基于恶劣工况下的纯电动车碰撞安全仿真与评估
2017-01-05 by:CAE仿真在线 来源:互联网
摘要:电池模组的变形量是判断电动车碰撞安全的重要指标之一。本文基于HyperMesh建立整车有限元模型,通过引入Euro-NCAP侧面柱碰和FMVSS301高速后碰两种恶劣工况对某纯电动汽车进行碰撞仿真和评估。计算结果表明在恶劣工况下纯电动车电池模组变形量满足设计要求。通过引入更严苛工况对电动车碰撞安全进行评估的方法,这对国内建立更加完整的电动车安全碰撞体系具有重要的参考价值。
1 概述
随着世界环境污染和能源危机的双重压力下,新能源汽车的研发势在必行。而目前纯电动汽车、混合动力汽车发展最为迅速,电动汽车已然成为未来解决能源和环境危机的必然方向。但是,近年来纯电动车碰撞事故的频繁发生,无疑将电动车运行安全的课题再次推至聚光灯下。
目前我国只有GB/T18384.1、2、3-2001《电动汽车安全要求》三项涉及电动车安全的国家标准,但其中只有一项对碰撞安全提出要求且仅限于正面碰撞,标准低于燃油车。因此,在国内针对电动车的开发基本是参照GB11551-2003《乘用车正面碰撞的乘员保护》、GB20072-2006《乘用车后碰燃油系统安全要求》及C-NCAP评价规程等汽油车的标准,但碰撞事故的频繁发生表明,目前的碰撞标准很不利于电动车的乘员保护[2-3]。电动车最大的安全问题就是电池包和高压线路在碰撞发生时的安全问题。一方面国家碰撞标准对于纯电动车来说仍然较低,另一方面传统的电池挤压测试并不能完全替代实际中可能发生的碰撞测试。尤其是在车辆的侧面和后面部位易产生过大的变形,不能有效的保证电池包的完整性从而产生漏电、漏液以及起火等现象发生。因此,我们在电动车的开车过程中有必要引入更加严苛的工况用以评估电动车的碰撞安全性。
本文以满足GB20072后面碰撞及C-NCAP侧面碰撞标准的某纯电动汽车为对象,利用Altair公司HyperMesh软件建立了整车有限元模型, 并针对Euro-NCAP29km/h侧面柱碰及FMVSS30180km/h高速后碰两个恶劣工况进行仿真分析以评估在开发过程中电动车的碰撞安全性能。
2 有限元模型建立
本文主要利用HyperMesh软件建立纯电动车整车有限元模型,主要包括车身、闭合件、底盘和动力系统以及完整的电池包模型。在针对国内法规时,我们往往简化了电池包的建模,对电池包的评估往往是针对电池框架的整体变形。为此,我们在针对恶劣工况下的碰撞评估中,我们详细地将电池包内部电池模组进行了建模和连接,期望在碰撞中能够得到内部模组的变形情况,从而反映电池包的碰撞安全性。整个有限元模型共1576516个节点,2236025个单元,包括梁单元、壳单元、实体单元、弹簧和铰链等单元类型,如图1 所示。
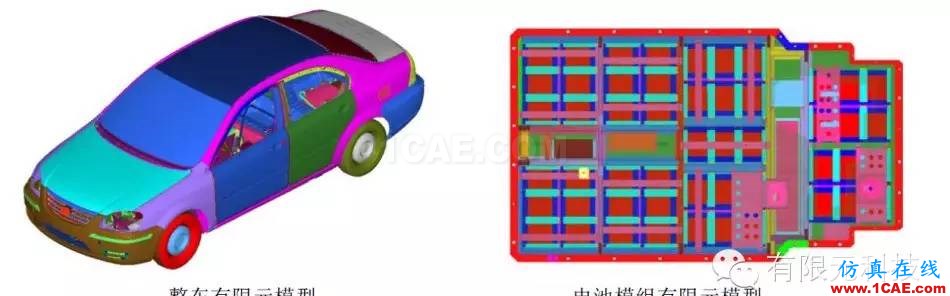
图 1整车及电池模组有限元模型
3 基于Euro-NCAP侧面柱碰工况纯电动车碰撞安全评估
3.1 有限元模型描述
纯电动车侧面结构及电池包布置空间如图2所示。
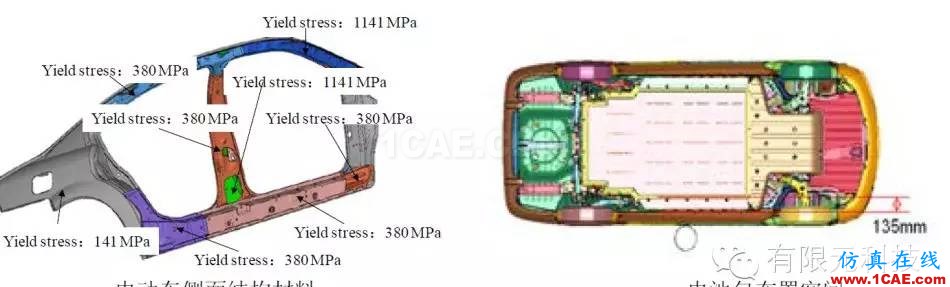
图 2电动车侧面结构及电池包布置空间
3.2边界条件和初始条件
Euro-NCAP侧面柱碰试验规定,整车处于静止状态放置在整备地面上,竖直固定放置一直径为254mm的刚性圆柱,在Z向,刚性柱最低点距离地面之间的距离不得超过102mm,上端超出顶盖最高点距离至少大于100mm。驾驶员假人的头部重心对准圆柱中心线,车辆以29km/h的速度撞击刚性圆柱。尽管撞柱碰撞速度只有29km/h,但对车身的要求很高,试验工况如图3所示。
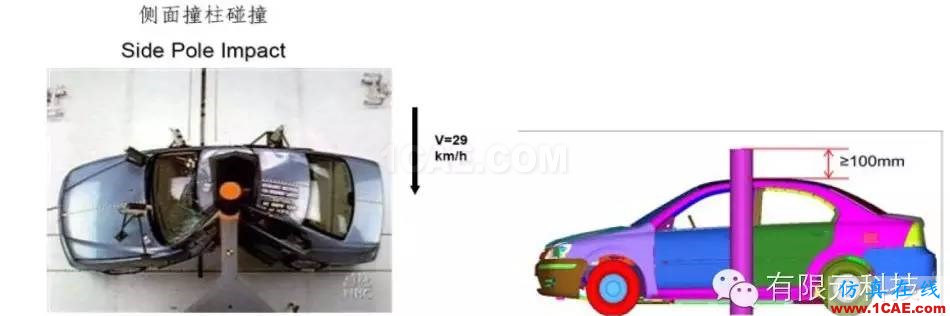
图3 Euro-NCAP侧面柱碰工况
3.3有限元仿真结果评估
从图4仿真结果显示车身结构稳定,刚性柱侧面侵入较小。电池包布置合理,从而规避了刚性柱的侵入空间。
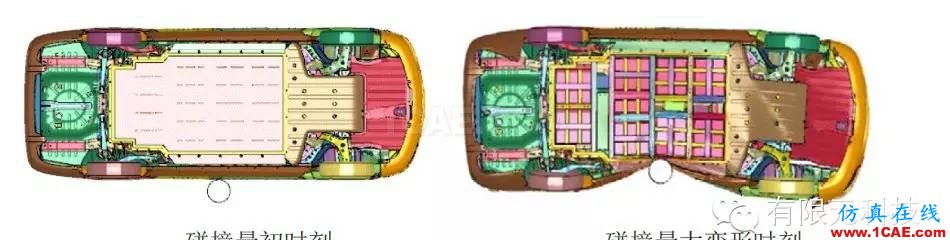
图4 侧面柱碰变形结果
内部电池模组从图5看,正对刚性柱的内部电池模组有较小位移,但无过大的挤压和结构侵入,在碰撞过程中不会造成发生漏电和电解液泄漏的情况。在撞击最严重时刻,模组之间最小间隙为1.5mm,单个模组最大变形为6mm,模组Y向宽度138mm,变形最大模组的Y向形变量为6mm/138mm=4.3%<30%。在合理的判定空间(针对模组单体)电池包压缩量小于30%,满足设计要求。
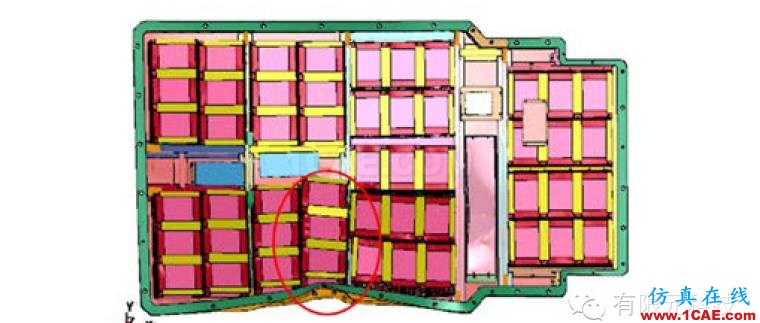
图5 内部电池模组变形结果(最大变形时刻)
4 基于FMVSS301高速后碰工况纯电动车碰撞安全评估
4.1 有限元模型描述
纯电动车后面结构及变形空间如图6所示。
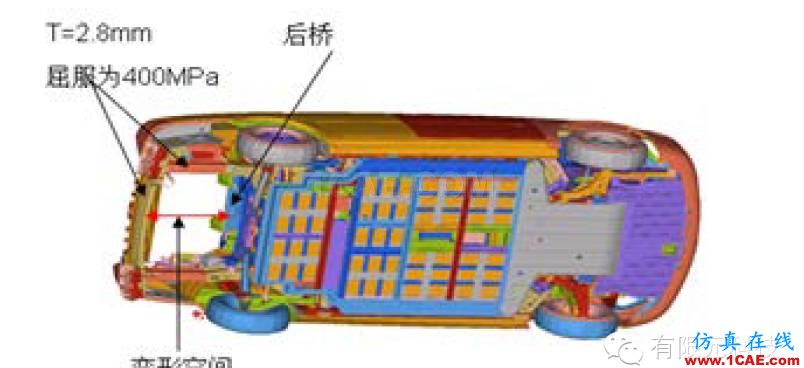
图6电动车后面结构及变形空间
4.2边界条件和初始条件
FMVSS 301《燃油系统的完整性》规定,整车本身处于静止水平地面上,使用FMVSS214中的台车,台车放置在与整车相同的地面上并将壁障高度降低50mm。后碰台车与整车有70%重叠并以80Km/h的速度撞击整车后部,台车可以偏向整车左侧或者右侧,试验工况如图7所示。

图7 FMVSS 301高速后碰工况
4.3有限元仿真结果评估
通过HyperView显示整车和电池模组变形结果,可以看出车身结构稳定,后纵梁尾段变形充分,变形形式合理,吸能良好且无硬物直接撞击到电池包,电池包整体变形较小,满足车体对电池包防护的要求,整车变形如图8所示。
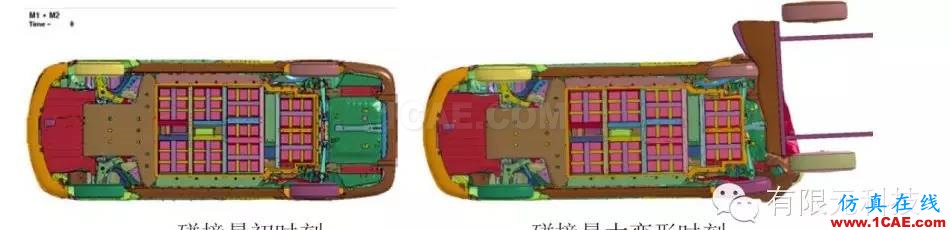
图8 FMVSS 301高速后碰仿真结果
而从内部电池模组来看,如图9所示,高速后碰下的内部电池模组有较小位移,但无后纵梁以及副车架等结构侵入的出现,因此在碰撞过程中不会造成发生漏电和电解液泄漏的情况。在撞击最严重时刻,模组之间最小间隙几乎未发生改变,单个模组最大变形为2mm,模组X向宽度133mm,变形最大模组的X方向形变量为2mm/133mm=1.5%<30%。在合理的判定空间(针对模组单体)电池包压缩量小于30%,满足设计要求。
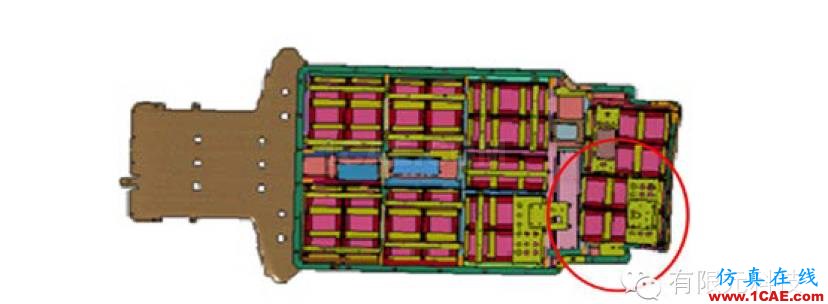
图9 内部电池模组仿真结果(最大变形时刻)
5 结论
本文以满足GB20072后面碰撞及C-NCAP侧面碰撞标准的某纯电动汽车为例,利用HyperMesh软件建立整车有限元模型,通过引用FMVSS301高速后碰和Euro-NCAP侧面柱碰这两个工况对纯电动汽车碰撞安全进行了仿真和评估,仿真结果显示,电动车在这两种恶劣工况下,电池模组的变形均满足设计要求,可以有效防止其侧面碰撞和高速追尾中发生漏电和电解液泄漏的情况的出现,从而在结构上避免起火现象的发生。
本文所提供的方法可以在电动车开发过程中,有效地评估电动车在恶劣工况下电池模组的变形量,提高电动汽车碰撞结构的安全性能。同时,这也对国内建立更加完整的电动车安全碰撞体系具有重要的参考价值。
相关标签搜索:基于恶劣工况下的纯电动车碰撞安全仿真与评估 HyperWorks有限元分析培训 HyperMesh网格划分培训 hyperMesh视频教程 HyperWorks学习教程 HyperWorks培训教程 HyperWorks资料下载 HyperMesh代做 HyperMesh基础知识 Fluent、CFX流体分析 HFSS电磁分析 Ansys培训 Abaqus培训