【干货】应对汽车翼子板拉深起皱开裂的技术总结【转发】
2017-07-23 by:CAE仿真在线 来源:互联网
翼子板是整车车身的关键零件,翼子板与侧围、发动机盖以及前保险杠等外观零件搭接配合,对外观、尺寸精度要求高。
对于传统拉深工艺,由于翼子板前保险杠处拉深台阶深度深,容易造成台阶处减薄率增大,导致后期整形时制件开裂风险增大,容易造成表面质量缺陷,影响制件的外观。
对于翼子板前保险杠处,为了减少整形量,传统拉深造型一般选在贴近制件法兰面。在成形翼子板前保险杠处时需保证制件在拉深和整形过程中不开裂以及后期整形时不会因为侧壁拔模角θ大而产生整形多料(拉深造型弧长大于制件弧长,导致整形后有部分板料叠加),如图1所示。
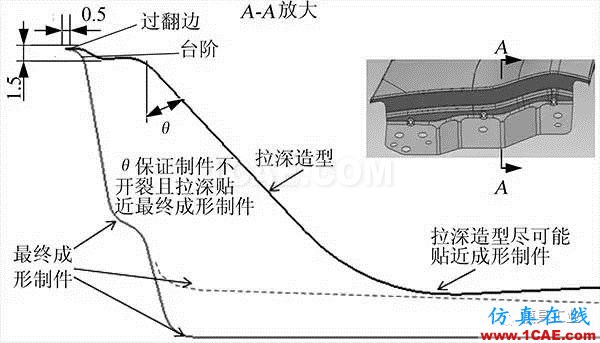
图1 传统翼子板前保险杠处拉深成形工艺
传统方案的问题分析及解决办法针对传统翼子板前保险杠处拉深起皱开裂问题,其开裂和起皱原因如下。
(1)开裂原因:①前翼子板保险杠处台阶高度约为25 mm,拉深时台阶处减薄率处于临界点,导致整形时台阶开裂;②为避免制件整形时积料起皱,拉深造型侧壁角度θ取较小值,使得拉深时侧壁减薄率增大,制件整形时侧壁开裂。
(2)起皱原因:①刀块与板料最先接触位置远离整形分模线,导致中间板料处于自由状态,难以控制,发生起皱;②为避免整形开裂,增大拉深造型侧壁拔模角θ,使得单位截面上拉深造型长度大于制件长度,整形时板料无处可走,形成叠料和起皱。
综上所述,针对制件的开裂现象采取减小拉深减薄率的方法,采取在A 面外侧增加一个浅台阶的方案。针对制件起皱,采用整形刀块从根部接触板料且外加压料板整形,整形后再修边的方案。拉深成形及后序断面如图2所示。
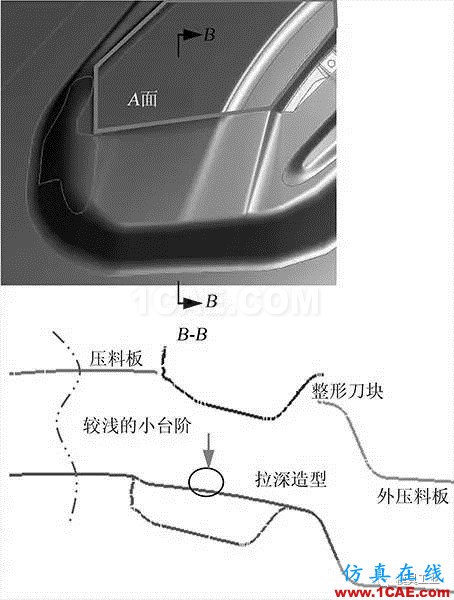
图2 更改后的翼子板前保险杠处拉深成形工艺
图3 所示为某品牌车型的翼子板,其前保险杠处A 面起伏较大,采用传统工艺拉深成形时制件起皱、开裂严重,针对这一问题进行翼子板新拉深成形工艺方案研究。
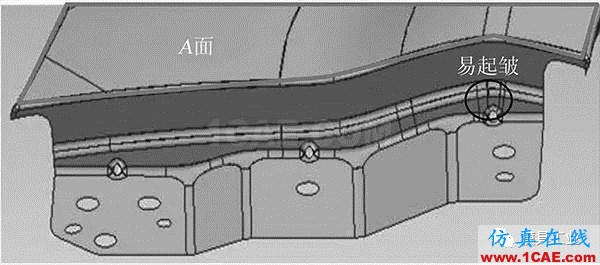
图3 翼子板前保险杠制件结构
2种方案成形工艺分析
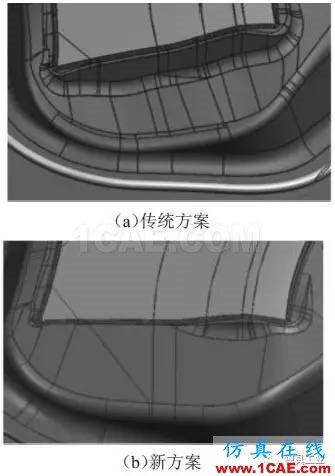
图4 翼子板前保险杠处拉深成形方案对比
图4 所示为翼子板的2 种拉深工艺方案。传统方案:拉深造型台阶深度深,使其更接近制件,但拉深减薄率大;新方案:沿着A面下面设置小台阶,减小拉深减薄率。
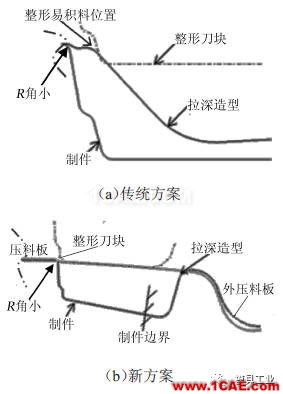
图5 整形刀块与板料接触顺序
制件拉深后整形时整形刀块的接触顺序如图5所示,从图5(a)可以看出,传统方案整形刀块先接触拉深侧壁,即法兰部位已贴近制件,但刀块与制件侧壁接触时,过翻边和1.5 mm台阶处多出的材料聚集到侧壁,增大起皱风险;且因拉深造型深度深,制件R角较小,拉深时减薄率大,整形时拉深成形后的制件强度不足,开裂风险也大幅度增加。图5(b)新方案中拉深工艺取消工艺台阶,整形积料明显减少,整形刀块在制件R角根部接触,减轻A面R角变形风险;同时由于外侧压料板的存在,板料的进料速度得到有效控制,起皱风险降低;且拉深造型较浅,拉深后前保险杠处减薄率小,能够保证制件的强度,有效避免整形时制件开裂现象。
2种方案CAE成形过程及结果对比
针对上述理论分析结果,利用AutoForm R3.1分析软件对上述2 种拉深工艺进行CAE分析验证,分析结果如下。
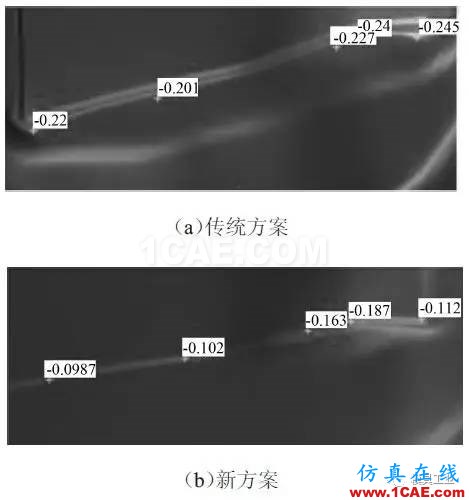
图6 拉深减薄率CAE分析对比
(1)制件拉深减薄率CAE 分析对比如图6 所示。从图6(a)可以看出,传统方案在拉深结束时制件最大减薄率已经达到0.245,超过翼子板B180H1材质的极限减薄率0.22,整形时极易发生开裂。如图6(b)所示,新方案拉深结束时制件最大减薄率为0.187,小于B180H1 材质极限减薄率0.22,整形时无开裂风险。
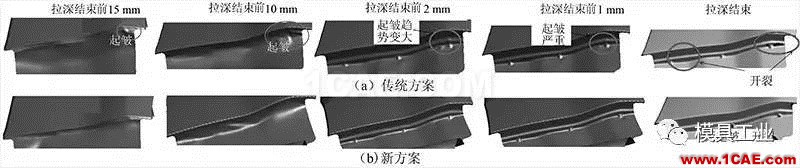
图7 拉深起皱CAE分析对比
(2)制件拉深CAE起皱分析结果对比如图7 所示。从图7(a)可知传统方案中,拉深结束前15 mm就存在起皱现象,起皱主要存在于制件的圆角半径较小处,并且越接近拉深结束时起皱现象越明显,起皱现象的存在有可能引起开裂风险。新方案改进后制件的起皱现象得到明显改善,直至拉深结束,制件均不存在起皱现象,制件的拉深成形质量提高,如图7(b)所示。
新成形工艺生产验证
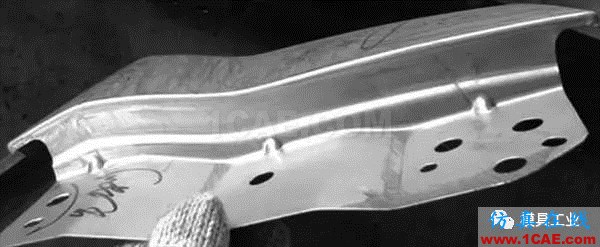
图8 现场制件状态
根据前期理论分析和CAE验证,对翼子板进行生产验证。如图8 所示为最终成形的翼子板,通过外观灯光和油石检查,制件成形质量良好,无起皱开裂现象,制件与前保险杠的调试时间缩短,提高了企业的生产效率。
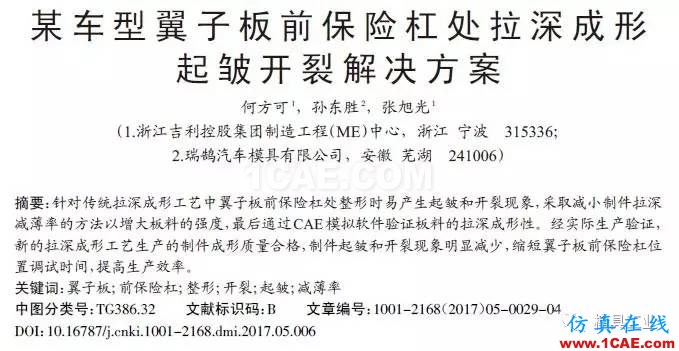
来源:模具工业
版权归原作者,如有标错,联系我们改正
相关标签搜索:【干货】应对汽车翼子板拉深起皱开裂的技术总结【转发】 Autoform分析培训班 Autoform汽车模具仿真 Autoform视频教程 Autoform资料下载 在线软件培训 汽车钣金代做 Fluent、CFX流体分析 HFSS电磁分析 Ansys培训 Abaqus培训 有限元培训 Solidworks培训