如何才能快速设计出一款低成本、高性能的离心泵产品?
2016-09-14 by:CAE仿真在线 来源:互联网
如何才能快速设计出一款低成本、高性能的离心泵产品?
为了提高工作效率,现在很多研发人员都在采用仿真联合实验的手段,但是由于设计和仿真不能同步进行,初步设计的产品如果通过仿真得到的性能曲线不能满足使用要求,往往需要返回到CAD模型中修改几何参数,再仿真计算获得结果,整个过程繁冗复杂,那么,怎么才能使整体研发流程最简化、研发成本和周期最小化呢?
有人想到了在CAD技术和仿真模拟技术的基础上,引入软件驱动和优化算法,重复驱动CAD软件和CAE软件自动修改模型和仿真计算,从而极大地减少工程师重复性的工作量,进而减少重复工作过程中出错的可能性。但由于存在与参数化建模软件、叶轮机械设计软件、数值分析软件集成的二次开发等门槛,一直举步维艰。
前不久,海基的几位工程师提出了一个方案,基于叶轮机械设计-仿真-优化的一体化思路,通过集成叶轮机械的参数化设计、数值分析和优化设计软件,并自定义开发各软件之间的接口和操作流程的批处理化,在同一平台上可自动实现包括参数化设计、数值分析和优化设计的所有功能,听起来神乎其神,那这个方案是否真的能帮助我们快速完成产品设计吗?
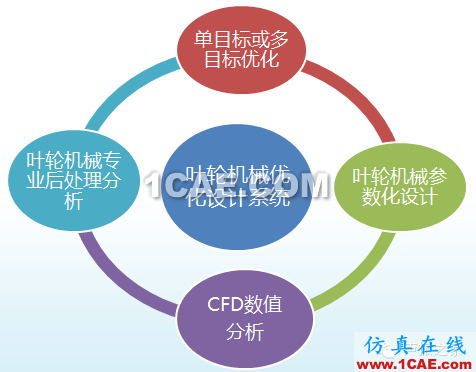
图1 叶轮机械优化设计系统架构
以离心泵的设计为例,理论上来说,采用该一体化设计平台,可通过采用CFturbo设计出较理想的初步设计模型,并自动输出至PumpLinx进行性能分析,获得数值计算结果,自动输出至优化设计软件Isight。通过在Isight中设置优化参数和提取数值计算结果,Isight会有针对性地对计算结果进行改型优化,自动调用CFturbo和PumpLinx进行“设计-仿真-优化”的多次循环,以最少的设计次数获得最佳的设计模型,最终获得符合要求的产品。
我们实际来做一个案例,假设离心泵设计点工况为:
• 流量:200m³/h;
• 扬程:≥45m;
• 额定效率:≥84%;
• 转速:2500RPM;
• 介质:20℃清水。
1、叶轮设计
在输入设计参数之后,根据CFturbo内置的经验函数可以自动计算出叶轮几何特性参数。本设计中,先根据所需设计的泵基本性能参数,根据CFturbo内置的经验函数得到泵的详细几何参数和相应的流体域模型,完成离心泵叶轮的三维初步设计,如下图所示:
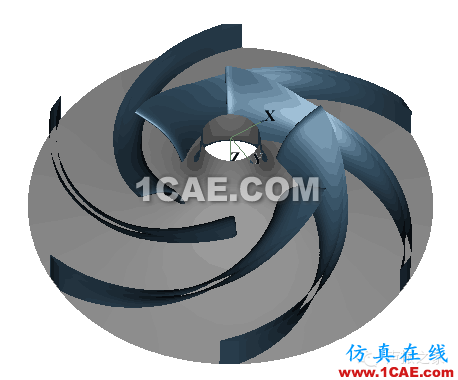
图2 叶轮设计模型
2 、蜗壳设计
CFturbo具有蜗壳设计模块,将已创建的叶轮模型导入之后,即可便捷地展开蜗壳的设计工作。最终生成的蜗壳模型如下:
图3蜗壳设计模型
3 、离心泵工作性能的数值仿真
叶轮和蜗壳模型生成完毕后,在CFturbo中直接启动PumpLinx可对设计模型和优化后的模型展开CFD分析,预测离心泵的流体动力特性。
对单个工况进行稳态仿真,迭代500次达到稳定,所需时间为20分钟。通过仿真,获得了离心泵初始模型的性能曲线,如下图所示。从图中可以看出,初始设计模型在设计点的扬程为45.02m,效率为83.65%,扬程达到了设计要求,但效率偏低,需要在原设计基础上对模型进行优化。
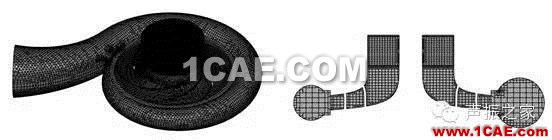
图4直流泵叶轮蜗壳网格图
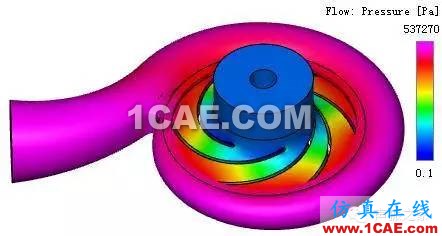
图5 设计流量工况下压力分布结果

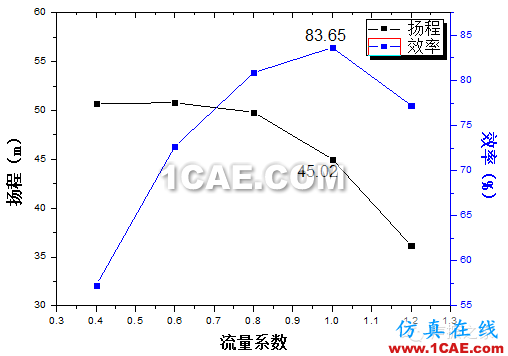
图6 计算所得泵的性能曲线
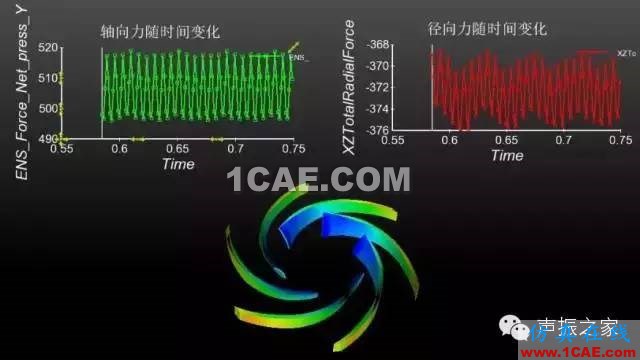
图7 多目标的后处理结果分析1
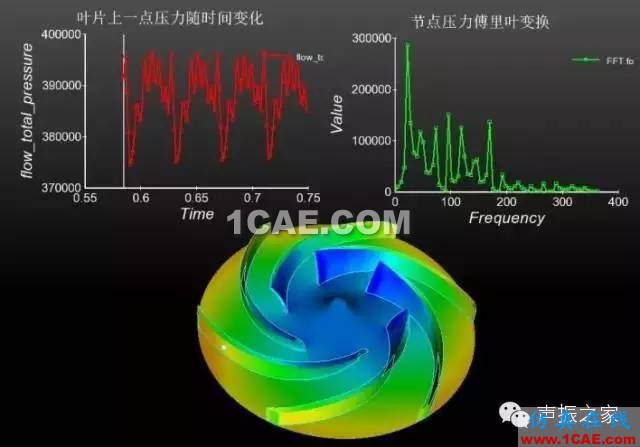
图8 多目标的后处理结果分析2
4、离心泵性能优化
(1)离心泵优化参数
为了提高离心泵效率,在叶轮设计参数中选取了10个可变参数作为优化变量,如下表所示:
表2 离心泵优化变量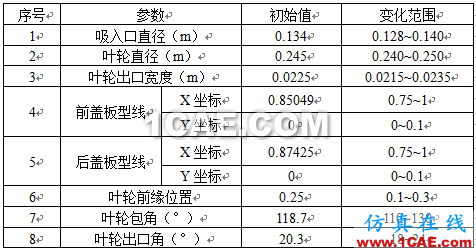
各变量含义示意图如下所示。
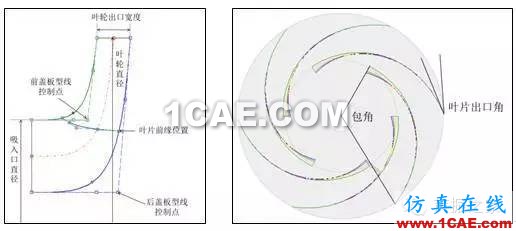
图9 变量示意图
(2)离心泵优化流程 优化过程需要不断进行“设计—评估—改进”的多次循环,通过一种搭积木的方式快速继承和耦合设计和仿真软件,将所有设计流程组织到一个统一的逻辑框架中,自动运行仿真软件,并自动重启设计流程,从而消除传统设计流程中的重复性工作,使整个设计流程实现全数字化和全自动化。本次优化设计流程如下图所示。
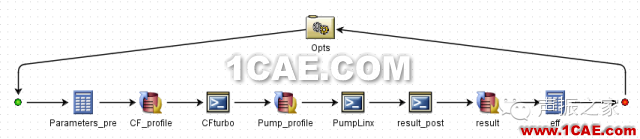
图10 优化流程图
本优化流程集成了优化算法、CFturbo设计软件、PumpLinx仿真软件、文档修改、计算器和一个自编后处理程序。
本案例是在离心泵优化设计平台上施加遗传算法全局搜索和二次序列规划方法局部寻优的优化策略组合,启动优化平台进行优化求解,最终获得优化后的设计模型。
(3)离心泵优化结果
优化目标:提高额定工况下离心泵效率,并保证扬程的设计要求;
约束:扬程≥45m。
下图显示了优化软件在计算迭代过程中离心泵效率的变化曲线。经过323次迭代优化计算后,寻找到目标函数的全局最优解,优化过程结束,最终得到的离心泵最优效率为85.21%。
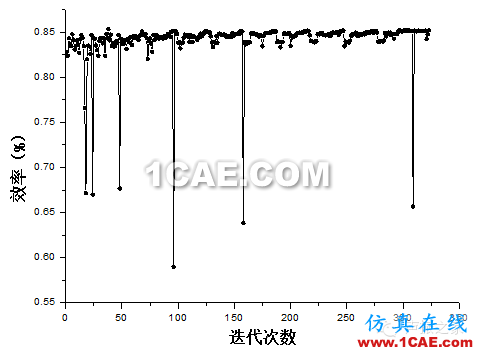
图11 优化过程曲线图
下图为计算得到的原始泵模型和优化泵模型的性能曲线的比较,其中黑色曲线为原始泵模型,红色曲线为优化后泵模型的性能曲线。从图中可以看出,优化后泵模型的扬程和效率都得到了一定的提升,流量系数在0.4到1.2范围内,扬程增大3-5m,效率提高1.56%-6.05%。外特性曲线表明,经优化后离心泵的水力性能得到明显改善。
图12 优化前后离心泵性能对比图
优化前后结构各参数值见下表,从表中可以看出,离心泵结构变化较大,其中吸入口直径、前后盖板型线、包角和出口角有了明显的改变,而叶轮直径和出口宽度变化较小。
表3 离心泵优化变量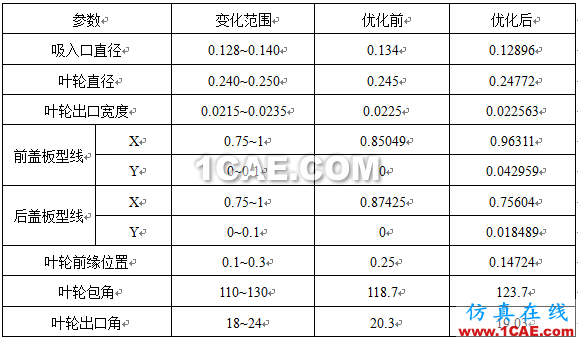
下图显示了原始模型和优化后模型子午面对比情况,从对比图可看出,叶轮前缘位置更靠近进口,叶轮对水做功较早。前后盖板型线改动也较大,前后型线在中间位置靠拢,在流动中间形成了较窄的空间。
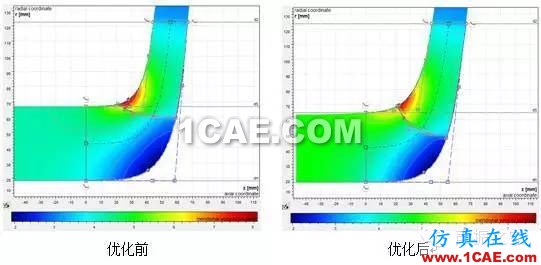
图13 优化前后子午面对比
通过验证,这套方案确实实现了意义上的“设计-仿真-优化”的一体化,可以帮助工程师更高效便捷地进行产品研发设计。
相关标签搜索:如何才能快速设计出一款低成本、高性能的离心泵产品? Pumplinx流体分析培训课程 Pumplinx旋转机构仿真分析 Pumplinx培训 Pumplinx学习教程 Pumplinx视频教程 Pumplinx软件下载 pumplinx流体分析 Pumplinx代做 Pumplinx基础知识 Fluent、CFX流体分析 HFSS电磁分析 Ansys培训