HyperWorks在汽车行李箱优化中的应用
2017-07-20 by:CAE仿真在线 来源:互联网
概述
近年来,随着CAE仿真技术的逐渐成熟,其高效率、低成本的优势被国内外汽车厂商青睐,成为汽车设计的不可或缺的主要手段。HyperWorks软件以其高性能、开放式有限单元前后处理器、强大的网格划分能力及提供几乎所有主流商业CAD系统和CAE求解器接口等诸多优点成为CAE技术广泛应用的工具。
本文针对某轿车行李箱在强度耐久试验中出现因行李箱刚性不足造成面板变形,导致行李箱盖锁扣发生偏移,难以关闭行李箱盖的问题展开结构强度分析工作。利用HyperWorks建立行李箱的有限元模型,通过OptiStruct求解器对结构强度进行分析,并提出结构整改建议,对比参考样车后采用最佳优化方案,最终实车通过强度耐久试验,满足设计要求。
1 建立有限元模型
1.1网格划分
首先利用HyperMesh前处理功能建立行李箱总成各结构件的有限元模型,选用壳单元,基本网格单元尺寸为5mm。结构连接采用RBE2、RBE3、粘胶、焊接单元,并充分考虑结构的具体特征如圆角、翻边、工艺孔等,对结构的简化处理不影响结构的强度分析结果。完成后的行李箱有限元模型网格数量共有73475个,其中三角形壳单元3476个,占4.7%。单元质量符合企业给定标准。行李箱有限元模型见图1。
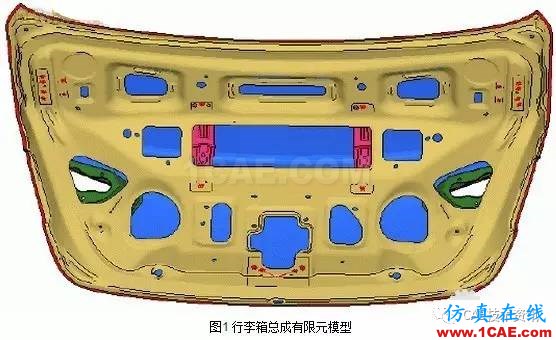
1.2材料属性
计算中所使用的材料参数如下:

1.3边界载荷
根据试验方法对行李箱盖进行约束和加载,具体方法如下:
约束条件:在行李箱盖铰链安装点处约束所有自由度,边界条件设置如图2。
载荷工况:在行李箱盖latch处施加力F=100N,方向为X向(车身前后方向),载荷设置如图3。
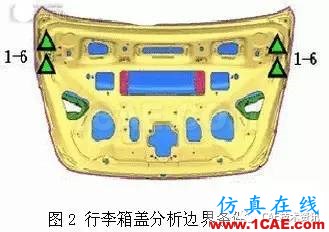
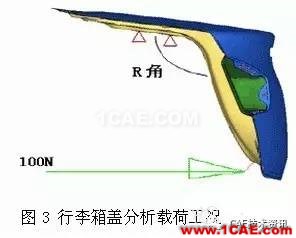
2 分析结果
通过OptiStruct求解计算出施力点的X方向位移值,体现出图2-3所示的R角的变化程度,反映行李箱盖的刚度特性。
分析结果得到该点的X向位移为4.94mm。为设定分析优化目标,特取一款类似的参考样车的行李箱盖做同样的工况分析,得出的位移值为4.4mm。因此,对该行李箱盖的结构强度优化目标,即在该载荷工况下,施力点的X向位移值≤4.4mm。
3 优化方案
根据经验,为提升行李箱盖的刚性,减少面板变形量,需加强行李箱盖内部R角折弯部位的刚度。因此,根据设计空间和成本考量,提出以下两种优化方案,并将分析结果与参考样车分析值进行对比,选取最佳方案。
方案一:在行李箱盖内板R角折弯部位添加凸筋。见图4。
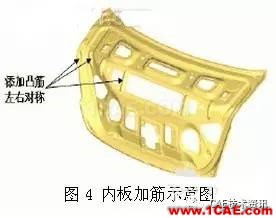
方案二:将行李箱盖左右铰链加强板加长。见图 5。
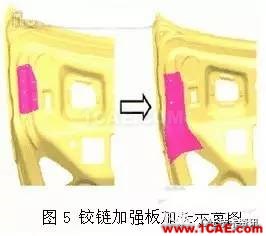
以上两种优化方案分析结果如下:
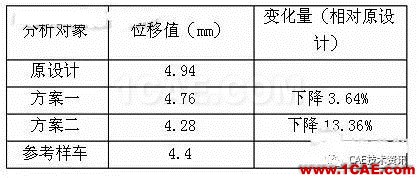
以上分析结果(图6 和图7)可以看出,方案一的施力点位移变化量略有减小,但未达到目标要求;而方案二的施力点位移变化量下降13.36%,到达4.28mm,低于目标4.4mm,说明该方案能够有效提高行李箱盖的内板刚性。
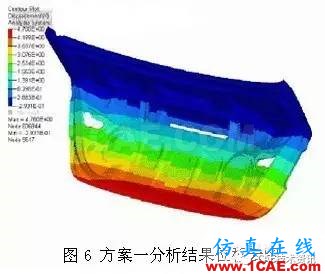
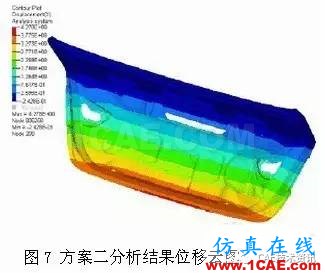
4 实车验证
根据方案二的建议,将行李箱盖左右铰链加强板加长后进行强度耐久试验测试,发现问题点已改善,不存在难以扣锁的问题。试验结果表明,优化方案二满足设计指标要求,达到了结构优化改进的目标。
5 结论
本文利用HyperWorks软件建立行李箱盖总成有限元模型,并对行李箱盖进行结构强度仿真分析。针对原先的设计问题点提出2种优化改进方案,对仿真结果进行对比分析,选取其中最佳的优化方案,并最终通过试验验证该结构优化改进是可行的。(转)
文章综合于网络,如有侵权请联系删除!
相关标签搜索:HyperWorks在汽车行李箱优化中的应用 HyperWorks有限元分析培训 HyperMesh网格划分培训 hyperMesh视频教程 HyperWorks学习教程 HyperWorks培训教程 HyperWorks资料下载 HyperMesh代做 HyperMesh基础知识 Fluent、CFX流体分析 HFSS电磁分析 Ansys培训 Abaqus培训