应对“时间就是市场”商业环境的压铸关键技术
2017-01-07 by:CAE仿真在线 来源:互联网
“时间就是市场” (Time To Market, TTM),对工业界而言,这是一个崭新而又永恒的话题,既是挑战,也是各大厂商的发展目标。随着社会的进步与经济的发展,这一主题将更为突出。例如,去年全球有500个新车型上市,平均2天就有一款新车呈现在您的面前。又如惠普公司,80%以上的利润来源于新近不超过两年的产品。所以,快速、高效地开发新产品是竞争取胜的一个关键因素。
和其他行业一样,铸造业也正经受着前所未有的挑战。归结起来,这种挑战主要体现在:
1. 人才短缺,且员工流失率高,这对压铸业的发展带來了严重的影响。以长三角、珠三角为例,这一带累计有近万台压铸机,对压铸人才需求极大。但技术人员流动性大,社会上又缺乏扎实的基础理论培训体系和机构,严重影响着技术人员水平的提升。
2. 企业普遍依赖于少数有经验的师傅。由于压铸技术参数难以控制,并互相影响,解决问题要靠经验累积,而目前高等院校有铸造专业的已经不多,而深入的压铸课程培训基本没有。
3. 压铸在职业竞争中并不具备太大优势,而且需要长时间培训,对年青人吸引力较低。
4. 对国际买家来说,中国是生产成本低的地区,适宜在此寻找平价产品;但对高要求的买家,他们会担心质量问题而选择其他区域。这种认识上的偏差,使得压铸产业一直在低水平徘徊,也阻碍了压铸产业的升级。
在未有大量的经验技术人才出现之时,系统化的计算机软件将是最有效而实用的工具,这不仅可建立一套模具设计及压铸技术的知识系统,同时亦可让新一代的技术人员及模具工程师更快地掌握。本文拟针对“时间就是市场”这一商业环境中的特点,对突破压铸企业所面临困境的有效关键技术进行讨论,并侧重在企业信息技术的应用方面。
1,产品可制造性评估
产品可制造性评估(Design For Manufacturing, DFM)是伴随“时间就是市场”和“质量就是市场(Quality For Market, QFM)”商业环境的直接产物。由于产品的实效性和高质量要求,所以必须在产品设计层面就加以把控。这种意义体现在最终产品的“舒畅制造”和价格优化上。
主机厂在设计的过程中,首要关注的是产品的功能与结构。但由于设计员经验和精力的局限,某些产品并未能充分考虑其可制造性,从而大大增加了工艺设计的难度。如果能从新产品的初步规划起,就展开DFM分析,通过全面的评估并及时修改产品设计,就能得到可制造的最佳设计方案,为一次设计即能生产制造提供了可能。这样,在提高产品质量的同时也缩短了开发周期。
然而,DFM分析所面临的问题也不言而喻。首先,高度依赖于工程师的经验,并且处于市场前端的往往是销售工程师,对制造工艺的了解非常有限;其次,缺乏必要的软件手段,目前存在的DFM软件寥寥无几,且基本上是以往制造数据是罗列,面临新产品则无从下手。再次,采用目前的三维CAD软件缺乏足够的分析能力,如只能手动切取横断面进行评估,不仅耗费时间精力也容易忽视一些重要的特征。最后,这种评估的模式往往需要在前端销售人员、产品报价人员和后端模具设计工程师中频繁交互讨论和修订,不仅效率低下而且在面临新客户时完全没有灵活性。
Geo-Designer 是Cast-Designer软件包中专为产品工程师和模具设计师设计的先端协同 DFM 分析工具。借助于 Geo-Designer产品工程师能在产品的设计阶段,考虑产品功能性的同时,也充分考虑可制造性,使设计成果迅速转化为批量生产。相比传统的工具与手段,Geo-Designer 提供了强大的分析功能,简便与快捷的操作模式,使用户通过改善设计阶段的质量而节省开发和生产成本。
Geo-Designer能快速、简单、准确地确定三维产品模型的关键区域,与产品需求进行比对,进而指导工艺设计。Geo-Designer能分析的内容包括铸件的基本信息(重量、体积、各方向投影面积)、质量分布检查、冷却速率分析、壁厚检查、浇冒口设计、拔模斜度分析、产品倒角探测、产品重量优化和EDM加工确认、热分布指数、顶出力大小分布、滑块检查等。而另一个非常突出的优点是,Geo-Designer非常容易使用,即使是销售人员和产品报价人员,也能轻松应对。
质量分布是工业设计中的一个重要关注点,产品厚度决定了零件关键区域的性能表现,无论从制造工艺、材料流动、还是零件强度与寿命都是如此。通常要获得理想的零件厚度对设计人员是一个很大的挑战,尤其是在设计与工艺频繁变更的过程中引起的厚度变化更是如此。更为复杂的是,在实际复杂产品中,产品厚度是一个三维的量,用质量分布(Mass Distribution)来表征更为合适。
下图显示了某个汽车零件的X光探伤图,显示了多处的“缩孔”缺陷,这些问题并不仅是来源于生产的制造链过程,如模具设计和产品压铸。其实早在产品的设计阶段,先天性的产品质量设计不良就埋下了隐患。由此可见,“更好的产品设计,是设计与制造出优质产品的源头”。
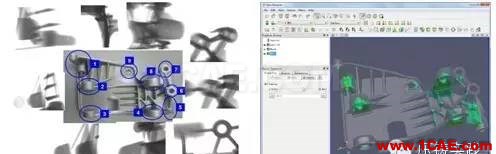
图一:产品的质量分布与Geo-Designer DFM预测的结果 (左图:X光探伤的照片 右图:Geo-Designer的质量分布指数, 整个分析过程只需要5分钟) (资料来源:通用汽车)
增强铸件的DFM评估,并非仅是主机厂的责任。对模具开发早期,也有着重要的意义。这些信息将直接影响到模具工艺设计的方案选择,例如确定内浇口的位置、设定第三相保压来消除缩孔、优化冷却管道排布(带走模具局部热量达到温度平衡)、预先设计局部挤压销等特殊模具结构来减少或消除缩孔缺陷、设定滑块和顶针的位置等等。
2,尽最大努力设计好流道
压铸产品的好坏,很大程度决定于流道设计。其进浇的方式、位置与排布、流道模式与尺寸等,都有着举足轻重的作用。流道设计的优劣,直接影响产品的生产性、缺陷与品质和生产效率。
2.1 专家系统的引入
“80%的产品质量问题,来源于工艺设计的好坏”,流道设计可以说是压铸模工艺设计中的核心部分。目前,流道设计仍然是一项依赖工程师经验的工作。工程师往往会运用书本上的一些经验公式,通过Excel表格等工具,计算出一些铸造的工艺参数。再通过三维CAD软件,完成造型设计。这种基于经验的设计,为铸造业带来前所未有的挑战。同时,现有的CAD软件只提供了三维造型能力,无法计算出设计所必须的铸造工艺参数,也不能把计算好的参数与CAD造型联动,更不能给出流道设计方案的建议。有鉴于此,引入流道设计专家系统,采取规范化设计非常必要。
CAST-DESIGNER是C3P Software针对压铸行业专门开发的压铸模流道设计分析系统。其内置了流道设计专家系统,并提出“基于工程经验的设计”概念,属于知识型(Knowledge-based)的设计产品。利用这个软件,三十分钟即可完成包括浇铸系统、溢流槽和排气系统以及冷却水道的设计。
图二是Cast-Designer流道设计的设计向导,通过输入铸件的基本信息(如重量、壁厚、材质等),程序将给出一系列的铸造工艺参数最佳建议数值,其中包括最佳充型时间范围、内浇口速度范围、内浇口面积与厚度等,用户可以直接采用或微调确认。在选择压铸机之后,能快速对一速、二速及临界切换点、整个流道的加速比等提供参数建议,并能实时调整,形成最后的截面积设计方案。最后通过PQ图对设计方案与压铸设备和模具进行即时校验,匹配出最佳的模具/设备组合。
对于复杂铸件,Cast-Designer有一个铸件分区设计功能,可以计算出每个内浇口的金属量和截面积以及金属流动距离,优化后能让整个充型过程更加平稳,避免金属液不平衡和包卷产生的缺陷。
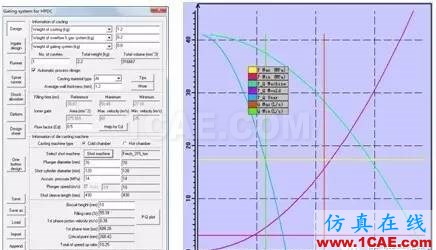
图二: Cast-Designer流道设计向导(左)和P-Q图用于实时校验设计方案(右)
2.2 基于经验的设计,是设计而非画图
理论上说,任何三维CAD软件(如CATIA, 西门子NX, Creo或PRO-E, SOLIDWORKS等)都能进行压铸模流道设计,但这些都是通用的CAD系统,功能强大但并不专业,特别是进行压铸模流道设计时非常费时费力且对使用者的要求很高。在企业中的应用状况是“一直在用但一直用不好”。
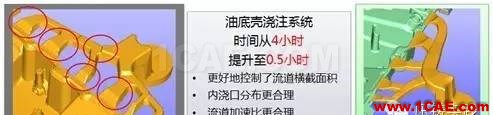
图三, CAD流道设计方法与Cast-Designer 流道设计的比较 (左图:采用Siemens NX/UG设计的流道,工程师具备4年设计经验,设计时间4小时,但横截面积控制并不合理; 右图:采用Cast-Designer设计的流道,工程师只有1年设计经验,设计时间只有半小时并能完美地控制流道截面积和加速比)
严格的讲,第一步的概念设计是在脑海里形成的而不是在电脑中完成的,这就是我们所说的草图或构思。草图设计是CAST-DESIGNER中一个比较有特色的功能,因为这种设计更接近自然中的设计模式。这里的草图并不是通常CAD软件中所谓的草图,而是真正意义上的草图,或者通俗的讲就是在草稿纸上画图。其作用原理大致如下:用户在使用CAD进行流道设计前,先在平面图纸上根据零件的二维视图或工程图大致钩画出流道的走向和大小,形成一个比较整体的布局,作为将来三维设计的参考。然后将草图扫描或拍照到电脑,再采用CAST-DESIGNER转化为矢量图,进行后续的设计。这种方法是值得推崇的,特别是对比较复杂的零件。日常工作中,我们也经常需要几个工程师一起商量设计原则并确定方案,而纸质讨论无疑是最有效和最便捷的。
另外一个可圈可点的亮点是一键式流道设计功能,这是Cast-Designer的一个独立设计模块,也可以说是完成了几代人的梦想。一键式流道设计事实上就是利用经验知识库进行设计,把常用的流道进行分类并形成经验知识库,然后数字化,以后碰到类似的产品即可直接调用,这样充分借鉴了以往的设计经验并大大缩短了设计和操作的时间。采用这种模式,往往几分钟就可以看到一个设计的雏形,在对工程设计上是梦寐以求的。Cast-Designer中特别设立了一种特别的语言CDGL支持客户定制,用户可以无限扩充。
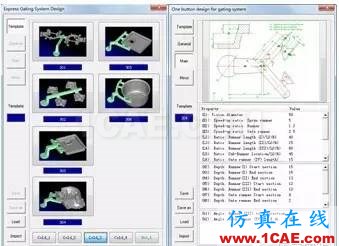
图四, Cast-Designer内置的一键式流道设计模板
2.3 反复比对并择优选取设计方案才有进步
任何一个设计,要获得优秀的结果,必须在多个方案中反复比较并择优选取。Cast-Designer提供诸多便利和快捷的设计手段。目的在与将用户从繁琐的CAD画图中解放出来思索更多更好的设计。从而防止永远局限在一个方案的禁锢中。
此外,采用这类属于知识型(Knowledge-based)的产品,不仅能在较短的时间内设计出专业的浇注系统直接为设计和生产服务,对企业而言既是一个培训的过程也是一个累积的过程。长期地使用这类系统,能为企业累积和建立一套标准化的设计规则,逐渐摆脱对人的过分依赖。
3,采用前端分析技术进行方案评估
即使是采用专家系统指导下设计的流道系统,仍有必要进行即一步的分析和评估,因为经验数据也好,专家系统也罢都是基于有限度的样本进行归纳总结的,而新的产品与这些样本想必总存在这样那样的差别。在进一步的分析方法中,其中一种行之有效的方法就是现代的CAE技术。
3.1采用前端分析的工业需求与迫切性
在当今的工业企业中,CAD与CAE技术已经不再是陌生的名词。事实证明,在设计阶段,经过充分的验证,可减少模具制造并投入生产之后才出现的产品缺陷问题。因此,许多的企业都已经相继引入了各种商业模拟软件并应用到实际的工作流程中,期盼节约成本,缩短周期。但很快就会发现,从三维数模开始,网格划分建立分析模型,到最后获得分析结果,需要2~3天的时间。如果设计方案需要变更,分析就要花1周以上的时间了,还没有等结果出来,模具都开好了。这就失去了预测和指导方案修改的意义了。
传统CAE软件产品的开发大都起源于上世纪90年代,当时的商业环境和今天并不一样,当时的信息技术与环境也和今天大不相同。所以大多数CAE软件的精力集中在功能开发上,而对用户的使用观感和使用效率上则基本不予重视。
面对“时间就是市场”的挑战,传统的CAE分析已经无法满足大部分企业对开模时间的要求。所以,普遍只用于不容有失的核心模具开发中,或者是上游厂商强烈要求CAE分析报告的时候,才应付了事。更有甚者,则沦为摆设,多年不用。
前端分析技术是最近几年在全球广泛使用的热门应用,其美妙之处在于能在产品和模具设计的初期,如概念设计阶段迅速地提供有效的分析结果和改进指导。因为在这一阶段,需要测试的设计思路和方案很多,一种快速而有效的工具就显得尤为重要。事实上在这一阶段,对分析结果的精确度虽有要求并非特别苛刻,因为许多因素还无法完全确定,相比之下,分析效率则显得非常关键。这也是在没有前端分析技术之前工业界采用传统的数值模拟方法却并不能非常有效地解决这一阶段问题的根源所在。
前端分析与传统的CAE分析的任务与目的并不完全相同,更不是传统CAE分析的简化,下表给出了压铸设计中前端分析与传统CAE分析各个阶段的对照。
工作起点
(Start point) 建模时间
(Modeling) 分析时间
(Analysis time) 结果精确度
(Result accuracy)
传统CAE分析方法 近乎完美的三维CAD数据,包含浇注系统、溢流槽、冷却系统甚至是完整的模具,对CAD数据质量要求较高。 耗时较长且复杂,必须经过专门培训。CAD清理、建立网格和设置分析模型并非易事。设置计算模型还需要更多的物理参数与热学条件,有些参数获得并不容易。 很长!根据模型大小,通常需要几小时到十几个小时,有时甚至几天的时间。对计算机的要求很高。 可获得相对较高的计算精度,前提是输入的各项参数正确。但设置正确的参数经验性很强,而且需要反复测试和校验。结果丰富(如温度场、流动场、应力场等)
前端分析方法 只需要铸件的三维CAD数据。可采用快速流道系统建立浇注系统、溢流槽和冷却系统等。同时也可接受STL数据格式。对原始数据质量要求较低。可以边分析边修改CAD数据。 非常简便和快速。几分钟内可对任何复杂或不干净的模型完成网格划分。设置计算条件非常简便,几分钟即可完成所有设置并完全参数化。无需特别培训。非常快!30分钟到一个半小时即可获得分析结果。 能获得合理精度的充填和凝固分析结果,完全满足前期设计与方案选择阶段的精度需求。获得的结果同样丰富(如温度场、流动场、应力场等)。
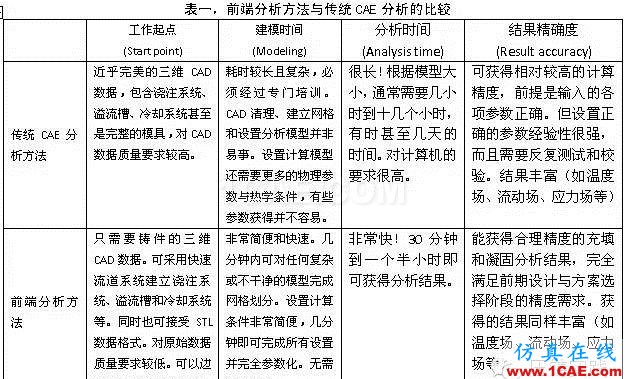
3.2技术手段:有限元分析技术
计算力学业已在应用中逐步形成自己的理论和方法。有限元法(FEM)和有限差分方法(FDM/FVM)是比较有代表性的方法,这两种方法各有自己的特点和适用范围。有限元法主要应用于固体力学,有限差分方法先前则主要应用于流体力学。但近年来这种状况已发生变化,它们正在互相交叉和渗透,特别是有限元法在流体力学中的应用日趋广泛。
有限元法和有限差分方法的区别是有限元法的函数是变化的,计算比较复杂的情况,计算量比较大;而有限差分方法的函数是不变的,计算通过变步长来实现,计算比较简单的情况,计算量比较的小。从功能上看,许多铸造软件大都基于有限差分法,可以对砂型铸造、金属型铸造、精密铸造、压力铸造等多种工艺进行温度场、流场的数值模拟,并可以预测铸件的缩孔、缩松等缺陷,但对应力场的模拟及裂纹的预测显得力不从心。
从压铸分析的角度来看,采用有限元分析方法是具有巨大优越性的:
1) 压铸件几何形状复杂,且多为薄壁件,有限元分析方法能进行更好的几何表征;
2) 有限元分析方法能够进行流场、温度场、应力场的三场耦合计算。与有限差分法(FDM)相比,进行应力计算时,无需使用两套网格和网格映射。有限元法具有较大的灵活性,特别适用于模拟复杂铸件成型过程中的各种物理现象。
3) 采用有限元方法能使用混合网格技术,且容许较大的元素大小比值,这样有利于优化模型大小,获得较高的有效模拟比(铸件元素数/整体模型元素数),从而提高模拟效率。比如说,在有限差分元方法中,考虑整个模具的网格数通常在千万数量级,而在同等精度下,有限元模型可以降低到近百万到一两百万的数量。这样不仅计算时间要节省,而且避免了庞大模型所造成的后处理困境。
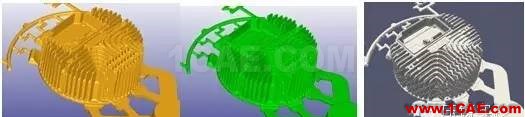
图五, FEM网格与FDM网格分析技术的比较 (左图)3D CAD几何 (中图)Cast-Designer FEM网格,网格数301,510 (右图) FDM网格,网格数in 4,803,845.
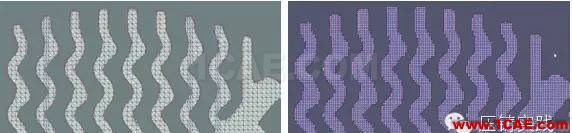
图六, FEM网格与FDM网格分析技术的比较, 切面图。红线表示CAD几何轮廓(参考基准),蓝色线条代表网格。左图,Cast-Designer FEM网格,整体网格数301,510。即使采用比较稀疏的网格,仍能非常优秀地表征几何。右图:FDM网格,整体网格数4,803,845。即使采用非常密集的网格,仍可明显看出其对CAD的表征欠佳。
诚然,有限元法在具备巨大优越性的同时也伴随着诸多的挑战。其中一个最大的挑战就是网格划分特别是复杂网格的装配。许多有限元分析的软件都是因为这一瓶颈未能突破而功败垂成。
3.3几何数据兼容性与网格技术
如上所述,网格划分在有限元铸造分析中是一个瓶颈问题和难点,能否攻克这一问题和最终实施是否便利是软件产品能否真正为工业服务的关键。
通过长期的研究和探索,Cast-Designer成功地开发了一种全新的网格技术,将传统的非随形网格和随形网格划分手段巧妙地结合在一起,形成了独一无二的网格划分模式。其主要特点有:
1) 几何相容性高。能接受各种原始几何数据,如三维实体CAD数据,STL数据或CAD实体与STL的混合数据。由于制造链本身的原因,模具制造企业往往获得的是OEM厂商的转化数据,不可避免地会发生数据丢失或不完整。 在这方面, Cast-Designer表现出惊人的相容性。即使原始数据不完整或有所丢失,内置的几何核心都能全自动的重构拓扑结构并进行修复和还原。
2) 自动几何跟踪和网格映射。为了追求几何的完美和准确表述,Cast-Designer内置了独特的几何跟踪技术和网格映射技术,这样,即使采用简单的网格,也能非常完美的进行几何表征。
3) 混合网格与全自动网格装配技术。通过采用混合网格,能大大提高模型的计算效率。在Cast-Designer中,支持六面体元素,三棱柱元素和三棱锥元素,这样可以对铸件采取六面体网格或三棱锥网格,而对模具则采取能结束较大元素比的三棱锥网格。比如图七中的例子就非常有效率。
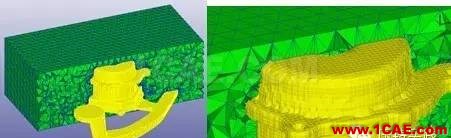
图七, Cast-Designer中的混合网格技术
同样,这种技术也可以应用在全套模具的网格装配上。用户定义模具的各个组件后,系统就能全自动的进行网格装配,包括铸件,动模,定模,滑块,水道和其他附属结构。这种功能具有非常高的技术水准,以前这样的工作往往需要数天甚至数周的纯手工作业,现在一个简单的按钮就完成了。当然,这中操作对机器的要求也比较高,通常8G的内存是标准配置。
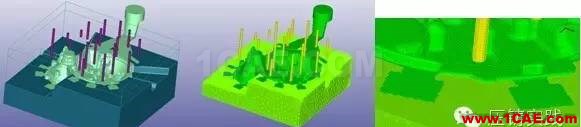
图八, Cast-Designer中网格装配技术
左图:整套模具的三维CAD几何 中图:Cast-Designer 划分的各部件网格并进行了自动装配。其中铸件采用六面体网格,网格数240,788个元素。定模包括 750,200 个三棱锥元素,动模包括 682,000个三棱锥元素。 右图: 显示局部的铸件与模具的网格连接关系。
4) 此外,还有一些专门针对铸造和压铸的网格技术。如局部网格技术用于保护复杂的高曲率或薄壁几何特征;自动分层技术保障流动模拟的顺畅性;自动网格质量检查与修复用于控制网格的质量等。
3.4 CAD驱动模拟分析
CAE模拟技术是分析验证的核心,包括充填模拟,凝固模拟和应力变形模拟。但这方面已经有非常成熟的技术和诸多的论述,限于篇幅,本文不再重复。
在应对“时间就是市场”的分析模拟中,还有一项非常重要的技术就是CAD驱动模拟分析。由于铸造产品可能随着客户的需求而进行各种微调与改变,如果每一改变都要用户进行一次全新的建模和模拟,则还是非常繁琐。Cast-Designer有一个特殊的MCAD模块,可以直接挂在现有的CAD系统中,采用独特的技术将CAE流动分析、热传导和凝固分析完全集成在客户现有的MCAD用户环境中, 让产品设计师、模具设计师在第一时间同时参与到工程决策中来。
这种全集成系统的优点在于,可以让你的CAD几何数据直接驱动整个模拟过程。当你在CAD环境中(如NX, Creo或SolidWorks中)对几何进行了修改, 只需一个按键和数十秒钟的等待,你的CAE模型也就相应地进行了修改。从而可以直接提交求解器进行模拟分析。
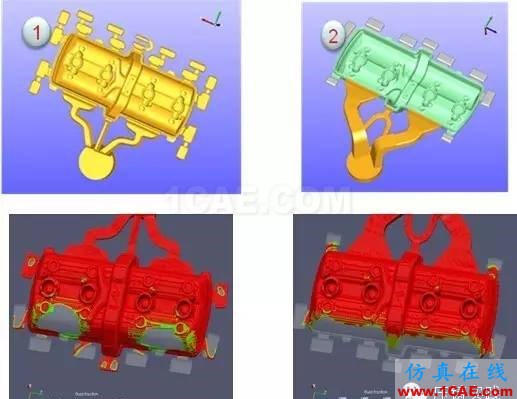
图九, 采用Cast-Designer的流道设计与分析系统进行方案对比
4,重视从产品,到设计到整个制造链的系统工程
除以上提到的DFM分析,流道设计与方案验证等技术外,在铸造过程中牵涉的其他技术还很多。特别是在设计阶段就对整个制造链有严重影响的一些因素,限于篇幅,本文抽取其中的几点进行简单的说明。
4.1快速冷却系统设计和生产周期评估
冷却系统在铸件生产过程中,发挥非常关键的作用。其设计的好坏会直接影响产品的品质(如缩孔疏松和应力变形等),也直接影响生产效率。而且,冷却水道一旦被加工好后,修改非常困难,传统的物理试错方式,难以获得平衡的温度及冷却效率。数值模拟能预测冷却系统对热的影响,但建模与分析都过于繁琐且需时太长,对实际设计指导意义不大。Cast-Designer中有一个专门的冷却系统设计和快速分析模块,为冷却系统的设计提供专业的建议,仅需几分钟到十几分钟即可对冷却效率进行详尽的检查与评估。
4.2产品变形与应力分析
对于薄壁件或超薄件,铸件变形是不可忽视的,也是工程师最头痛的问题。为了在铸造过程中有效分析预测裂纹倾向、变形和残余应力,从而为铸造工艺设计人员提供改进、优化工艺的科学依据,保证铸件尺寸精度及稳定性,提高铸件质量, 对铸件进行应力和变形分析是非常必要的。
利用有限元技术,能轻松完成耦合计算,包括热、流动和应力。应力分析包括了热应力和机械应力。采用应力分析可以分析出残余应力、塑性变形、热裂和铸件最终形状等。
对于一些非常复杂几何的铸造,在以上应力和变形的基础上还可以提出变形补偿,通过逐步迭代的方式求出预先的几何形状。
4.3产品寿命与耦合分析
对于一些质量要求很高的产品,耦合分析是必要的,比如铸造缺陷对产品寿命和碰撞性能的影响。这样,可以采用铸造模拟软件对铸造过程中的卷气、缩孔和应力等进行分析,并将铸造产品的缺陷与应力信息传输给其他结构分析软件进行产品性能的进一步评估。一般而言,缩孔等宏观缺陷较铸造应力的影响更大。在软件上,这要求软件具有非常完备的数据接口和协同分析能力。
5,结论与建议
面对日新月异的市场变化,汽车、3C和各种消费产品的更新换代非常迅速,产品外观也越来越时尚和复杂,如何在有限的设计周期内,获得高质量的设计,成了一线厂家的制胜之道。而要达到这一目标,除了要有丰富的设计经验外,也要依靠科学的工具。
在产品设计阶段,我们如何有效地提前进入进行协同设计和制造性评估是顺畅将来设计和铸造的关键;在模具设计阶段,我们如何进行整个流道方案的设计,通过控制入水方式与位置、流道横截面积、调整溢流槽的排布达到我们预想的流动状态和消除缺陷;应用前端设计分析技术的意义在于,从流道的快速设计,到铸造过程的模拟预测,再到方案修改,都能把控在1到2个小时内。这样,我们几乎能在一个工作日内,完成4到5个流道方案的评估,从中确定最优的设计方案。
相关标签搜索:应对“时间就是市场”商业环境的压铸关键技术 机械设计培训课程 基于数字方式的制造业升级 工业4.0 中国制造2025 CAD CAM自动化智能化机械制造的应用 Fluent、CFX流体分析 HFSS电磁分析 Ansys培训 Abaqus培训 Autoform培训 有限元培训