绍或某些功能模块的论述操作,并未注重与冲压工艺本身的结合,仅能作为软件操作说明书使用。对汽车企业专业模具设计和工艺设计人员来说,这类著作不免有些欠缺专业理论的指导和可借鉴的优化经验。
因此,对专门从事冲压相关的工程人员来说急需一类专业的CAE分析指导书籍,《AutoForm原理技巧与战例实用手册》由一组长期从事汽车车身覆盖件的CAE分析的专业人员编写。由浅入深的介绍了AutoForm软件的基本操作及冲压成形模拟最新的方法原理;更重要的是,该书作者长期工作在汽车覆盖件制造第一线,具有丰富的实践经验,对冲压成形中的各个难点问题有独特的解决方法与经验。本书的阅读对象是可以是从事于冲压加工,模具设计的专业人员以及准备进入这个领域的初级学员,还可以作为高校研究板料冲压原理和工艺可制造型分析的老师和学生的指导书。
本书系统的阐述Autoform在冲压成形、液压成形、热成形等多个领域的应用范例;涵盖了从冲压件开发、成本计算、工艺开发、模具制造到零件生产的整个产品开发流程中各个重要专题;创造性地提出了基于AutoForm的板金件工艺设计与优化、料片展开及排样、回弹分析及型面补偿计算、零件稳健性分析与优化以及模具表面防护等诸多方面的实际应用方法、原理和技巧;涉及冲压成形中多个难点问题解决,如切边线精确展开、科学的模具成本计算和可靠的模具型面回弹补偿等。这些成果不仅反映了当前冲压成形数值模拟技术应用的最新研究进展。
本系列连载不能一一罗列该书中的所有内容,预定分3篇对《AuoForm原理技巧与战例实用手册》中涉及难点、热点及经验总结进行介绍。
首先对冲压成形中最普遍的读者最关心的的难点问题——回弹分析与补偿计进行阐述,该模块概述了回弹补偿基本原则和补偿策略、详细介绍了基于Autoform的回弹补偿设置流程。
其次,关于冲压模具工艺过程稳健性分析与应用,在有关AutoForm软件介绍的书籍中较少提及,本次连载后续也将对如何用AutoForm获取一个与实际生产波动相符的模拟结果,如何在产品和模具设计早期就关注冲压的稳健性问题进行专题介绍。
最后,如何以最经济的模具成本来满足不同的产量要求关系到企业的经济效益。《AutoForm原理技巧与战例分析实用手册》作为一本实用性的书籍,从工序的合理布置到模具成本计算做了全面的介绍,为冲压零件开发、科学地计算模具成本和有效降低模具成本提供帮助。
从本期开始,将逐一对以上三个读者普遍关心的模块进行详解。
回弹分析及补偿背景
回弹现象是汽车白车身冲压成形不可避免的问题。随着汽车工业的迅速发展,对冲压件的精度要求越来越高,特别是高强度钢、铝合金板材的大量使用,回弹问题显得更加突出,成为汽车工业领域的热点问题。通过对冲压成形数值模拟,可以在设计阶段发现并提出问题、了解回弹分布、获得回弹补偿,对减小回弹具有重要指导意义。
本文结合AutoForm软件介绍了回弹分析及补偿计算的流程、规律以及经验性东西。
1 成功回弹计算与补偿的5个原则
一个成功的回弹补偿很大程度上依赖于前期准备,要取得一个较小的回弹偏差值,需要输入精确的数据模型和工艺过程条件。结合AutoForm软件特点和实际的工程应用,总结出成功回弹计算与补偿的5个基本原则,以获得正确的回弹模拟结果,指导实际的生产。5个基本原则如下:
原则一:要保证合理的模具工艺规划和正确合理的模拟结果;
原则二:按照校核模拟设置(Final validation)要求设定参数;
原则三:合理的回弹评估;
原则四:保持工序过程的稳健性;
原则五:按照补偿策略进行补偿。
2 回弹补偿策略
根据工程应用经验,在这里一共总结出了三个回弹补偿策略,即补偿所有模具、仅补偿拉延模具和对各个模具进行不同的补偿。
这三个补偿策略均按照图1的全工序模拟过程进行介绍,OP20~OP50全工序模拟的模具模型按照零件模型(图1中绿色形状)进行制作。
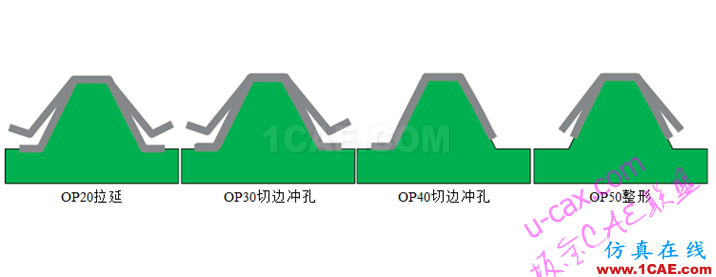
图1 全工序过程
2.1 补偿策略一:补偿所有模具
回弹补偿基于最后的工序,基于OP50的回弹结果对所有的模具进行同样的补偿。该补偿策略是大多数零件模具的补偿方式,到最后一序工作结束后,零件回弹到零件的形状。
2.2 补偿策略二:仅补偿拉延模具
回弹补偿基于最后的工序,基于即用OP50的回弹结果仅对OP20拉延的模具进行补偿,其他工序均不补偿。该补偿补偿策略是在OP20拉延回弹后和OP50整形回弹后相比较回弹量相接近,这样按照OP50之后的回弹补偿OP20的模具,OP20拉延完成经回弹就达到产品的形状。
2.3 补偿策略三:对各个模具进行不同的补偿
对各个模具进行不同的补偿是根据实际情况进行量身定做(Tailor-made)的补偿策略,即用基于OP50的回弹结果并考虑定位附加变形对OP20拉延的模具进行补偿,但其他工序按照后工序外形定位补偿原则。
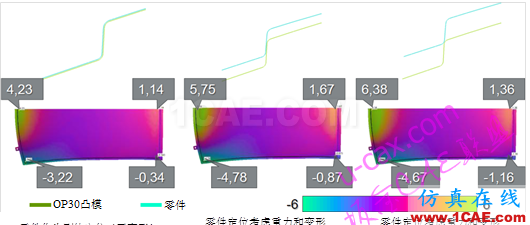
图2 零件在不同定位状态下的干涉与回弹情况
1)拉延模缩放
当零件完成OP20拉延向后续定位时,如果按照实际考虑零件的传送、重力和变形时,零件会和后续的下模干涉,这样当压料板和下模闭合时,零件会产生附加变形,如图2所示,这样会影响回弹分析结果。图3显示的是零件在不同定位状态下的干涉与回弹情况。这两张图表明,零件如果在传送和重力的作用下发生变形,这样使零件在定位时产生影响,零件会产生附加变形,回弹量也加大。
这样必须考虑办法减小或消除这种对回弹不利的因素,这里采用的办法是将OP20的拉延模型放大,如图3所示,从图中可以发现零件和OP30的下模干涉消除,零件的回弹显著减小。
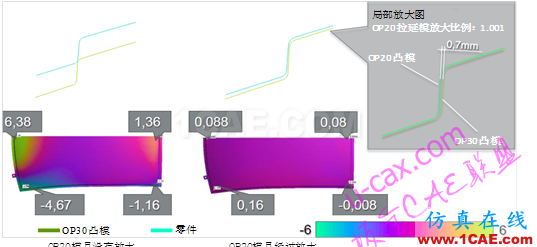
图3 OP20拉延模放大
2)后工序外形定位补偿
后工序外形定位补偿是指在OP20拉延工序完成后发生回弹,如果后工序(大多数情况是指切边工序)的型面还是按照零件模型设计,这样零件就会和后工序的模具形状不符合,如果OP20拉延工序发生严重的回弹,零件放置在后续工序上经过压料板闭合后会发生严重的附加变形。这样就需要对后工序的模具型面按照OP20回弹的型面进行补偿,即正补偿。
因此后工序外形定位补偿的目的是避免零件在后工序压料板闭合时产生附加变形,主要应用在拉延后产生回弹较大的情况。
后工序外形定位补偿实现方法:第一步是拉延模拟后计算回弹结果;第二步后工序应用AutoForm的回弹补偿模块以拉延模做参考模具进行补偿因子为-1的补偿。
3 获得准确回弹补偿的步骤
进行准确回弹补偿的流程图,如图4所示,包括9大步或15小步。本节将分两个方面,即精确的回弹模拟和有效的回弹补偿分别进行介绍。
3.1 精确回弹模拟
精确回弹模拟包括第一步至第五步,即:
第一步:获取正确合理的成形模拟结果。满足原则一的要求,使用AutoForm进行一个成形工序的开发与优化,进行工序构思和拉延模型制作,并考虑优化所有工艺参数和测量检具的夹持条件。在进行回弹之前,零件必须是能满足最终质量要求:无开裂/无起皱/最终料片形状,所有工序条件(拉延筋位置/切边操作/斜楔操作)能够在现实中实现。模拟步骤:
1)模型/工具定义。检查模具网格在90度的R角上保证至少有8个单元。
2)料片定义。设置料片形状、材料数据和轧制方向,并检查材料性能参数等。 3)工序过程定义。设置拉延筋和工序过程,检查切边线、冲孔和方向的设置是否合理,压边力是否合理,切边/冲孔顺序是否合理(考虑应力释放顺序) ,进行运动干涉检查(kinematical check)和模具穿透检查(检查模具间隙),检查行程设置是否合理。
4)模拟结果评估。模拟结果的评价包括成形性(Formability)开裂分析、厚度分布、起皱检查(目测)、棱线滑移线和凹模入口R角冲击线、压边圈闭合情况、材料流入量(Draw-in)、压边圈压力分布以及模拟收敛性检查(拉延、成形与翻边工序应小于40个迭代步)等。
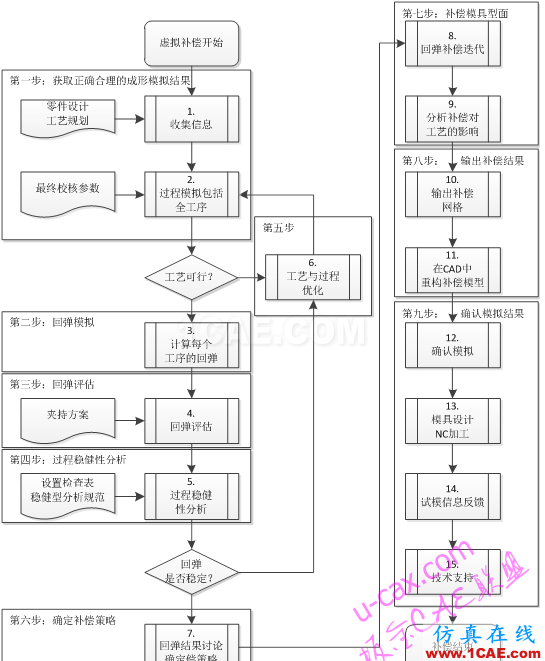
图4 进行准确回弹补偿的流程图
第二步:回弹模拟。按照原则二进行回弹模拟的控制参数设置,需检查回弹计算的收敛行为(Convergence behavior)。一般不用自由约束回弹,应采用约束条件下进行回弹计算,约束应尽可能的少并和实际相一致;定义参考模型和夹持方案(注意夹持面的选取:上表面/中层面/下表面,夹持点定义采用映射原始点) 。
第三步:回弹评估。对夹持方案进行分析评估,确认其是否合理,查夹头和导向销的夹持力和作用力(应小于30牛),以确认是否存在附加变形和位置偏移。确认参考面的位置是否正确,回弹结果距离正确的判断和分析(节点到参考面的法向)。
第四步:过程稳健性分析。定义工序环境(输入变量) à根据不同的输入变量的变动计算出多个模拟结果à评估分析工序过程的影响和敏感性。注意:工序稳健性主要考虑成形性和回弹是否稳定。
第五步: 工序与过程优化。如果全工序模拟过程中,零件的成形性存在问题,如开裂、起皱等,或者回弹不稳定,这就需要进行工序优化或过程参数优化,如修改工序参数的设置、模具造型或零件造型等。
3.2 有效的回弹补偿
有效的回弹补偿包括第六步至第九步,即:
第六步:确定补偿策略。讨论分析各个工序的回弹特点,按照原则五和第2节定义的回弹补偿策略对各个工序模具进行补偿。
第七步:补偿模具型面。按照确定的模具补偿策略和拉延模具的补偿原则进行指定的曲面迭代回弹与补偿计算,当回弹结果达到预定的误差精度要求时,结束迭代计算。
在AutoForm中,回弹计算结束经过第一次补偿在计算回弹后,可以通过Activator进入下一次迭代补偿,注意补偿曲面的拔模负角。
第八步:输出补偿结果。输出补偿的网格,然后将网格输入CAD软件系统进行曲面重构,尽可能保证重构的曲面与补偿网格一致。
第九步:再次计算确认模拟结果。在进行加工之前,对基于补偿的重构CAD模型再次进行模拟计算验证。验证合格后,提交给模具设计和NC编程进行模具的制造。到试模时,进一步的跟踪和验证,检查试模条件和模拟条件的一致性,必要时再做调整。然后总结经验,更新模具补偿策略,为后续的模具回弹补偿提供经验支持。至此整个回弹补偿的工作结束。
4 结束语
本文基于AutoForm的回弹分析及补偿计算的操作,结合实际生产中的经验,总结了回弹分析及补偿计算的5个原则,这是获得可信回弹及补偿结果的基本条件。在此基础上本文介绍了回弹补偿的策略和获得准确回弹补偿的具体步骤,对实际模具制造和零件生产具有指导意义。
参考文献
[1] 涂小文,徐海梅,肖利勇等. AutoForm原理技巧与战例实用手册[M].武汉:湖北科技出版社,2013
[2] AutoForm Engineering GMBH, AutoForm Plus R3.1 User Help Document
[3] AutoForm Engineering GMBH,AutoForm Plus R1技术讲座,中国, 2009.
[4] AutoForm Engineering GMBH,AutoForm Springback Workshop, China, 2010.
[5] AutoForm Engineering GMBH,AutoForm Processing HSS & AL Seminar, China, 2011.
相关标签搜索:基于AutoForm的回弹补偿设置流程 Autoform分析培训班 Autoform汽车模具仿真 Autoform视频教程 Autoform资料下载 在线软件培训 汽车钣金代做 Fluent、CFX流体分析 HFSS电磁分析 Ansys培训 Abaqus培训 有限元培训 Solidworks培训