【作品展示7】车身关键零部件材料板厚优化匹配问题研究【转】
2016-11-09 by:CAE仿真在线 来源:互联网
作者介绍INTRODUTION
Vince
湖南长沙人,研究领域:车身结构可靠性/稳健性优化设计、车身结构“材料-工艺-性能”全耦合稳健优化设计、汽车车身结构多学科与轻量化设计、车身结构耦合工艺过程的一体化设计。
擅长Hyperworks、Ls-dyna、ABAQUS、Nastran,iSIGHT、modelFRONTIER、MATLAB等软件。在项目中,主要负责FEA模型的建立与试验验证、相关代理模型的构建与精度分析、优化算法的开发及实施等工作。
作者联系方式:
邮箱:zhang_tiger@foxmail.com
QQ: 1076346363
作品展示PRENTATION
安全、节能和环保是目前汽车工业发展面临的三大主题,而这些问题都与汽车轻量化密切相关。大量研究表明,汽车每减重10%,其油耗将减少6~8%,排放量降低5~6%。但是汽车在轻量化的同时,对汽车安全性也提出了更严峻的挑战。为了达到汽车轻量化和安全性能的完美平衡,合理的材料与板厚的匹配显得尤为重要。基于以上原因,本文提出一种基于HyperMesh 12.0、Ls-dyna R7.1.1、iSIGHT5.8.3及MATLAB2014a的一种车身关键零部件材料板厚优化匹配的自动化方法。
模型描述
本文研究对象为某公司在研车型,其有限元模型及样车如图1所示。该模型包含771个部件,998,218个节点,974,383个壳单元(主要为四边形单元),4497个梁单元,19,314个实体单元,总重量为1263kg。
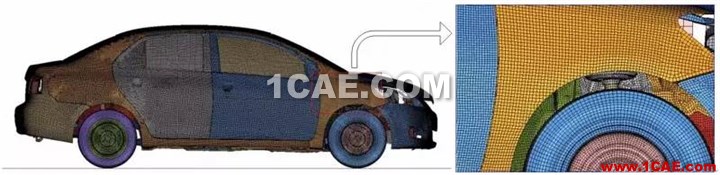
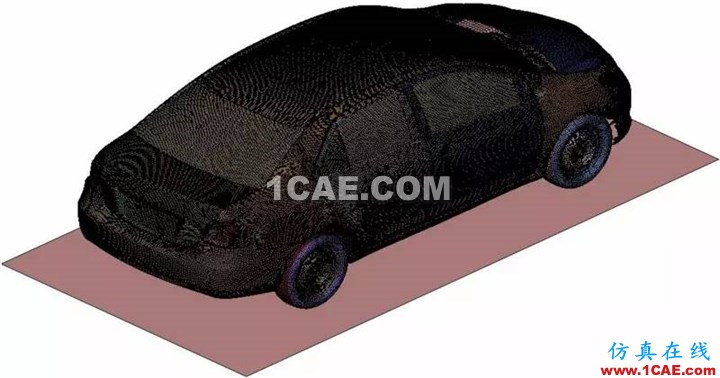
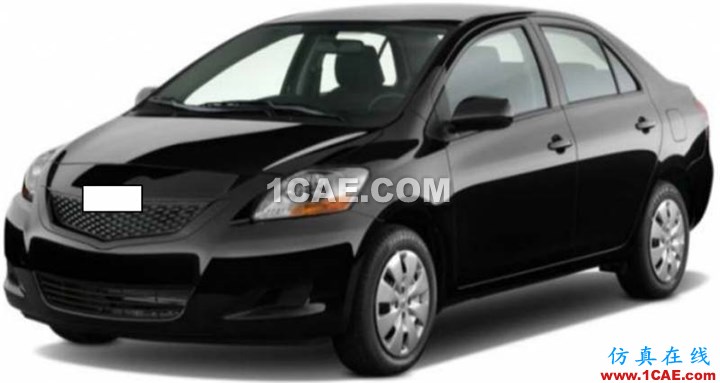
图1整车有限元模型及样车示意图
图3给出了车身仿真的加速度传感器的布置情况,详细位置为左右后座横梁及发动机上下。
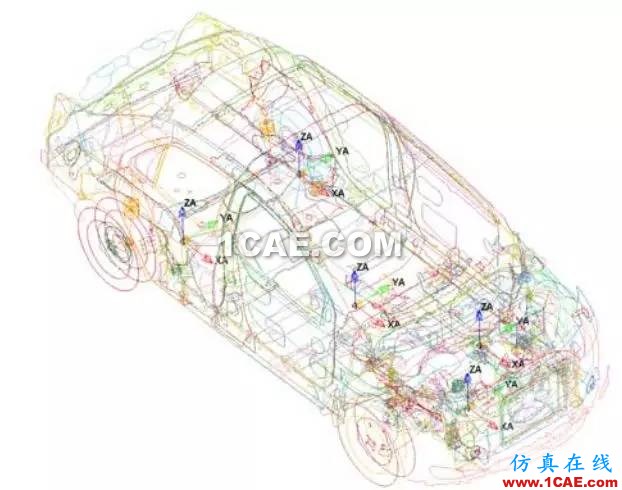
图2加速度传感器布置位置
图3给出了该模型在56.3km/h下的100%正面碰撞的试验测试结果。很明显,图3中变形模式、右后座速度及加速度曲线均与试验结果相吻合,以及图4总能量守恒状态良好,完全满足国标的要求,以上结果充分说明了该有限元模型的准确性。
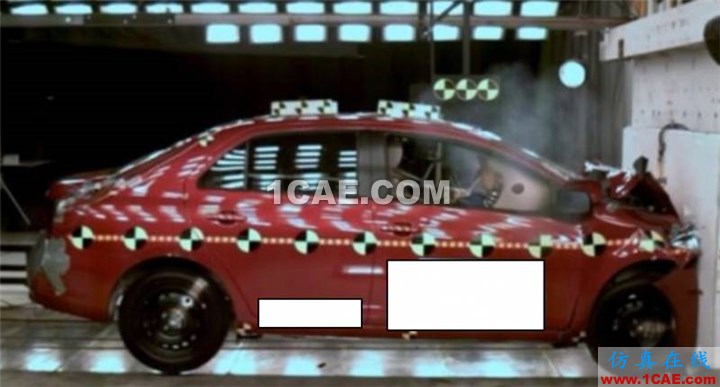
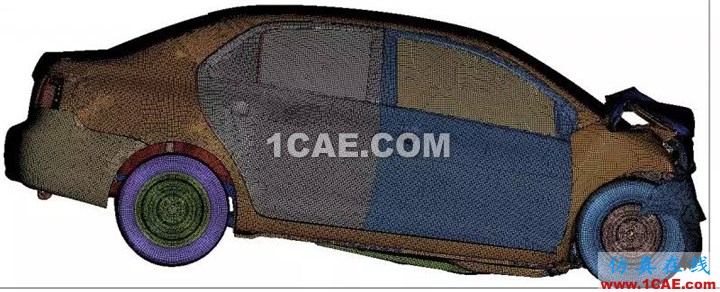
(a)试验和仿真的总体变形模式对比
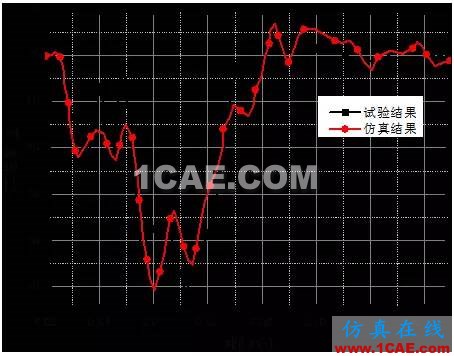
(b)右后座椅横梁加速度的试验和仿真结果对比
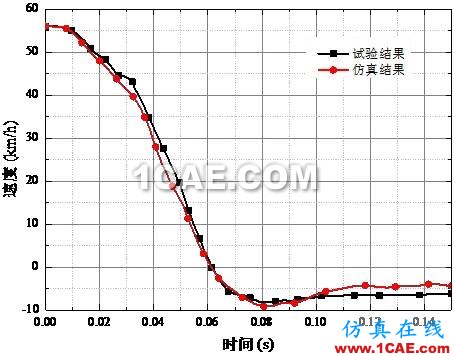
(c)右后座椅横梁速度的试验和仿真结果对比
图3试验结果及仿真结果的比较
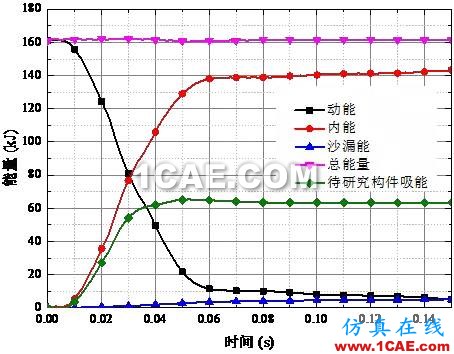
图4整车碰撞过程中能量变化历程
图5中所示保险杠、吸能盒及前纵梁在碰撞的0.08s时吸收能量占整车总吸能的46.8% (如图4所示),而总重量仅占整车重量的5.3%。以上数据充分说明了车身前端结构在整车碰撞安全中的重要作用。因此,本文选择车身前端结构总的保险杠、吸能盒及前纵梁为研究对象,通过组合使用HyperMesh 12.0、Ls-dyna R7.1.1、iSIGHT5.8.3及MATLAB2014a等工程软件,实现自动化的材料板厚优化匹配。
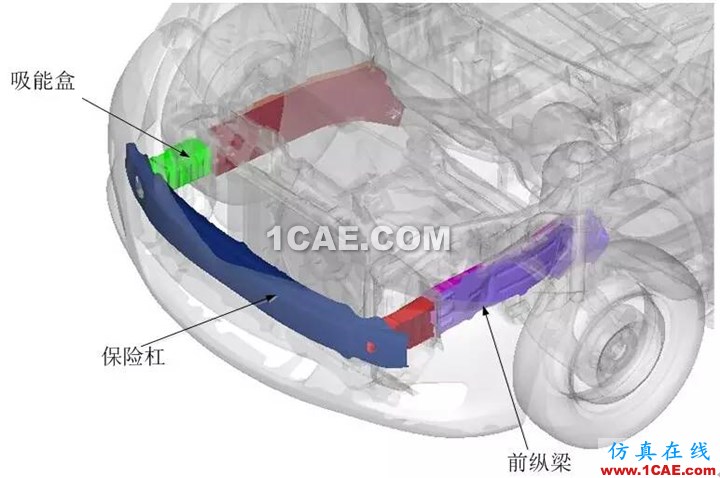
(a)车前前端结构
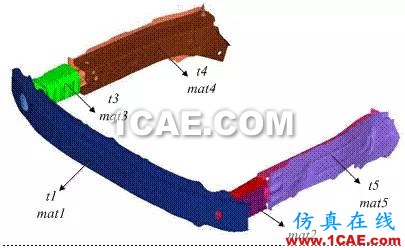
(b)前端结果设计变量
图5整车前端结构示意图
数学模型
数学模型:整车碰撞设计的目的为使结构尽量多的吸能能量、侵入量尽量减小、减速度峰值尽量低,以及重量尽量的轻。设计变量如图5(b)所示,主要为前端结构的材料及板厚。本文选取的结构响应如表2所示,初始设计如表1所示。
基于以上分析,本文的数学模型总结如下:
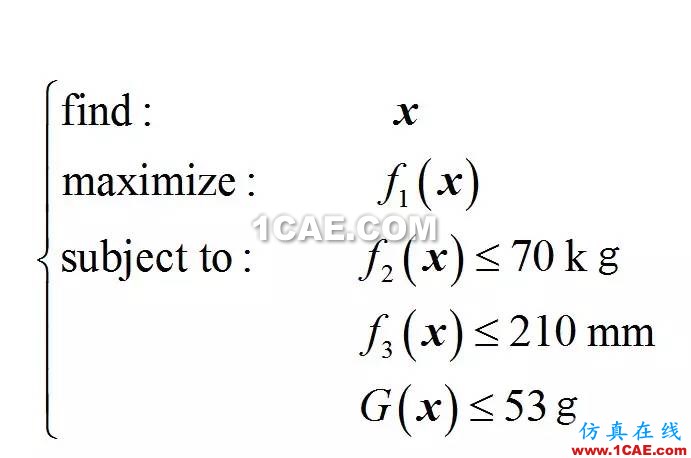
其中x = [x1, x2, x3, x4, x5, x6, x7, x8, x9, x10]T为设计变量,且具有以下离散备选值(如图5):

以上材料属性如下表2及图6所示:
表2 设计响应及其初始值
表3 备选材料属性
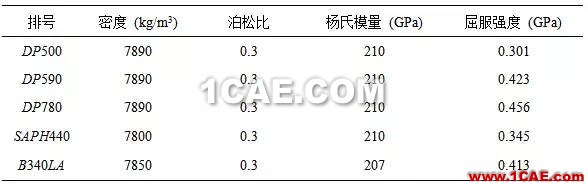
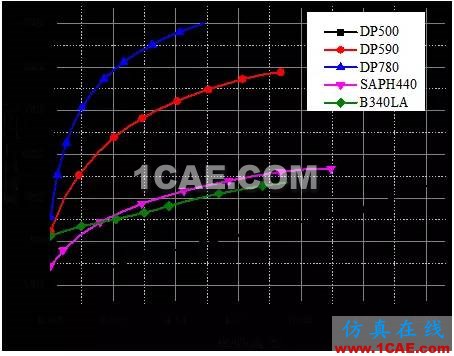
图6备选材料应力-应变曲线
以上首先使用HyperMesh 12.0建立模型,后续进行了试验验证,确保模型精度,为后续参数研究提供必要的条件。为求解上述优化问题,本文综合使用iSIGHT5.8.3、Ls-dyna R7.1.1及MATLAB2014a构建优化流程,如图7所示。其中优化算法采用模拟退火算法(Adaptive simulated annealing, ASA),LS-DYNA组件用于求解每次优化迭代中更新的k文件,MATLAB组件用于读取和换算LS-DYNA组件计算的结果。
在该自动化材料板厚匹配的计算方法中,难点在于如何在k文件中解析出设计变量,以及如何从计算结果中解析出需要的响应指标。本文中解析设计变量中对于板厚直接使用板厚数值作为解析目标,而对比材料在优化时解析材料对应的ID号作为设计变量,在优化过程中每种材料只调用其对应的ID即可,也即是设计备选的材料的ID在优化中是不变的,而每次迭代只是修改每个构件调用材料的ID来实现匹配不同材料的目的。在使用ASA优化时,对设计变量设置为允许的板厚和材料ID。
对于解析碰撞响应,本文中的响应主要为研究构件吸能及重量,前围板的最大侵入量和右后座椅横梁的加速度峰值。本自动化匹配流程中主要采用有include功能提取研究的车身前端结构,对关键响应构件建立set,以便在结果文件中直接读取所需响应结果。为了将计算响应转换为上述优化数学模型中的目标及约束,本文采用MATLAB编程实现数据的转换。
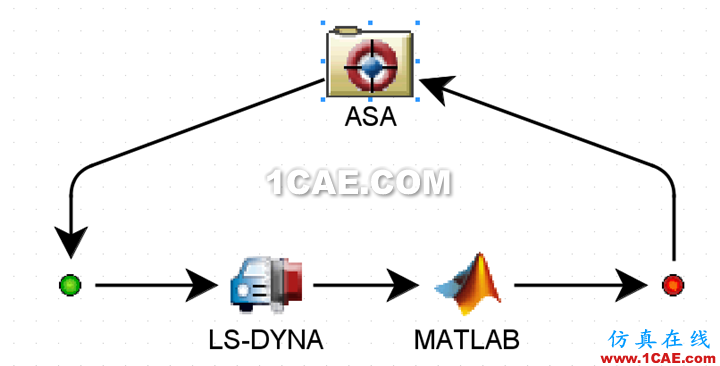
图7 自动化材料板厚优化匹配流程
通过上述优化方法获得优化结果如表4和5,由表可知最优结果使减速度降低了8.93%,侵入量减少了7.85%,吸能提升了15.33%及重量减轻了1.4%。对最优结果进行计算并与初始设计对比,如图8。由以上计算结果可知,本文中提出的基于HyperMesh 12.0、Ls-dyna R7.1.1、iSIGHT5.8.3及MATLAB2014a的一种车身关键零部件材料板厚优化匹配的自动化方法非常有效,而且该方法可以推广到更复杂的工程问题。
表4 最优设计变量

表5 最优响应与初始响应的对标

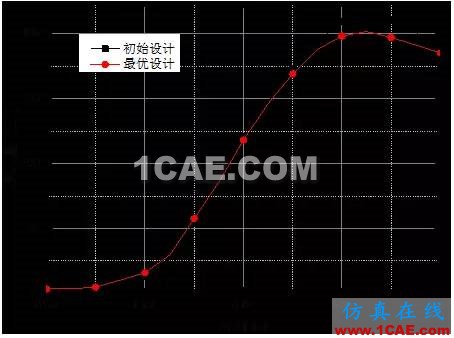
(a)前围板侵入量的初始设计与最优设计对比
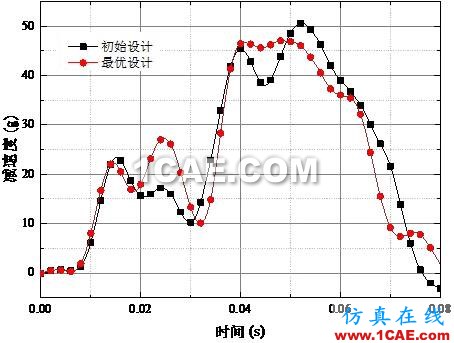
(b)右座椅横梁加速度的初始设计与最优设计对比
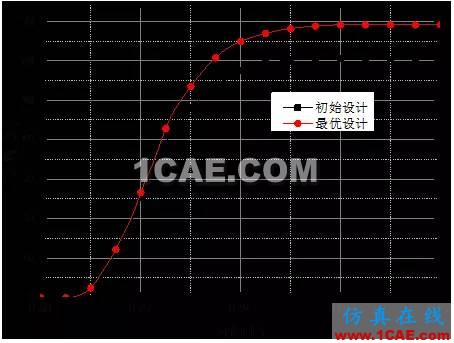
(c)结构吸能的初始设计与最优设计对比
图8最优设计与初始设计对比
项目经验EXPERIENCE
(1) 2014.09-2015.09:前纵梁轧制变厚板可靠性多工况设计(国家自科支持项目)
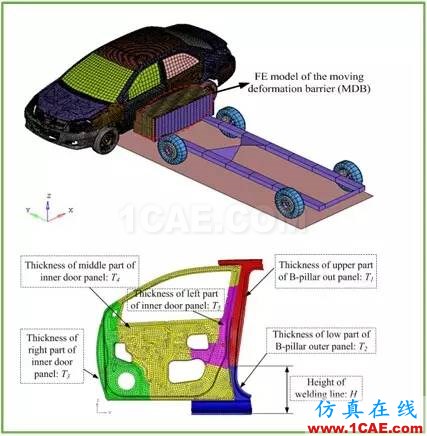
(2) 2015.12-2016.4:前纵梁轧制变厚板可靠性优化设计
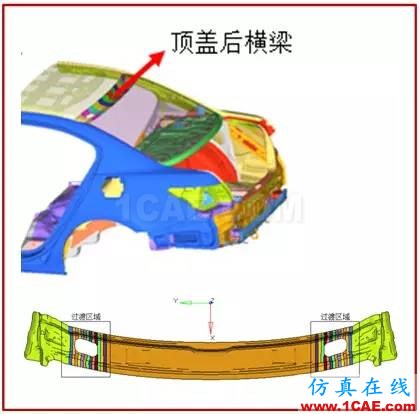
(3) 2014.5-2015.10:车身侧围结构拼焊板组合优化设计(校企合作项目)
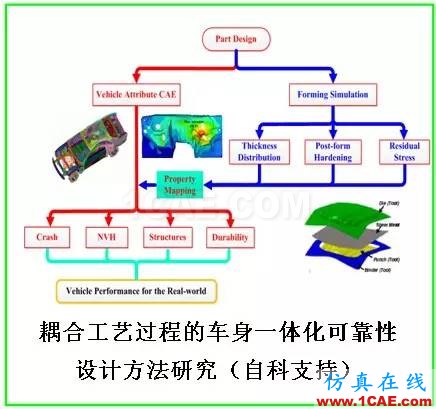
(4) 2015.9-至今:车身顶盖后横梁轧制变厚板稳健性设计
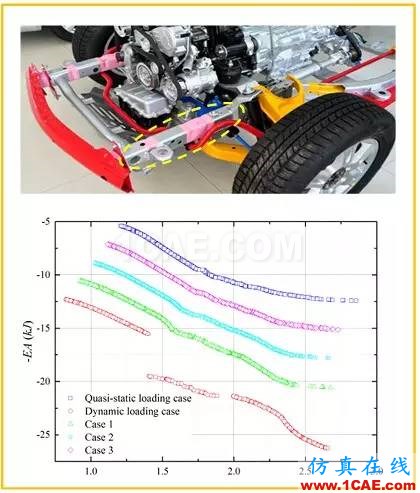
(5) 2015.9-至今:车身结构耦合工艺过程的一体化设计
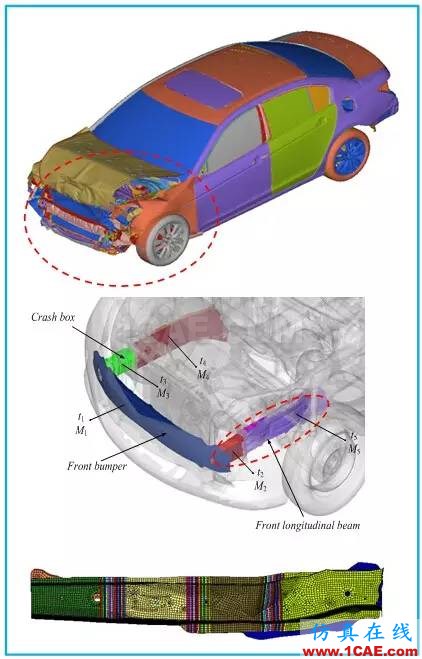
作者寄语MESSAGE
本人主要负责FEA模型的建立与试验验证、相关代理模型的构建与精度分析、优化算法的开发及实施等。希望能和汽车设计公司车身设计部门及车身设计爱好者合作,一起交流车身先进设计方法!
相关标签搜索:【作品展示7】车身关键零部件材料板厚优化匹配问题研究【转】 HyperWorks有限元分析培训 HyperMesh网格划分培训 hyperMesh视频教程 HyperWorks学习教程 HyperWorks培训教程 HyperWorks资料下载 HyperMesh代做 HyperMesh基础知识 Fluent、CFX流体分析 HFSS电磁分析 Ansys培训 Abaqus培训