CAE于发动机盖拓扑优化中的应用
2017-01-05 by:CAE仿真在线 来源:互联网
1 前言
发动机盖是车身中的关键部件,其性能直接影响了汽车的NVH性能、碰撞安全性能、防水性、门盖开启方便性及整车外观等。因此,对汽车发动机盖的模态,刚度、强度进行分析研究及优化显得很有必要。
本文通过有限元分析方法,利用HyperMesh建立有限元分析模型,采用OptiStruct求解器进行计算求解。通过分析结果对比,对不合格工况进行拓扑优化,并对最终优化后的结果进行性能检验。
2 模型概况
发动机盖总成以钣金件为主,在结构上一般由外板和内板组成,中间夹以隔热材料,内板起到增强刚性的作用,该总成还包括锁钩加强板,锁钩,铰链,铰链支座,铰链加强板。
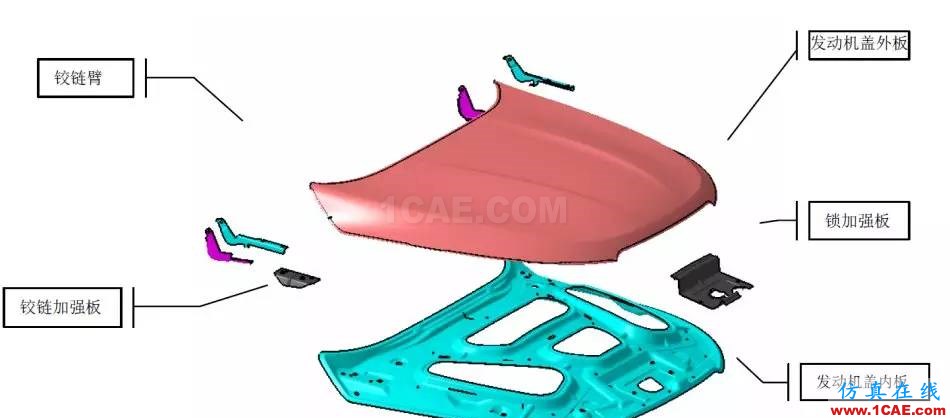
图1.1发动机盖有限元模型
有限元模型主要采用壳单元和实体单元进行建模:其中内板,外板,锁加强板,铰链,铰链支座,铰链加强板按10mm进行网格划分,壳单元总共34427个,锁钩划分为实体单元,因为锁钩尺寸比较小,按照3mm进行网格划分。发动机盖内外板的边缘通过包边处理实现连接;铰链固定在车身上,采用RBE2模拟螺栓连接,并约束六自由度使其固定;铰链座与铰链臂之间采用销轴连接,通过RBE2模拟螺栓连接,约束12346自由度,放开Y轴的旋转自由度5;铰链与内板的连接采用螺栓,通过RBE2单元进行模拟,约束123456自由度;内板与外板之间的胶连接,通过ACM单元模拟实现;铰链处的焊点采用CWELD单元模拟实现;锁钩与锁加强板之间是焊接关系,锁钩是体单元,为了更真实的模拟连接关系采用RBE2单元模拟实现;缓冲块采用弹簧SPRING单元实现,密封胶采用CBUSH单元模拟实现。发动机盖总成质量为17.48kg,模型的材料属性见表1.1,其中发动机盖总成结构有限元模型如图1.1所示。
表1.1 模型材料属性

3 模型分析
3.1模型计算及分析结果
模型检查无误之后,进行工况加载并计算。发动机盖的模型计算工况包括刚度、强度、模态、非线性分析等等十多种,读取计算结果与工况要求目标值进行比较:自由模态工况中的扭转模态为24.59HZ,小于合格目标值30HZ,不满足工况要求;扭转刚度为8750.70N·m/rad,略小于合格目标值9000N·m/rad,不满足工况要求;前乘坐工况的最大应力为183.19MPa,大于屈服应力,不满足工况要求;侧乘坐工况的最大应力为171.99MPa,与屈服应力非常接近;后乘坐工况的最大应力为209.39 MPa,大于屈服应力,不满足工况要求。
综上所述,自由模态的扭转模态、扭转刚度、乘坐(前乘坐、侧乘坐、后乘坐)强度、下拉强度等等工况的计算结果,不满足设计工况要求,需要进行结构优化。
3.2发动机盖内板结构优化分析
拓扑优化的研究领域主要分为连续体拓扑优化和离散结构拓扑优化。不论哪个领域,都要依赖于有限元方法。连续体拓扑优化是把优化空间的材料离散成有限个单元(壳单元或者体单元),离散结构拓扑优化是在设计空间内建立一个由有限个梁单元组成的基础结构,然后根据算法确定设计空间内单元的去留,保留下来的单元即构成最终的拓扑方案,从而实现拓扑优化。目前,连续体拓扑优化的研究已经较为成熟,主要有均匀化方法、变密度法、渐进结构优化法(ESO)以及水平集方法等。
由上面分析可知多种工况不满足设计要求,需要对发动机盖总成进行优化改进。对于发动机盖总成来说,外板及铰链的形状一般不可以改变,外板为空间曲面板,要迎合整车造型的需求,体现轿车的外形风格,结构优化的空间不大。内板为薄钢板,筋条网格状布置,其主体结构可根据需要布置孔洞,以减轻自身重量,内板的作用还包括:加强结构刚度、达到足够的抗凹性能及满足碰撞(行人保护)法规要求,此外兼顾加工工艺、轻量化、车身的防腐蚀和最低成本原则等方面的需要。
本文在保证发动机盖总成外板形状不变的情况下,采用变密度法对发动机盖内板及加强件进行拓扑优化。因发动机盖内板结构多种多样,对发动机盖的模态、刚度和其他性能的影响较大,这里仅考察内板结构优化设计对发动机盖总成模态、刚度和强度的性能提升影响。
优化分析步骤:
1) 设定约束
优化约束是在优化过程中必须满足的条件,为了保持发动机盖的性能,故需要约束。权衡计算速度,本文选取发动机盖自由扭转模态和扭转刚度作为优化约束,要求各优化约束指标均不低于原设计性能。本文中设定自由扭转模态固有频率最小为30HZ,扭转刚度为9000N·m/rad。
2) 设计变量
OptiStruct的拓扑优化过程采用变密度法。该方法假设材料的弹性模量与材料的密度为确定的数学关系,且每个设计单元的密度为一个优化变量。当优化结果表示设计单元的密度接近0,表示该单元弹性模量接近0,即该单元对考察的优化工况没有贡献,该单元应剔除;若密度越接近1,表示该单元的贡献量越大,该单元需要优先保留。在本文中因为内板的厚度为0.7mm,设置basethickness =0.7mm,内板的厚度在0.7-1.5mm之间变化。
3) 优化结果分析
通过HyperView进行后处理,并查看优化结果。设计单元的密度是该内板结构保留或增强的标志。密度越高,颜色越红,则说明该结构对所考察的工况越重要,反之,密度越低,颜色接近蓝色,则该结构对所考察的工况所起的作用越小。从密度分布图2.1中可以看出:内板的”A”字肋比较薄弱,需要进行加强改善以提高发动机盖总成的性能。
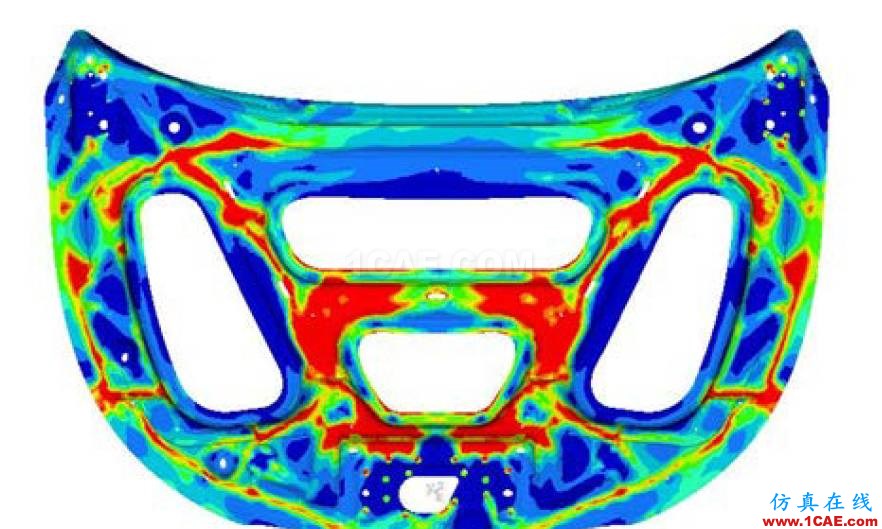
图2.1拓扑优化结果-内板密度效果图
3.3 优化方案
1)根据工艺要求,对于易引起大变动的结构部位或者是与其他总成的连接部位尽量维持原有设计,减少模具的改造成本,红黄蓝三线框图所示,例如:装焊安装孔,缓冲台,锁扣安装位置等等,见图2.2,对于这些部位稍有变动,会引起其他连接件的变动,涉及范围比较广,增加了经济成本,所以这些部位都维持原有的设计。
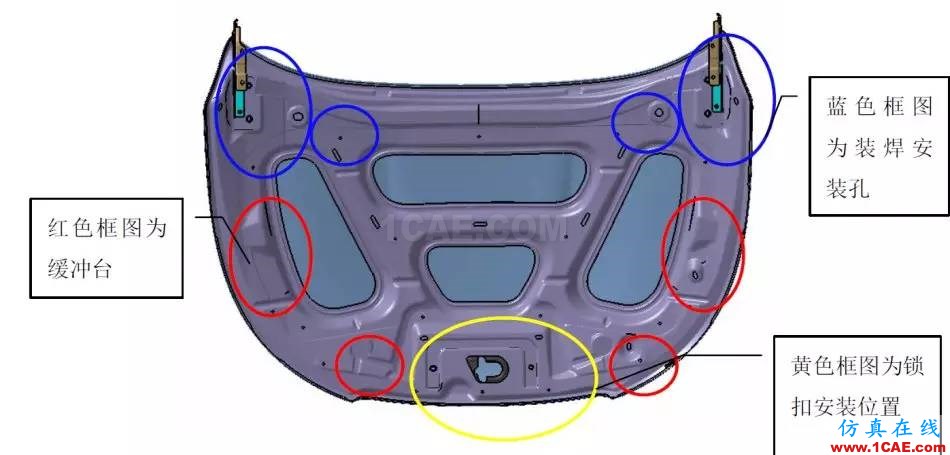
图2.2几何模型
2) 根据经验并参考优化结果,提出了两种改进方案:
方案一修改”A”字形的中间肋的结构,增加截面面积,增大垂向的倾斜度,见图2.3。
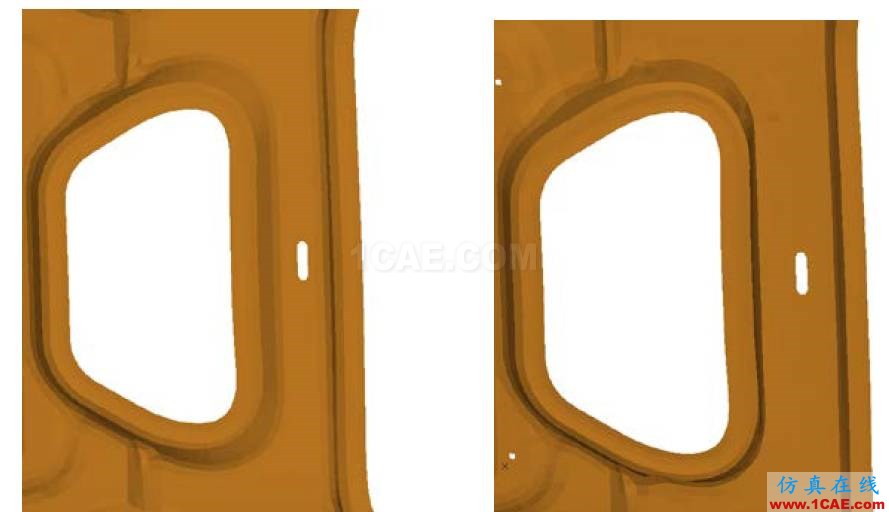
图2.3 方案一
方案一的计算结果:自由模态工况中的扭转模态为26.34HZ,小于合格目标值,不满足工况要求;扭转刚度为9260N·m/rad,略大于合格目标值,满足工况要求;前乘坐工况的最大应力为195.23MPa,大于屈服应力,不满足工况要求;侧乘坐工况的最大应力为107.43MPa,小于屈服应力,满足工况要求;后乘坐工况的最大应力为88.45MPa,小于屈服应力,满足工况要求。
方案二抬高如图2.4所示的两个部位,使“A”字形内板结构更加完整。
方案二的计算结果:自由模态工况中的扭转模态为30.04HZ,略大于合格目标值,满足工况要求;扭转刚度为11771.30N·m/rad,大于合格目标值,满足工况要求;前乘坐工况的最大应力为182.11MPa,略微大于材料承受的最大屈服应力,不满足工况要求;侧乘坐工况的最大应力为101.21MPa,小于屈服应力,满足工况要求;后乘坐工况的最大应力为86.42MPa,小于屈服应力,满足工况要求。

图2.4 方案二
综上所述,自由扭转模态均满足设计要求,前乘坐应力略大于目标值,而且前乘坐工况只是偶尔会发生的现象,在计算中也会存在误差,所以此处忽略前乘坐应力稍大的情况,方案二基本上满足设计要求。在满足设计要求的同时发动机盖总成的质量也没有增加,所以本文采用方案二的优化设计方案,至此优化结束。
相关标签搜索:CAE于发动机盖拓扑优化中的应用 HyperWorks有限元分析培训 HyperMesh网格划分培训 hyperMesh视频教程 HyperWorks学习教程 HyperWorks培训教程 HyperWorks资料下载 HyperMesh代做 HyperMesh基础知识 Fluent、CFX流体分析 HFSS电磁分析 Ansys培训 Abaqus培训