基于Hypermesh/Fe-safe的同步环组件疲劳寿命分析
2017-07-05 by:CAE仿真在线 来源:互联网
变速器同步环组件是锁环式同步器系统的重要组成部分,锁环式同步器系统的一种主要失效模式为同步环外环的断裂,而引起同步环外环断裂的主要原因是齿套偏摆导致同步环外环局部受力过大。针对此问题,采用Hypermesh隐式分析来计算同步过程中齿套偏摆对外环的挤压应力,并采用Fe-safe软件以强度分析结果为输入,进行同步环外环疲劳寿命分析。通过此分析,在同步器设计初期进行同步环外环疲劳寿命计算,根据计算结果进行结构优化,以满足疲劳寿命设计要求。
疲劳破坏是工程结构和机械失效的主要原因之一,引起疲劳失效的循环载荷的峰值往往远小于根据静态断裂分析估算出来的“安全”载荷[1]。因此开展同步环组件疲劳寿命研究对变速器同步器设计有着重要的工程意义。
1 简介
目前广泛采用的同步器是惯性式同步器,它有锁环式和锁销式等形式。轿车变速器由于转动惯量小,主要以锁环式同步器为主[2]。锁环式同步器主要通过同步环锥面碳层的摩擦来实现转速的同步,使整个换挡过程平顺完成。
理想状态下,同步器在同步过程中同步环组件不会发生疲劳破坏。然而实际工况下,拨叉在拨环过程中,可能出现三个叉脚只有一个受力的情况,从而导致齿套偏摆,引起同步环外环局部受力过大,进而引起疲劳破坏。齿套偏摆状况如图1所示。
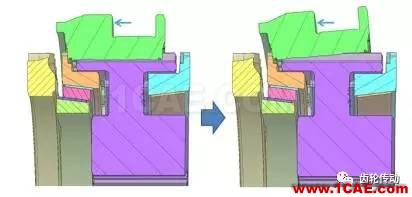
图1 齿套偏摆示意图
本文以某变速器双锥同步环为例,基于Hypermesh/Fe-safe软件进行齿套偏摆时同步环疲劳寿命分析,通过此分析,为同步器前期结构设计提供指导,确保其满足设计要求。
2 强度分析
2.1 分析模型
在进行CAE分析过程中,前处理花费的时间占整个分析的60%以上,因此想要提高工程师的工作效率则必须选择有效的、便捷的前处理软件[3]。前处理过程主要包括:几何处理、网格划分、约束载荷施加及输出参数设置。本文中的分析过程采用Pro/e软件进行几何建模,将Pro/e生成的.stp格式几何模型导入Hypermesh软件进行前处理。
为了节省分析资源的同时获得较准确的分析结果,同步环组件采用二阶四面体(C3D10I)及一阶六面体(C3D8I)混合建模,为了保证计算精度和计算效率,根据以往经验对应力不集中的地方采用较为稀疏的网格进行划分,对应力集中位置采用较细密的网格进行划分,对某些小倒角、小孔进行简化处理,避免产生过小尺寸的网格单元。图2所示为同步器系统的有限元分析模型。
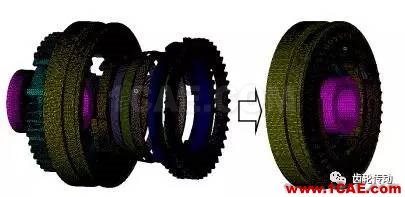
图2 有限元分析模型
2.2 材料参数
在Hypermesh软件中定义材料参数、建立结构属性和赋予结构属性,同步器系统各零部件的材料参数如下表1所示。
表1 零部件材料表
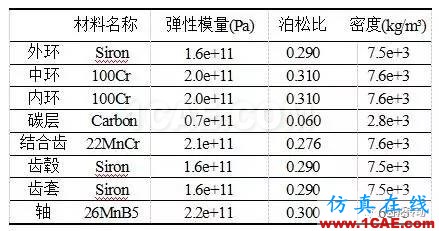
2.3 边界条件与载荷
为实现齿套偏摆分析计算过程,本文采用在齿套上施加1000N换挡力的同时对齿套施加强制转角的方式进行加载。由于外环结构为周向不对称结构,换挡力的位置会影响外环应力分布。为计算外环的最大应力值及最小应力值进而分析外环的疲劳寿命,本文在齿套周向上每间隔24°角位置处设置加载点,每次在一个加载位置处施加F=1000N的换挡力,并对齿套施加一定强制转角,进行应力计算,共计进行15次计算。换挡力分布如图3所示。
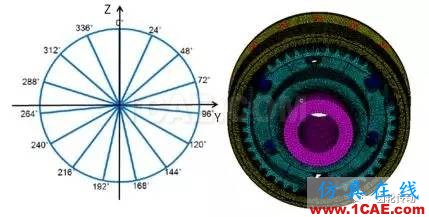
图3 拨环力分布图
变速器齿套最大偏摆角度为1°,分析过程中齿套施加绕Y轴和Z轴的强制转角Yα和Zα,计算方法如下:
绕Y轴强制转角Yα= Ycos(α)+Z sin(α)
绕Z轴强制转角Zα= -Ysin(α)+Zcos(α)
其中:Y= 1°= 0.0174532925 rad
Z= 0°= 0.0 radα=0°、 24°、48°、……、336°
齿套施加绕Y轴和Z轴的强制转角Yα和Zα的计算结果如表2所示。
表2 齿套强制转角列表
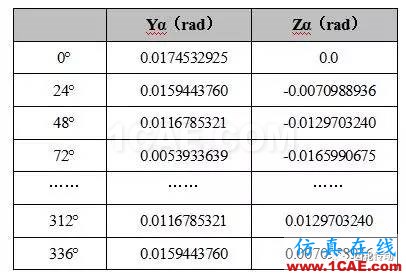
本文仿真分析加载过程共分为两步,第一步在换挡力F作用下齿套和外环压紧,第二步保持换挡力F不变,给齿套施加相应强制转角。加载方式如图4、图5所示。
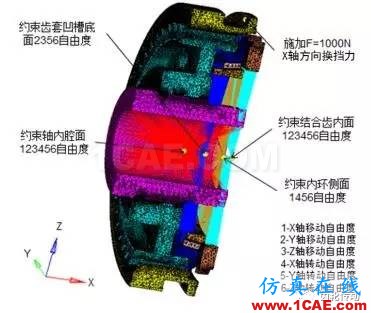
图4 边界条件及载荷(step1)
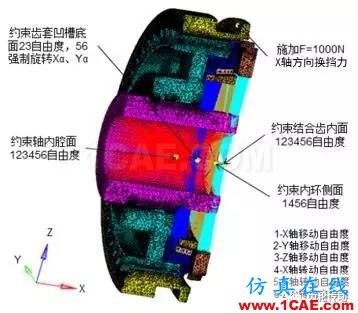
图5 边界条件及载荷(step2)
2.5 分析结果
将建立的有限元计算模型导入ABAQUS软件中进行强度计算,获得同步环外环在齿套偏摆情况下的强度结果,如图6所示。
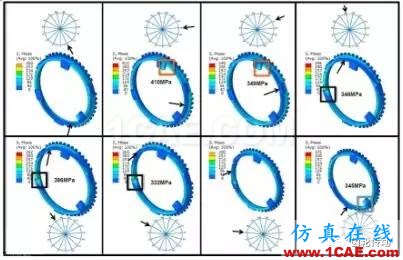
图6 外环应力分布云图
从图6中可知,外环最大应力发生在换挡力施加在264°位置处,值为410MPa;外环最小应力发生在换挡力施加在96°位置处,值为185MPa。
3 疲劳分析
3.1 材料疲劳参数
材料的疲劳参数对同步器外环疲劳寿命的影响极大,外环材料疲劳参数如表3所示。
表3 外环材料疲劳参数表
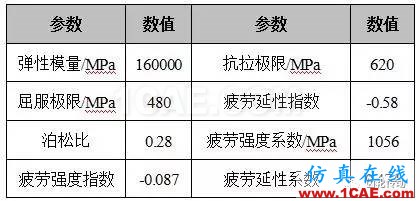
3.2 疲劳循环周期
同步器台架试验中,换挡过程外环平均转速为1100rpm,平均换挡时间0.361s,因此整个换挡过程中,同步器外环旋转6圈,承受6次交变载荷。同步器外环所在档位换挡次数设计要求为65000次,疲劳循环周期如图7所示。
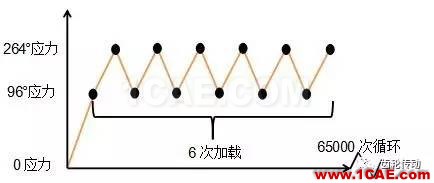
图7 疲劳循环周期图
3.3 疲劳寿命分析
将外环强度分析结果,材料疲劳参数及疲劳循环周期输入Fe-safe软件中,采用最大主应力法作为应力判断标准, Smith-Watson-Topper(SWT)作为平均应力修正方法,进行疲劳寿命计算。
3.4 分析结果疲劳分析结果如图8所示,由图可知,LOGLife小于零主要集中在卡爪根部(LOGLife<0不满足设计要求),最容易发生疲劳破坏处LOGLife值为-1.1,循环次数N=10-1.1×65000=5163次。
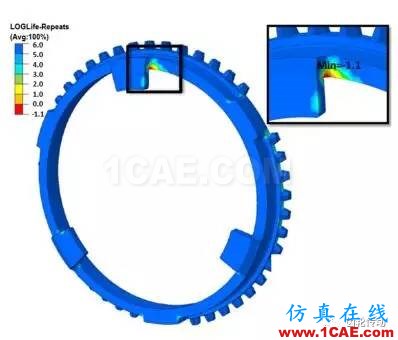
图8 外环疲劳寿命云图
经过疲劳耐久台架试验后,同步器外环出现断裂,其断裂情况如图9所示,断裂位置与仿真结果吻合。
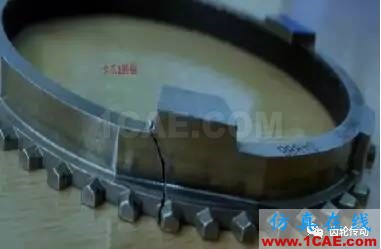
图9 外环疲劳断裂图
(1)本文以某变速器同步器系统为研究对象,基于有限元软件Hypermesh/Fe-safe,建立了分析齿套偏摆对同步环外环疲劳寿命影响的仿真分析模型;
(2)采用周向加载及强制转角方式,通过强度分析计算,获得了外环最大应力及最小应力分布位置及数值;
(3)结合具体试验工况进行疲劳分析计算,获得外环疲劳断裂位置及疲劳循环次数;
(4)通过试验与仿真分析结果对比,显示断裂位置与分析结果吻合。本文仿真分析方法可在同步器设计初期进行疲劳耐久预测,从而缩短研发周期,降低研发成本。
相关标签搜索:基于Hypermesh/Fe-safe的同步环组件疲劳寿命分析 fe-Safe培训 fe-Safe培训课程 fe-Safe软件培训 fe-Safe在线视频教程 fe-Safe教程 fe-Safe疲劳分析 Fluent、CFX流体分析 HFSS电磁分析 Ansys培训 Abaqus培训 Autoform培训 有限元培训